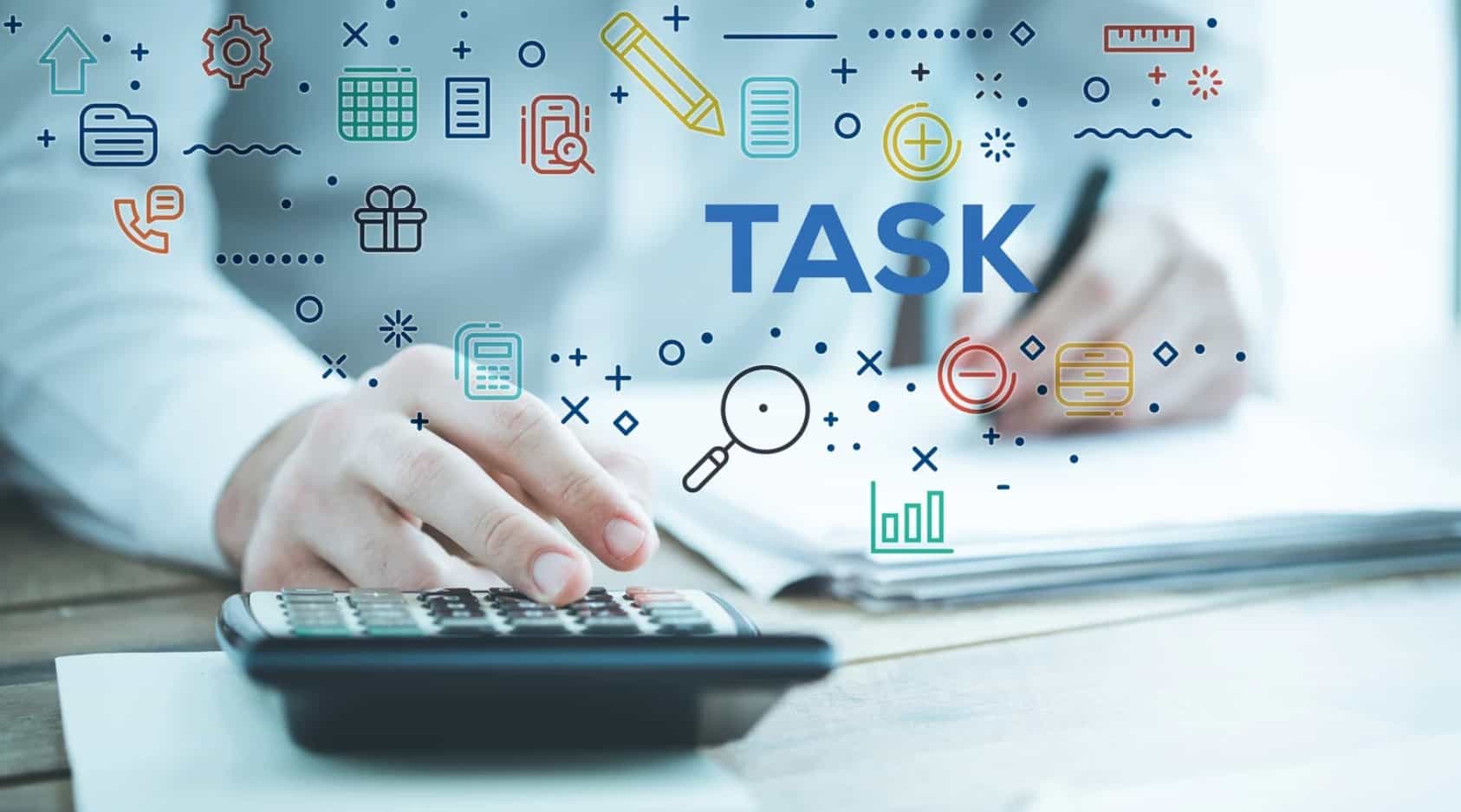
In the corner office of a manufacturing plant, a skilled engineer spends three hours every Monday manually entering quality control data into spreadsheets. Down the hall, a procurement specialist dedicates her Thursday afternoons to copying purchase order information from emails into the ERP system. Meanwhile, an operations manager at another facility stays late twice a month, painstakingly compiling production reports from multiple systems.
They're not lazy. They're trapped.
Trapped by invisible manual tasks that have been baked into workflows for so long they've become part of the company's operational DNA. These employees aren't doing what you hired them for. They're performing work that robots—or more accurately, intelligent automation—should be handling. And you're paying premium human rates for it.
The cost isn't just financial. It's the opportunity cost of what these talented individuals could be doing instead. The engineer could be improving production processes. The procurement specialist could be negotiating better supplier terms. The operations manager could be mentoring his team or strategizing efficiency improvements.
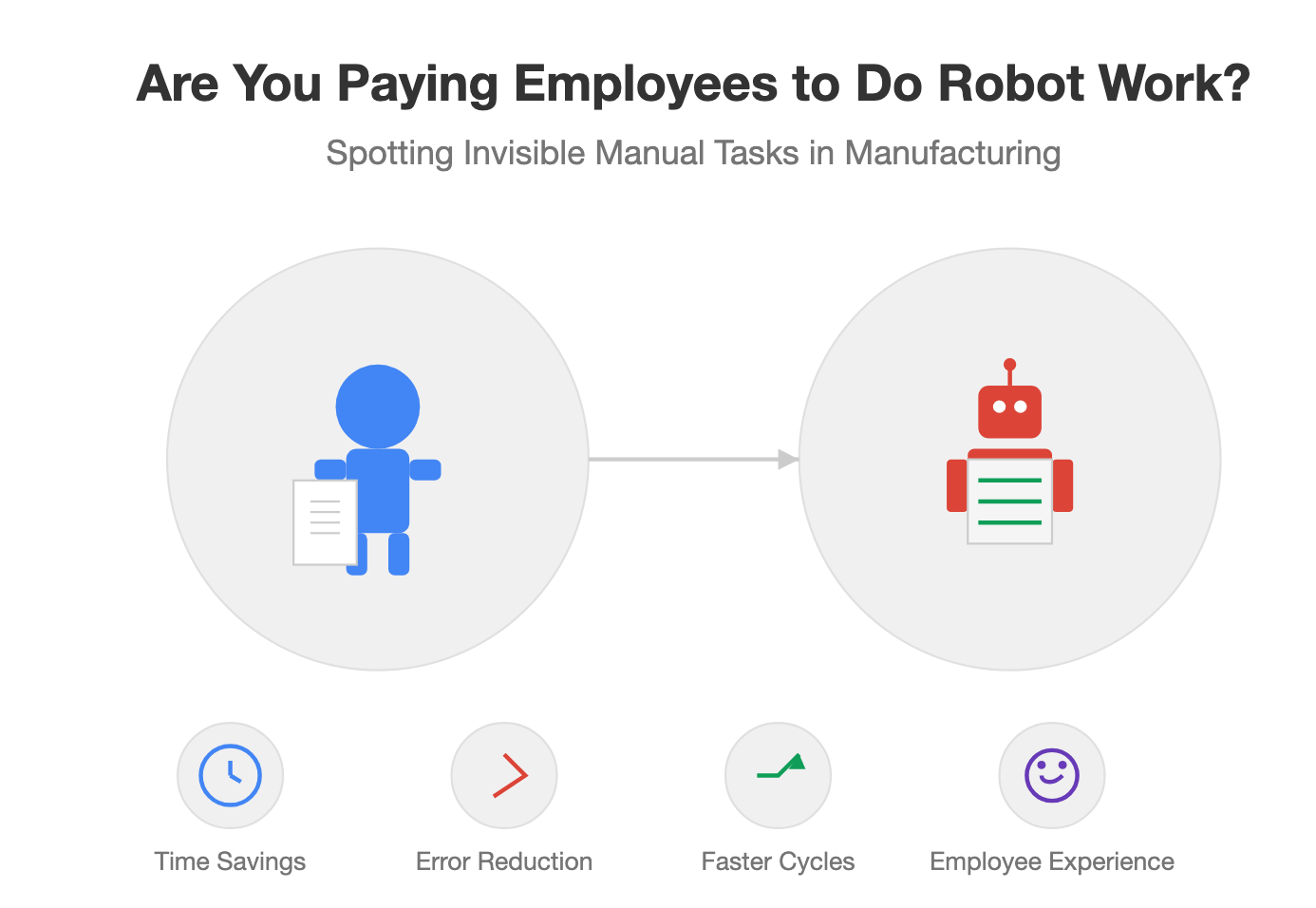
The Hidden Epidemic of Manual Tasks
Manual tasks lurk in the shadows of every organization. They're often not documented in job descriptions. They don't show up neatly in time tracking systems. They exist in the spaces between official responsibilities—the necessary but mundane activities that keep operations running.
