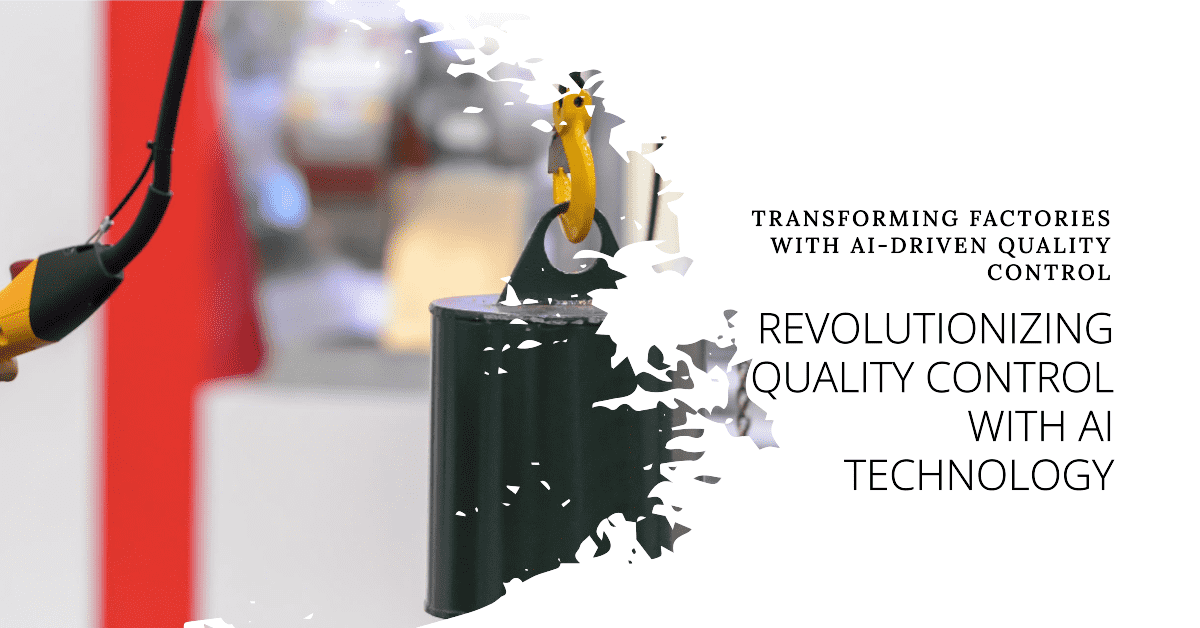
Manufacturing products with high quality and minimal defects has always been a top priority for factories. However, traditional quality control (QC) methods relying on human inspectors are time-consuming, inconsistent, and inefficient at catching all defects. Fortunately, recent advances in artificial intelligence (AI) and computer vision are revolutionizing quality control, enabling 24/7 automated inspection to boost productivity and ensure every product meets specifications.
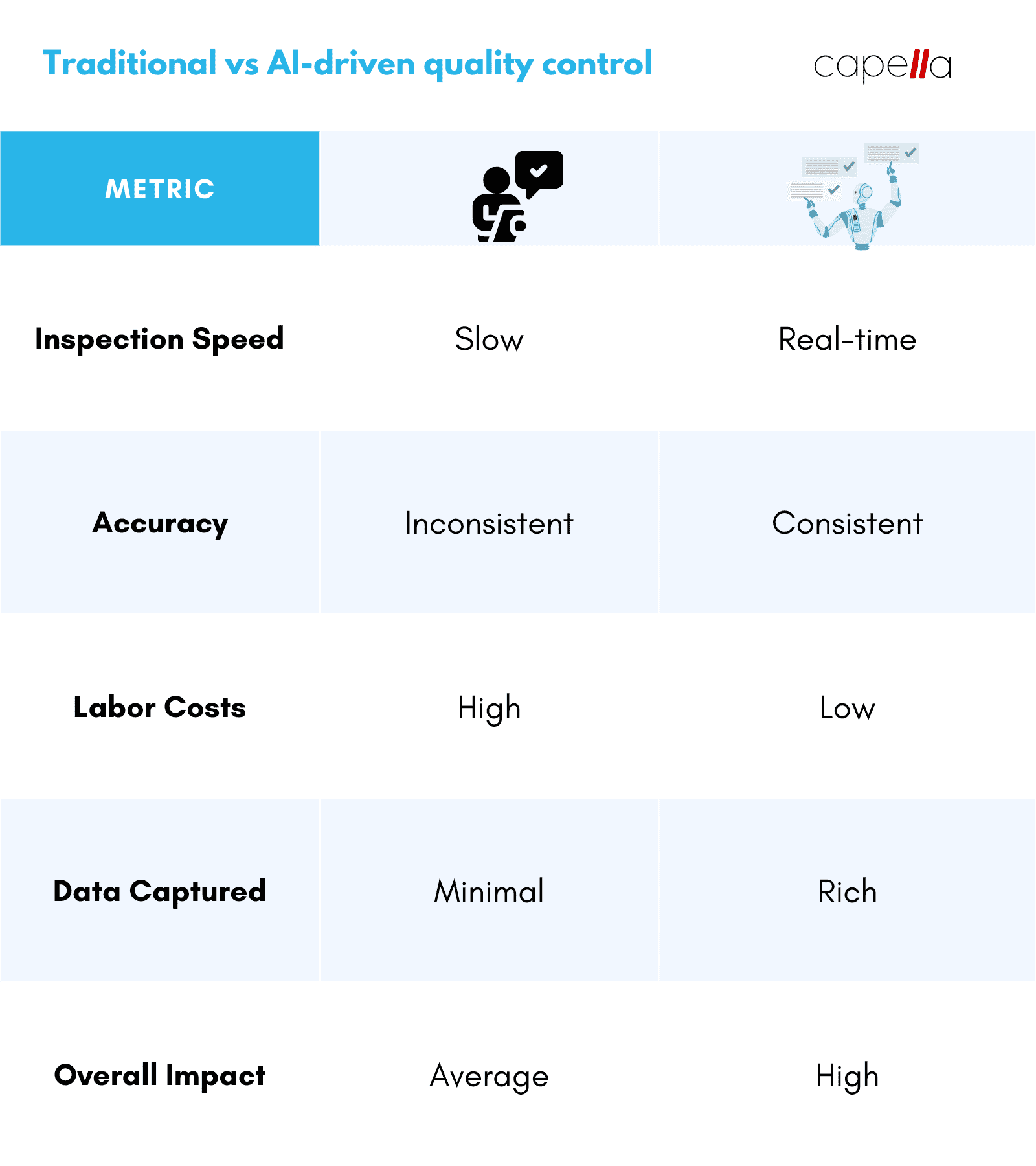
The Need for AI-Driven Quality Control