According to McKinsey, employees spend approximately 28% of their workweek managing emails and nearly 20% searching for and gathering information. That's nearly half of their productive time consumed by tasks that could be largely automated. For knowledge workers specifically, a study by Asana found that they spend only 26% of their time on skilled work they were hired to do.
These statistics aren't just abstract numbers. They represent real productivity drain happening right now in your organization. A manufacturing director I worked with recently discovered that his team of production planners was spending 15 hours per week collectively on data entry tasks—translating information from paper-based quality inspections into their quality management system. That's nearly two full workdays that could have been dedicated to process improvement or problem-solving.
"I had no idea we were wasting talent this way," he told me. "These are highly trained professionals with engineering degrees. I didn't hire them to be data entry clerks."
The most insidious aspect of these manual tasks? They've become normalized. Employees don't question them. Managers don't see them. They're simply "the way things are done around here."
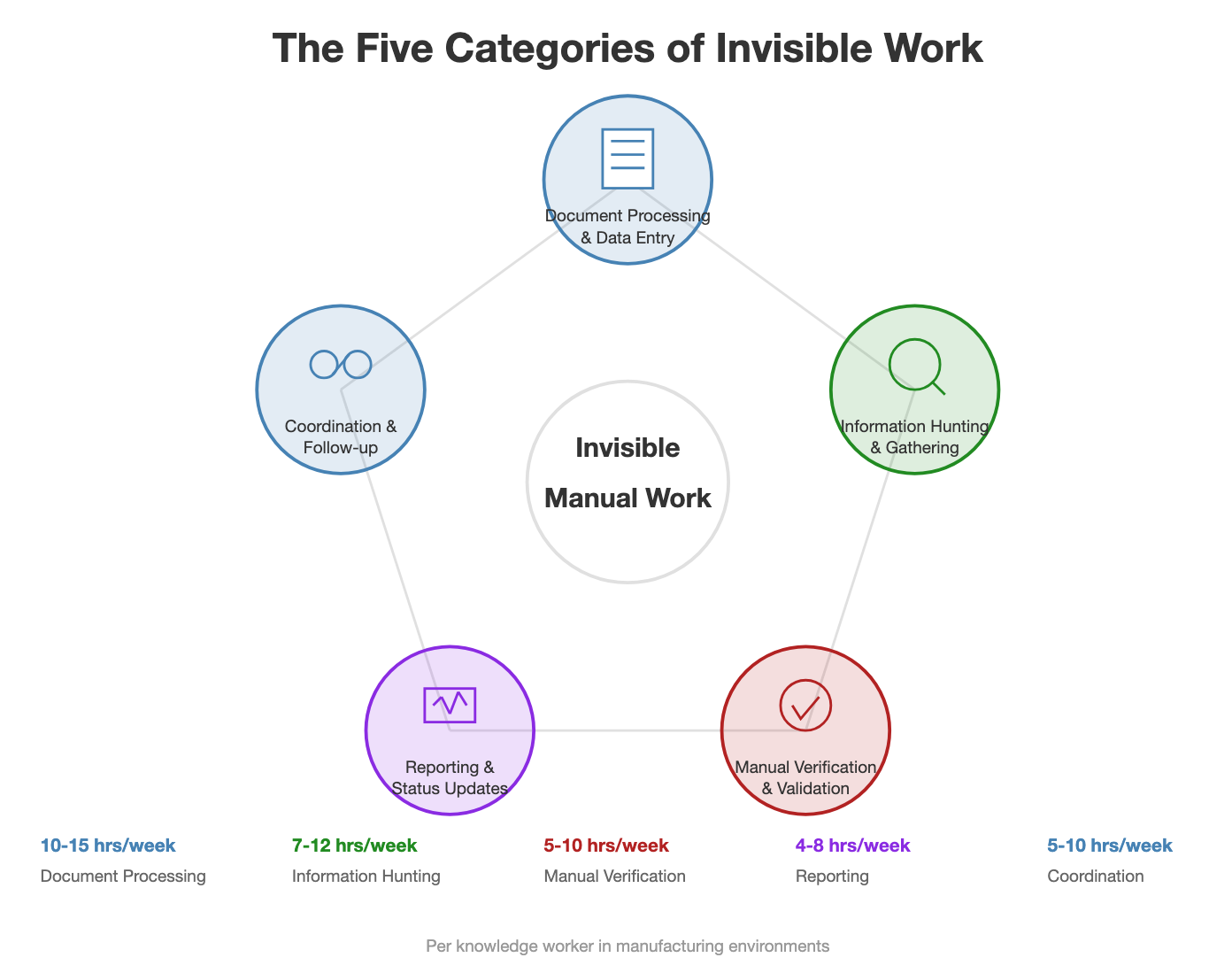
The Five Categories of Invisible Work
Through my work with dozens of manufacturing and industrial companies, I've identified five major categories of invisible manual work that plague operations. Recognizing these categories is the first step toward eliminating them.
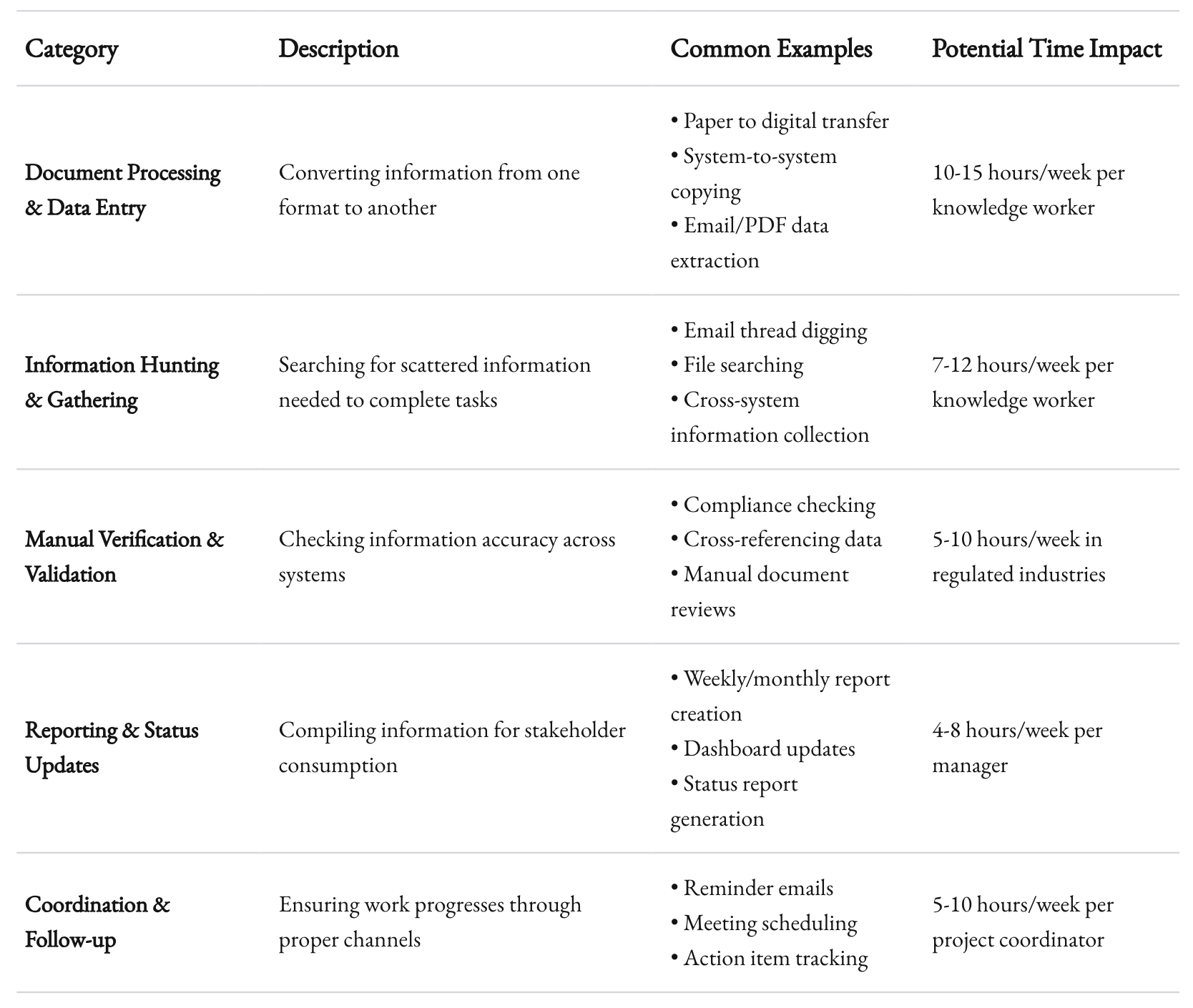
1. Document Processing and Data Entry
This is perhaps the most pervasive form of manual work. It includes:
- Manually transferring information from paper documents into digital systems
- Copying data from one system to another
- Extracting specific information from emails, PDFs, or other unstructured sources
- Re-keying information from spreadsheets into enterprise systems
A metal finishing company I consulted with discovered their order processing team was spending an average of 10 minutes per order on manual data extraction and entry—across 60-70 orders daily at each of their 13 locations. That translated to 10-11.7 hours per day per location lost to manual processing. After implementing automated data extraction, they saved 33,800-41,340 hours annually—equivalent to $650,000 in labor costs.
2. Information Hunting and Gathering
Knowledge workers spend inordinate amounts of time searching for the information they need to do their jobs:
- Digging through email threads to find specific instructions or approvals
- Searching shared drives for the "right version" of documents
- Requesting status updates from colleagues across departments
- Compiling information from multiple sources for reports
An aerospace manufacturing company was struggling with their quoting process, relying on spreadsheets that were difficult to maintain and standardize. Their estimators needed to be highly experienced to create accurate quotes, and inexperienced estimators often caused lost profits through over or under bidding. The company had no way to quantify which bids they were winning as data wasn't being collected systematically.
After implementing an AI-powered pricing tool, they saw a 90% reduction in estimate errors and a 23% increase in win rate. Perhaps most importantly, they could now roll out changes to their pricing strategy six times faster than before.
3. Manual Verification and Validation
In highly regulated industries, verification tasks consume considerable time:
- Manually checking compliance with industry standards
- Cross-referencing information across systems to ensure accuracy
- Verifying calculations or measurements
- Manually reviewing documents for errors or inconsistencies
One particularly stark example comes from a quality control department at a medical device manufacturer. Specialists were spending 12 hours weekly verifying that product specifications in their manufacturing execution system matched their quality management system—essentially comparing two databases that should have been synchronized automatically.
4. Reporting and Status Updates
The corporate appetite for reports is insatiable, and producing them manually is enormously time-consuming:
- Gathering data from various systems for weekly/monthly reports
- Creating custom visualizations from raw data
- Manually updating dashboards
- Producing status updates for different stakeholders with slightly different requirements
I've seen floor supervisors in manufacturing environments spend the last hour of each shift compiling production statistics and quality metrics that existed in their systems but weren't automatically aggregated. That's 250+ hours annually per supervisor—time that could be spent troubleshooting issues or coaching team members.
5. Coordination and Follow-up
The work of making work happen is itself substantial:
- Sending reminder emails for approvals or information
- Scheduling and rescheduling meetings
- Following up on outstanding action items
- Coordinating work across departments or shifts
These tasks are particularly pernicious because they're often seen as "just part of the job" rather than systematic inefficiencies that could be addressed.
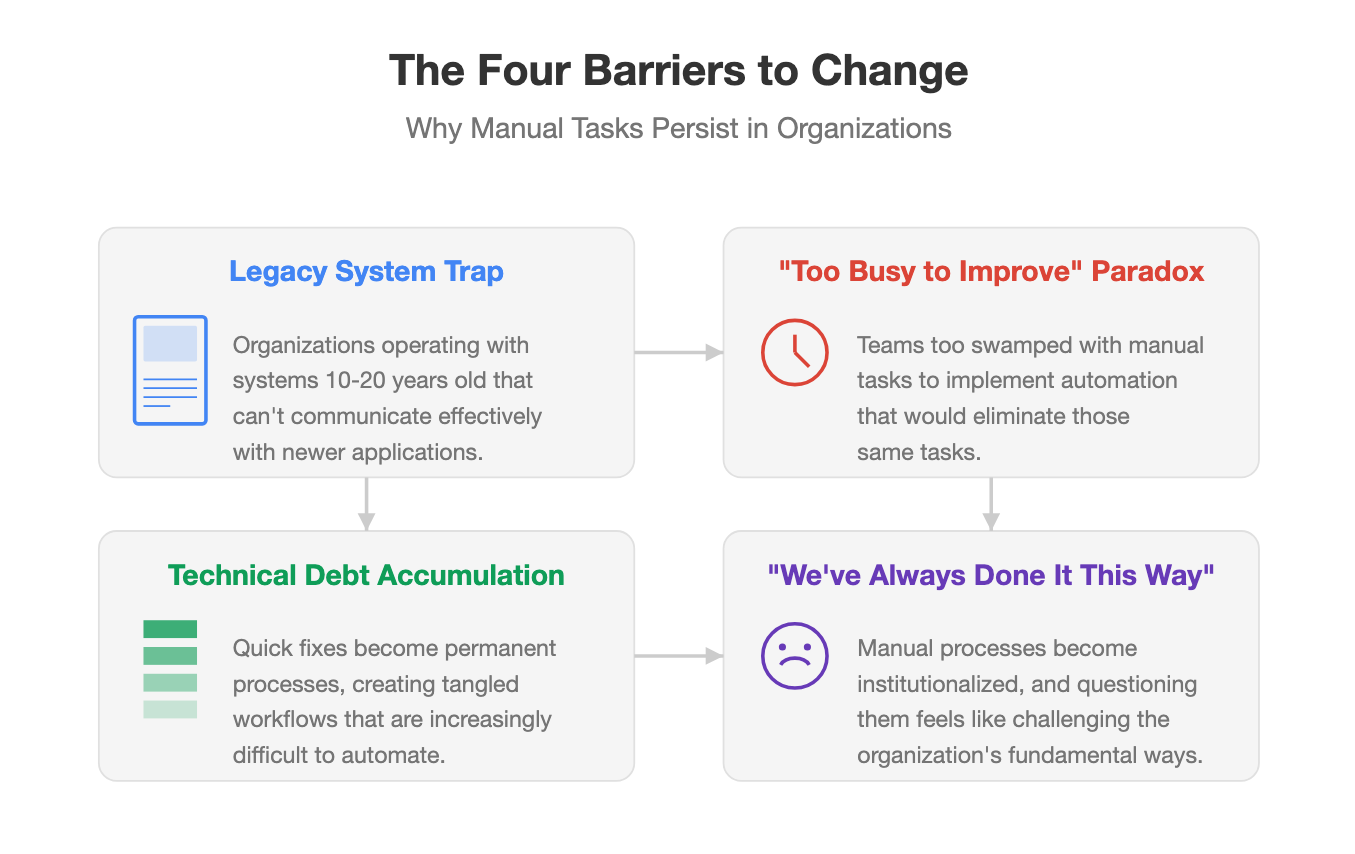
Why These Tasks Persist: The Four Barriers to Change
Understanding why these inefficiencies persist is crucial to eliminating them. Four barriers typically keep these manual tasks in place long past their expiration date.
The Legacy System Trap
Many organizations operate with enterprise systems implemented 10-20 years ago. These systems weren't designed for today's integration requirements and often can't communicate effectively with newer applications. As one IT director put it to me, "We're running 21st-century operations on 20th-century technology."
Companies often compensate for system limitations by creating human workarounds. A purchase order that can't automatically flow from the procurement system to the accounting system gets manually re-entered. Production data that can't be automatically transferred from the shop floor system to the ERP gets manually uploaded at day's end.
These workarounds quickly become standard procedure, and the manual effort becomes invisible—until you deliberately look for it.
The "Too Busy to Improve" Paradox
In a perfect illustration of catch-22 logic, many teams are too swamped with manual tasks to implement the automation that would eliminate those same tasks. When employees are already working at capacity, finding time to document processes, test new solutions, or learn new skills feels impossible.
A maintenance manager at a food processing plant told me his team knew they were wasting hours manually logging equipment checks, but they were so busy keeping machines running that they never had time to implement the digital solution that would save them hundreds of hours annually.
This paradox is particularly challenging because breaking it requires an investment of the scarcest resource—time—with the promise of returns that feel distant when you're in the thick of daily operations.
The Technical Debt Accumulation
Organizations accumulate technical debt when they implement quick fixes rather than optimal solutions. Over time, these shortcuts pile up, creating a tangle of processes that become increasingly difficult to automate or optimize.
I witnessed this at a chemical processing facility where a temporary manual process for reconciling batch records, implemented during a system upgrade five years prior, had somehow become permanent. The planned automation never materialized, and new employees were simply trained on the manual process as if it were the intended design.
The "We've Always Done It This Way" Mindset
Perhaps the most formidable barrier is simple inertia. Manual processes become institutionalized over time, and questioning them can feel like challenging the organization's fundamental practices.
I recall a manufacturing manager who discovered his team was spending hours each week manually creating work orders because "the system doesn't do it right." When pressed, no one could articulate what "right" meant—only that the current process had been in place for years and changing it might cause problems.
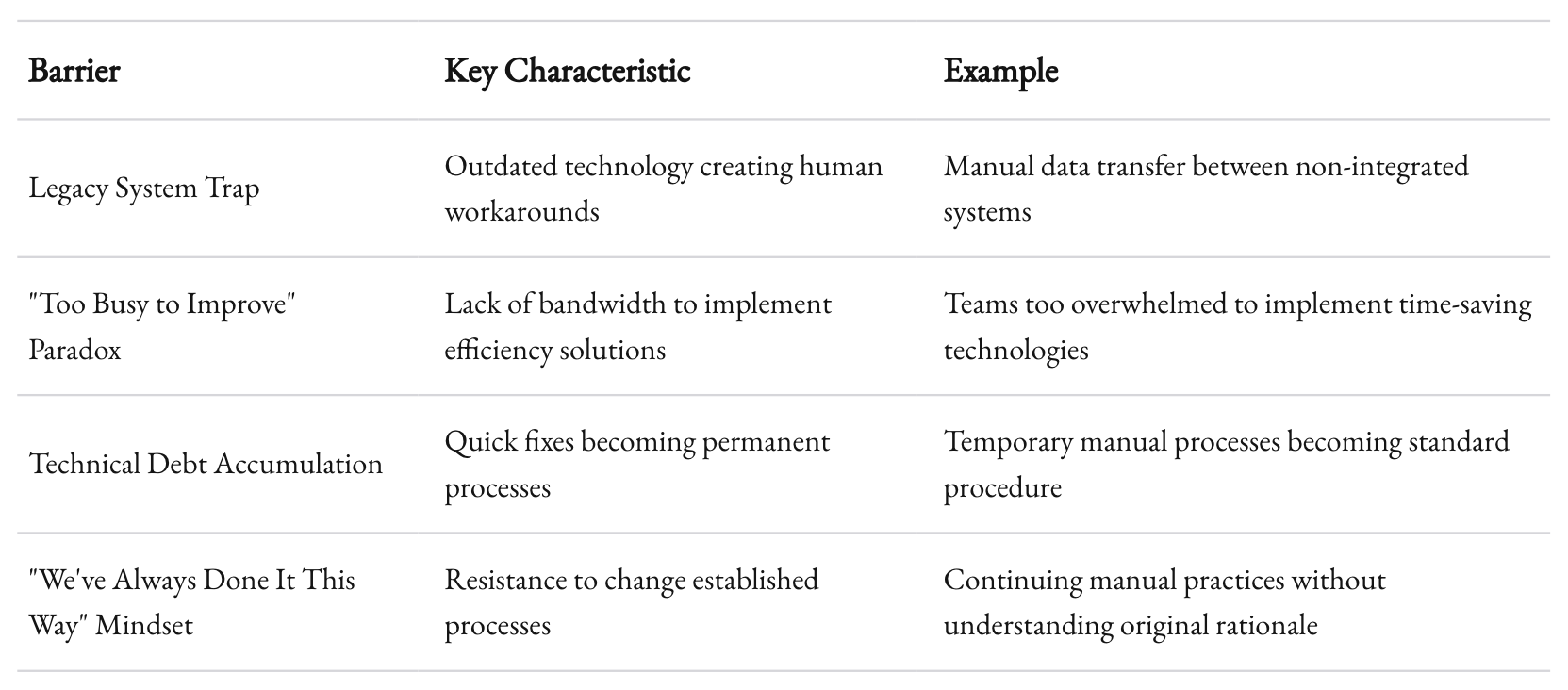
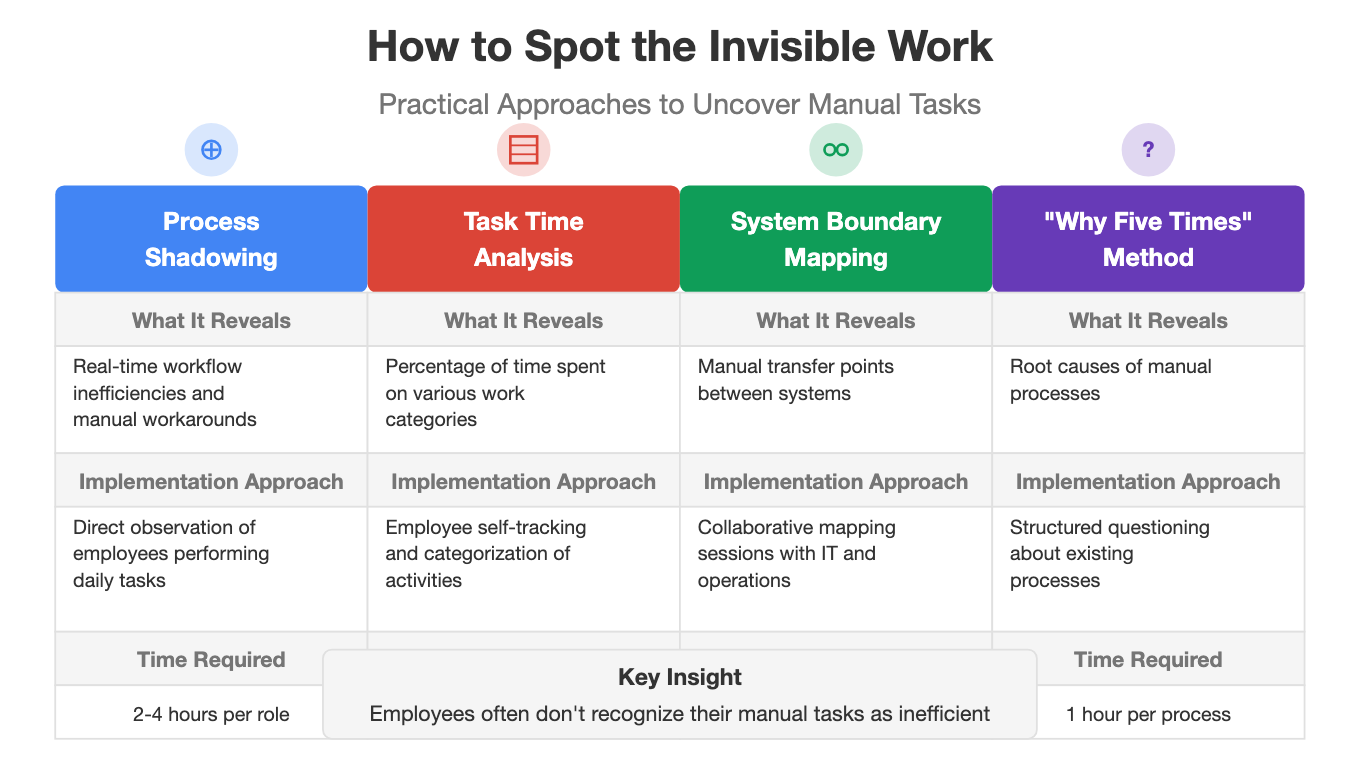
How to Spot the Invisible Work in Your Organization
Identifying manual tasks requires deliberate effort and a fresh perspective. Here are practical approaches to uncover them:
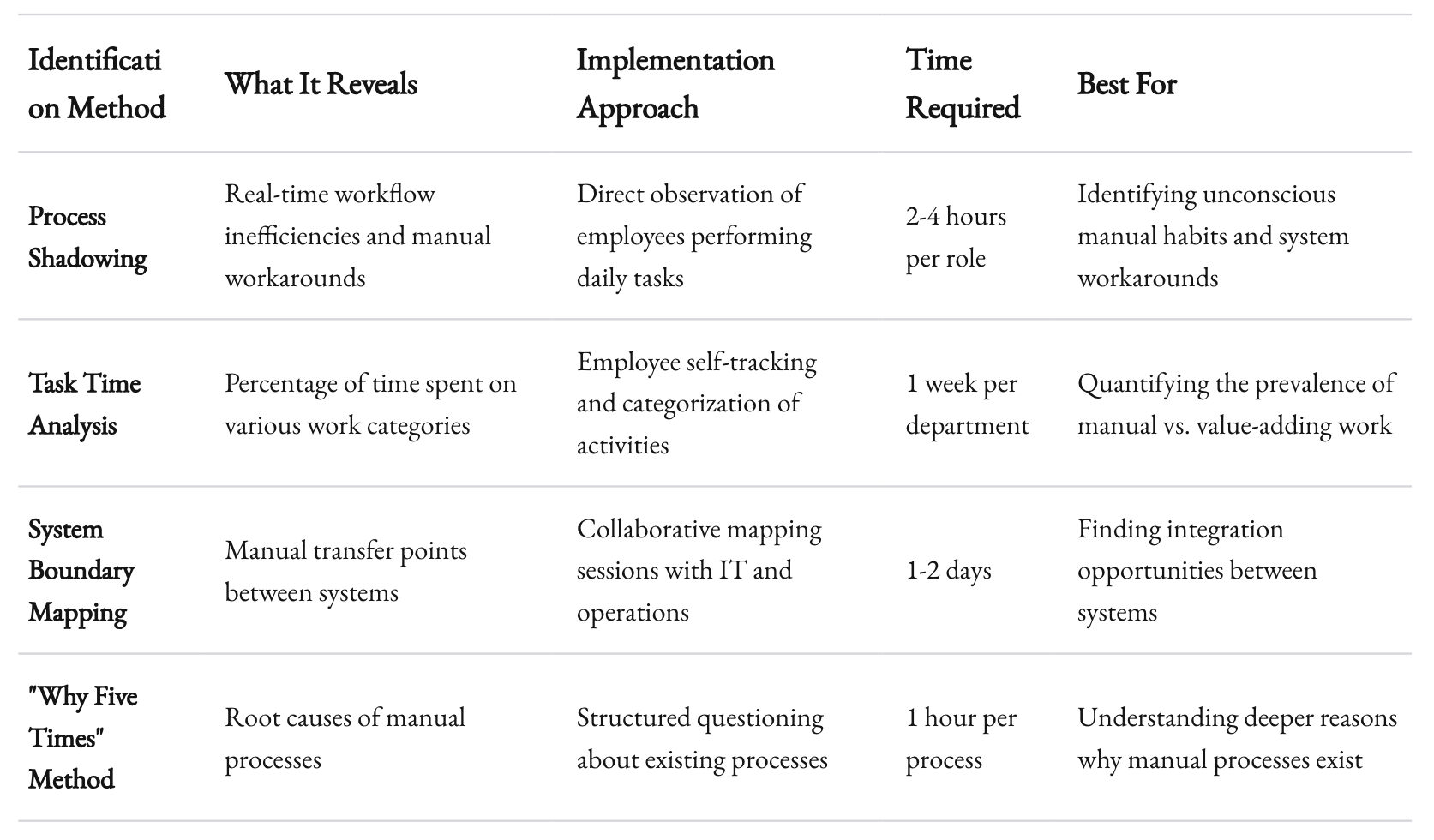
Process Shadowing
The most effective method is simple observation. Select key roles across your organization and arrange to shadow employees for several hours. Don't ask them to explain what they're doing—just watch.
Pay particular attention to:
- Screen switching between applications
- Data being copied from one place to another
- Information being retyped from physical documents
- Time spent searching for files or information
- Repetitive email patterns or follow-ups
I've found that employees often don't even recognize their manual tasks as inefficient because they've become so accustomed to them. Direct observation cuts through this normalization.
Task Time Analysis
Ask employees to track their time in detail for one week, categorizing tasks into:
- Core value-adding work (directly related to primary role)
- Administrative work (necessary but not central to role)
- Manual processing work (repetitive, rule-based tasks)
- Coordination work (making other work happen)
The results often shock both employees and management. In one instance, a team of design engineers discovered they were spending 30% of their time on administrative and manual tasks rather than actual engineering work.
System Boundary Mapping
Create visual maps of how information flows between your key systems. Mark each point where human intervention is required to move information from one system to another. These transfer points are prime opportunities for automation.
For example, a logistics company mapped their order-to-delivery process and found seven distinct points where information was manually transferred between systems—each representing both a delay and a potential error source.
The "Why Five Times" Method
When you observe a manual process, ask "why" five times to get to the root cause:
- Why is this task done manually? "Because we need to check the information."
- Why do we need to check it? "Because the source system sometimes has errors."
- Why does the source system have errors? "Because suppliers don't follow our input standards."
- Why don't suppliers follow standards? "Because we haven't enforced them."
- Why haven't we enforced them? "Because we've always just fixed the errors manually."
This approach often reveals that manual processes exist to compensate for upstream issues that could be addressed more effectively.
The Transformation Path: From Manual to Automated
Once you've identified manual tasks, how do you eliminate them? The journey from manual processes to intelligent automation typically follows four stages:
Stage 1: Streamline Before Automating
Before applying technology, simplify the process itself. Unnecessary steps that have accumulated over time only complicate automation efforts.
A manufacturing client was manually processing quality certificates that accompanied raw material deliveries. Before automating, we analyzed the process and discovered they were capturing 27 data points, though downstream processes only used 8 of them. Simplifying what needed to be extracted made the subsequent automation much more straightforward.
Stage 2: Apply Rule-Based Automation
Start with simple rule-based automation for structured processes. Tools like Robotic Process Automation (RPA) can effectively handle tasks with clear rules and minimal exceptions.
For example, one manufacturing company implemented RPA bots to automatically extract information from standardized supplier invoices and enter it into their accounting system, eliminating 23 hours of weekly manual processing.
Stage 3: Integrate AI for Unstructured Data
For more complex tasks involving unstructured information (like emails, documents, or images), AI-powered tools are required. Modern document processing platforms can extract information from varied formats with remarkable accuracy.
Consider the metal finishing company mentioned earlier. By implementing AI-powered document processing, they automated extraction of critical order information including customer details, part numbers, quantities, material specifications, surface finish requirements, and special processing instructions—all from varied order formats.
Stage 4: Create Continuous Improvement Feedback Loops
The most sophisticated stage involves systems that learn from their own performance. As exceptions are handled by humans, the system learns and improves, requiring less human intervention over time.
An oil and gas inspection company deployed an asset tracking system with this capability. Initially, their field workers needed to validate many of the system's interpretations of container tracking data. But as the system learned from these corrections, automatic processing accuracy improved from 65% to over 90% within three months.
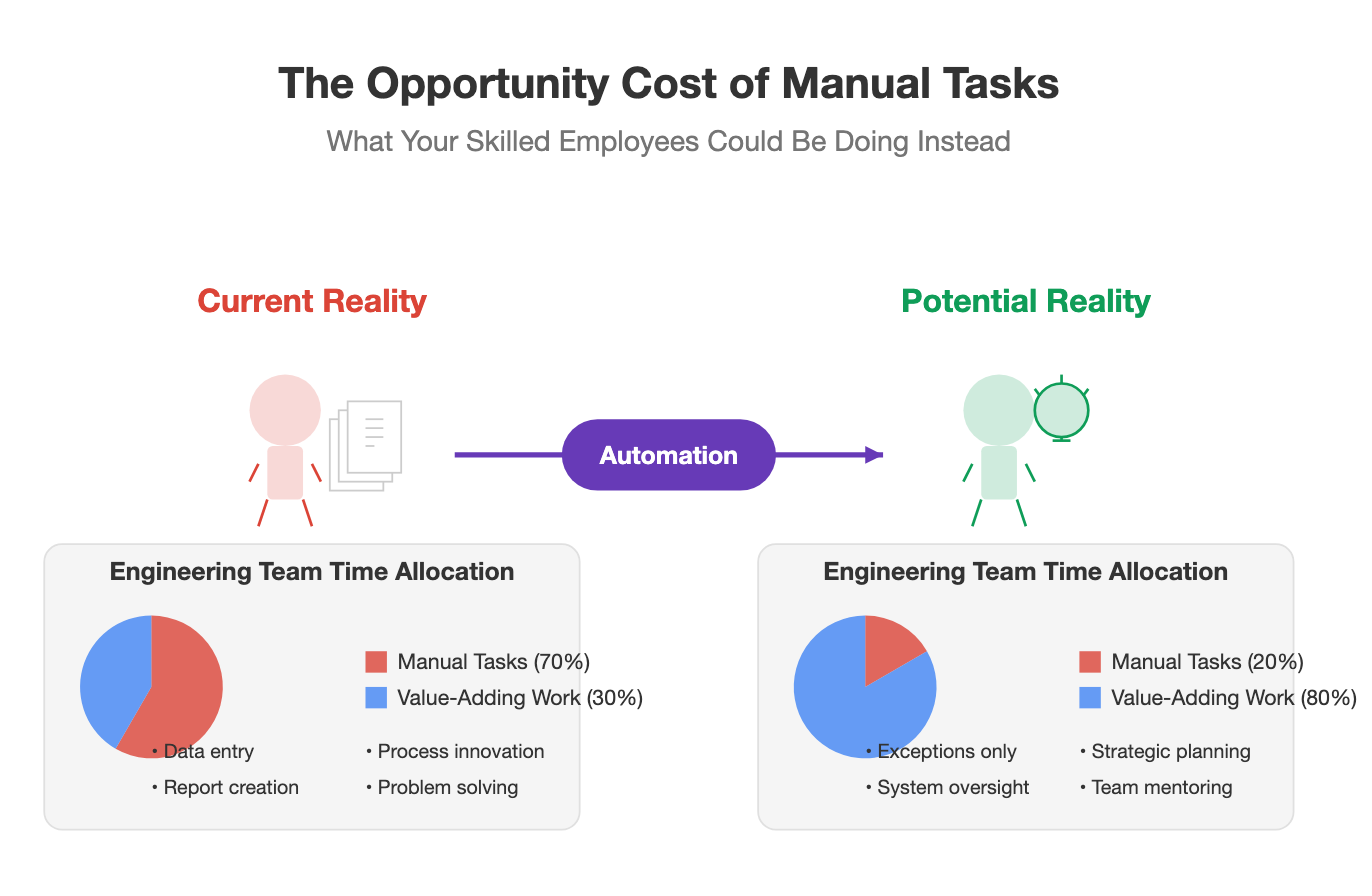
Measuring the Impact: Beyond Labor Savings
The benefits of eliminating manual tasks extend far beyond simple labor cost savings. When evaluating automation initiatives, consider these four impact dimensions:
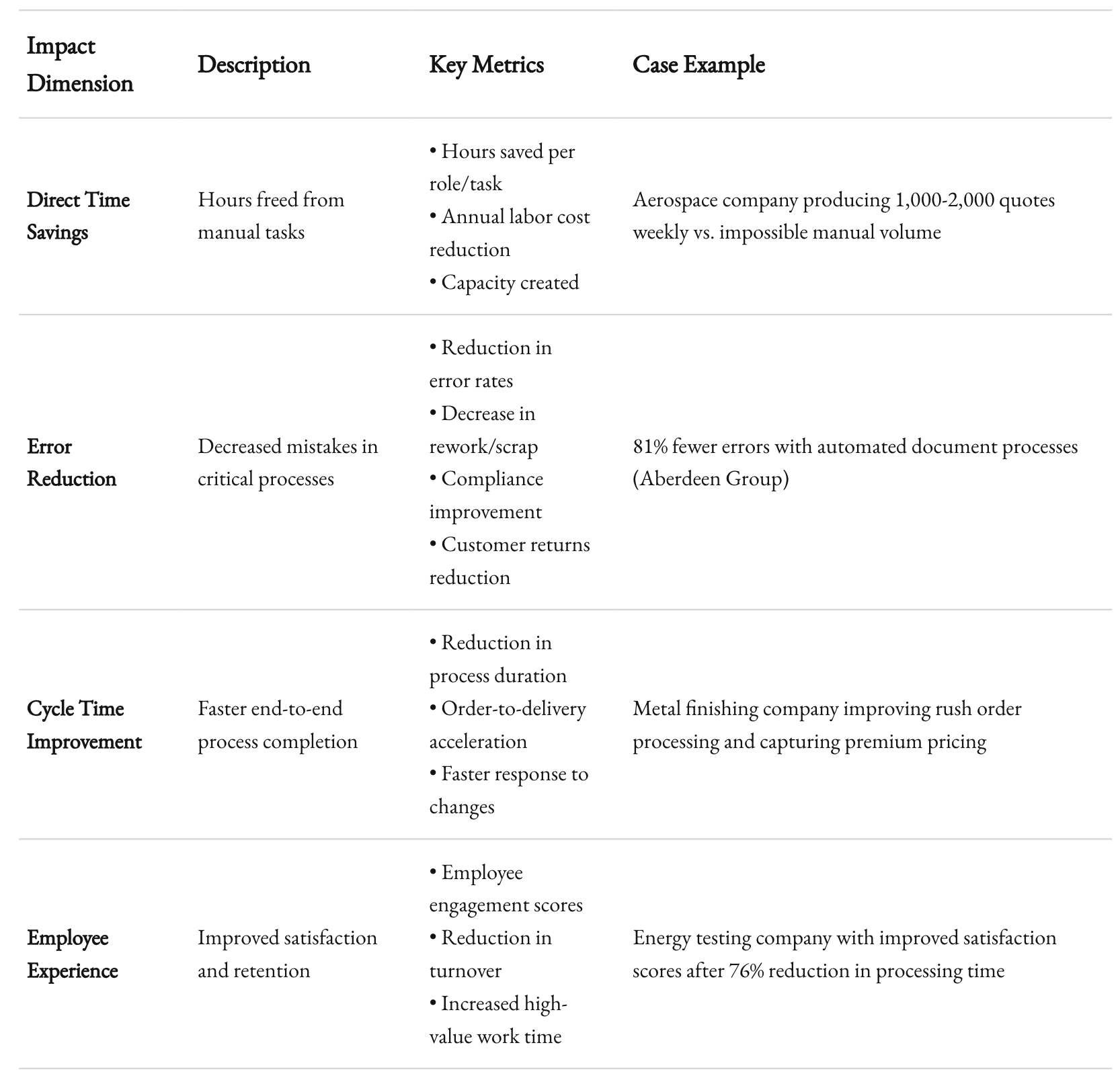
Direct Time Savings
This is the most straightforward measure—hours saved by automating manual tasks. Multiply these hours by fully-loaded labor costs to quantify direct savings.
The aerospace manufacturing company mentioned earlier was able to produce 1,000-2,000 quotes per week across their facilities after implementing their AI-powered pricing tool—a volume that would have been impossible with their previous manual approach.
Error Reduction Impact
Manual processes inevitably introduce errors. Quantify both the direct cost of these errors (rework, scrap, customer returns) and their downstream effects.
A study by the Aberdeen Group found that companies with highly automated document processes experienced 81% fewer errors than those with primarily manual processes. For manufacturing operations where a single error can cause production delays, quality issues, or even safety incidents, this impact is substantial.
Cycle Time Improvement
Faster processes create value beyond labor savings—they improve customer experience, reduce working capital requirements, and increase operational agility.
At the metal finishing company, reducing order processing time by 10 minutes per order not only saved labor costs but also allowed them to process rush orders more effectively, improving customer satisfaction and capturing premium pricing for expedited services.
Employee Experience Enhancement
Perhaps most significantly, eliminating manual tasks improves employee satisfaction and retention. Knowledge workers who can focus on challenging, value-adding work rather than mundane tasks report higher job satisfaction and lower burnout rates.
A global energy testing company that implemented a digital sample collection and technician dispatch solution saw not only a 76% reduction in cylinder intake processing time but also noted significantly improved employee satisfaction scores in their next engagement survey.
Starting Your Automation Journey
If you're convinced it's time to tackle the manual tasks plaguing your organization, here's a practical roadmap to get started:
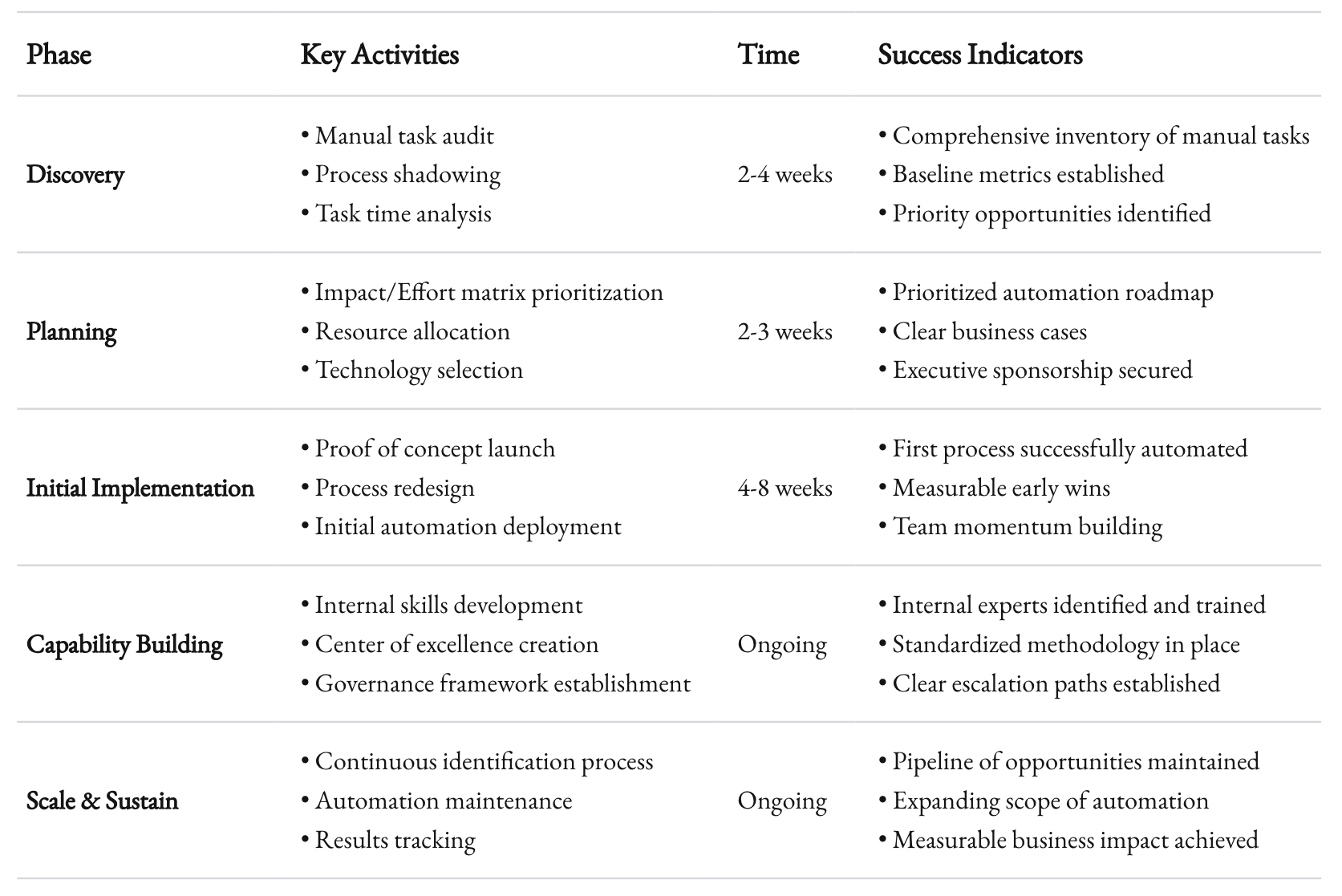
- Conduct a manual task audit Begin with a 2-week assessment of key roles, using the process shadowing and task time analysis methods described earlier. This will give you baseline data on where the largest opportunities exist.
- Prioritize opportunities using the Impact/Effort matrix Evaluate each identified manual task on two dimensions: the impact of automating it and the effort required. Focus first on high-impact, low-effort opportunities to build momentum.
- Start with a proof of concept Select one high-priority process for a focused automation effort. This allows you to demonstrate value quickly while learning how automation technologies work in your specific environment.
- Build internal capabilities As you expand your automation initiatives, invest in developing internal expertise. The most successful automation programs balance external specialists with internal teams who understand your business context.
- Create a continuous identification process Make spotting manual tasks an ongoing practice rather than a one-time effort. Some organizations create "automation scouts"—employees who identify opportunities in their daily work.
The Human-Machine Partnership
The goal isn't to eliminate human work—it's to elevate it. When we free people from robotic tasks, we enable them to apply uniquely human capabilities: creativity, judgment, empathy, and strategic thinking.
A manager at the aerospace manufacturing company put it perfectly after their quoting process transformation: "We didn't reduce our estimating team. We completely changed what they do. Instead of hunting for information and plugging numbers into spreadsheets, they're now analyzing market trends, developing customer-specific strategies, and building relationships. They're doing work that actually requires human intelligence."
That's the promise of eliminating invisible manual tasks—not replacing people with technology, but partnering people with technology so they can do what they do best.
The invisible work in your organization is waiting to be discovered. Your talented people are waiting to be unleashed from mundane tasks. The only question is: when will you start looking?
How is your organization tackling manual processes? Have you uncovered hidden inefficiencies in your operations? Share your experiences in the comments below.
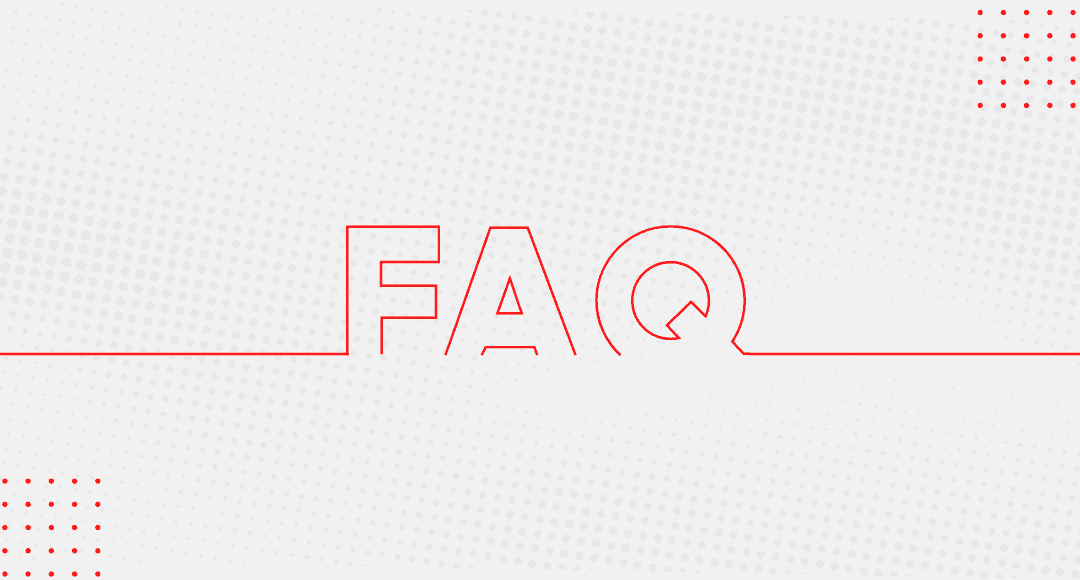
1. How do we identify which manual processes to automate first?
Start by focusing on high-volume, repetitive tasks that follow consistent rules. These typically provide the best return on investment. Document processing, data entry, and information transfer between systems are excellent starting points. Rather than trying to automate entire workflows at once, look for discrete tasks that cause bottlenecks or consume significant time. Create an impact/effort matrix: plot potential automation opportunities based on the business impact (time saved, error reduction, customer experience improvement) against the effort required to automate. Tasks in the high-impact, low-effort quadrant should be your first targets. Remember that automation isn't always about the most complex processes—sometimes automating simple but frequently performed tasks creates the most substantial time savings.
2. Our legacy systems don't integrate well. Is automation still possible?
Absolutely. While seamless system integration is ideal, it's not a prerequisite for meaningful automation. Modern automation approaches can bridge legacy systems without requiring expensive replacement. Technologies like Robotic Process Automation (RPA) can interact with existing applications through their user interfaces, essentially mimicking how humans interact with these systems. API adapters and middleware solutions can create connections between systems that weren't designed to communicate. For document processing, intelligent document processing platforms can extract information from one system and input it into another, creating a digital bridge across disconnected applications. Even when full integration isn't possible, automating portions of a process can still yield significant benefits. Start with the manual transfer points between systems, and you'll often find that automating these handoffs delivers substantial value even if the core systems remain unchanged.
3. How do we measure ROI on automation initiatives beyond simple labor cost savings?
While labor cost savings are the most straightforward measure, a comprehensive ROI calculation should incorporate multiple dimensions. Time-to-value acceleration is often overlooked—measure how much faster processes complete and what that means for customer satisfaction, inventory carrying costs, or production capacity. Error reduction impact should be quantified by examining the downstream effects of mistakes—rework costs, scrap, warranty claims, and customer retention. Capacity creation should also factor in—automation doesn't just save time, it creates new capacity that can be repurposed for higher-value work. Perhaps most importantly, consider the strategic advantages: does automation allow you to respond faster to market changes, introduce products more quickly, or improve your ability to scale operations without proportional cost increases? For manufacturers, metrics like Overall Equipment Effectiveness (OEE) improvement, production changeover time reduction, and quality improvement tell a more complete story than labor savings alone.
4. Will employees resist automation initiatives out of fear for their jobs?
This concern is natural but can be effectively addressed through transparent communication and thoughtful implementation. Frame automation as augmentation rather than replacement—technology handling the mundane aspects of work while humans focus on judgment, creativity, and relationship-building. Involve employees directly in identifying automation opportunities; they know the pain points better than anyone and often welcome relief from tedious manual tasks. Create clear pathways for skill development, showing how automation creates opportunities to develop higher-value capabilities. Share concrete examples of how other employees have transitioned into more rewarding roles following automation. Manufacturing environments in particular often face labor shortages rather than surpluses; automation helps address this reality by allowing existing talent to accomplish more. The most successful automation programs position employees as beneficiaries of the change, not victims of it.
5. How much customization is required for AI-powered document processing in a manufacturing environment?
Manufacturing environments do have unique requirements, but modern intelligent document processing platforms are designed with customization capabilities that don't require data science expertise. Most platforms need some level of configuration for your specific documents—training the system on your quality certificates, bills of materials, inspection reports, and other domain-specific documentation. The amount of customization depends on document complexity and variability. Highly standardized documents with consistent formats require minimal customization, while varied, unstructured documents need more extensive training. Most manufacturing companies find they need moderate customization focused on industry-specific terminology, technical specifications, and company-specific reference data. The good news is that today's AI platforms are designed with business users in mind; many offer no-code or low-code interfaces for training and refining the system. A typical implementation might require 4-8 weeks of configuration and training before reaching production-ready accuracy levels.
6. What's the difference between RPA and AI-powered automation for manufacturing operations?
Think of the relationship between RPA (Robotic Process Automation) and AI as complementary rather than competitive. RPA excels at executing precise, rule-based tasks exactly as programmed—like transferring data between systems, filling out standardized forms, or following explicit if-then decision trees. It's perfect for processes with consistent rules and minimal variation. AI-powered automation, by contrast, can handle ambiguity and learn from experience. It excels at tasks requiring interpretation, pattern recognition, and judgment—like extracting information from varied document formats, classifying incoming communications, or making predictions based on historical data. In manufacturing environments, these technologies often work together: AI might interpret unstructured data from quality inspection reports, while RPA handles the structured task of entering that interpreted data into the quality management system. The choice isn't either/or; most sophisticated automation initiatives incorporate both technologies, applying each where it delivers the most value.
7. How do we ensure data quality and accuracy when automating document-intensive processes?
Data quality requires a thoughtful approach throughout the automation lifecycle. Start with input standardization wherever possible—create templates, data validation rules, and input guidelines for suppliers, customers, and internal teams. Implement progressive validation in your automated workflows, verifying critical data elements at multiple stages rather than a single final check. Confidence scoring is essential—configure your system to flag extractions with low confidence scores for human review while allowing high-confidence extractions to proceed automatically. Exception handling workflows should route unclear cases to subject matter experts who can not only correct the immediate issue but help the system learn from the exception. Ongoing accuracy monitoring through sampling and periodic audits helps catch issues before they become systemic. Remember that perfect accuracy isn't always the goal—in many manufacturing processes, automation that achieves 95% accuracy with the remaining 5% handled through exception processes still delivers tremendous value compared to fully manual approaches that might achieve 98% accuracy but at significantly higher labor costs.
8. What organizational structure best supports ongoing automation initiatives?
The most effective approach combines centralized expertise with distributed implementation capability. A central Automation Center of Excellence (CoE) typically houses specialized technical skills, standardized methodologies, governance frameworks, and best practices. This team handles complex implementations and provides guidance to the broader organization. At the department level, embedding automation champions who understand both the business processes and basic automation capabilities creates crucial translation between technical capabilities and business needs. For manufacturing specifically, having automation expertise within operations rather than solely in IT is vital—people who understand production workflows, quality requirements, and compliance considerations. The CoE model works particularly well because it balances standardization (preventing a proliferation of incompatible solutions) with business relevance (ensuring automation addresses genuine operational needs). As automation initiatives mature, consider whether specialized roles like "automation architects" or "continuous improvement engineers" might help sustain momentum across the organization.
9. How do we maintain and scale automation solutions once implemented?
Sustainability requires thinking beyond the initial implementation. Establish clear ownership for each automated process—someone responsible for monitoring performance, handling exceptions, and initiating improvements. Create a maintenance schedule that includes regular reviews of automated processes against changing business requirements or regulations. Version control is essential, especially for configurations, business rules, and AI models. Develop a testing framework for validating changes before deployment, particularly for mission-critical processes. Knowledge management is often overlooked but crucial—document not just how the automation works technically, but why certain decisions were made and what business rules are encoded. For scaling across the organization, create reusable components, shared services, and templates that accelerate the deployment of similar solutions in different areas. Finally, establish governance mechanisms that balance innovation with standardization, ensuring new automation initiatives leverage existing capabilities while allowing for necessary customization.
10. How will AI advancements change our approach to automation in the next 3-5 years?
Manufacturing automation is entering a transformative phase driven by several AI advancements. Multimodal AI will increasingly combine document understanding with visual inspection capabilities, enabling systems that can extract information from both written reports and production imagery. Generative AI will move beyond content creation to process creation—suggesting optimized workflows based on patterns observed across operations. Knowledge graph technology will connect previously isolated information, creating contextual awareness that improves decision quality. Perhaps most significantly, AI will shift from purely task automation to decision automation, helping identify optimal production schedules, maintenance timing, or quality control parameters. The human-AI interface will become more natural, with conversational capabilities allowing workers to interact with automated systems using everyday language rather than specialized commands. The organizations that will benefit most won't be those that simply deploy the latest technologies, but those that create the organizational capabilities to continuously integrate advancing AI into their operations while maintaining clear focus on business outcomes rather than technological novelty.
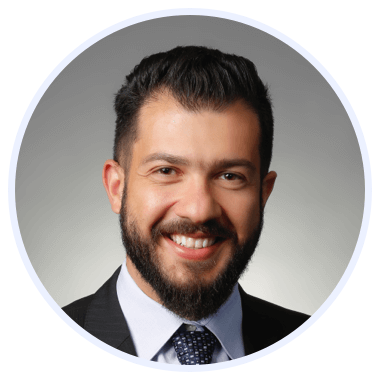
Rasheed Rabata
Is a solution and ROI-driven CTO, consultant, and system integrator with experience in deploying data integrations, Data Hubs, Master Data Management, Data Quality, and Data Warehousing solutions. He has a passion for solving complex data problems. His career experience showcases his drive to deliver software and timely solutions for business needs.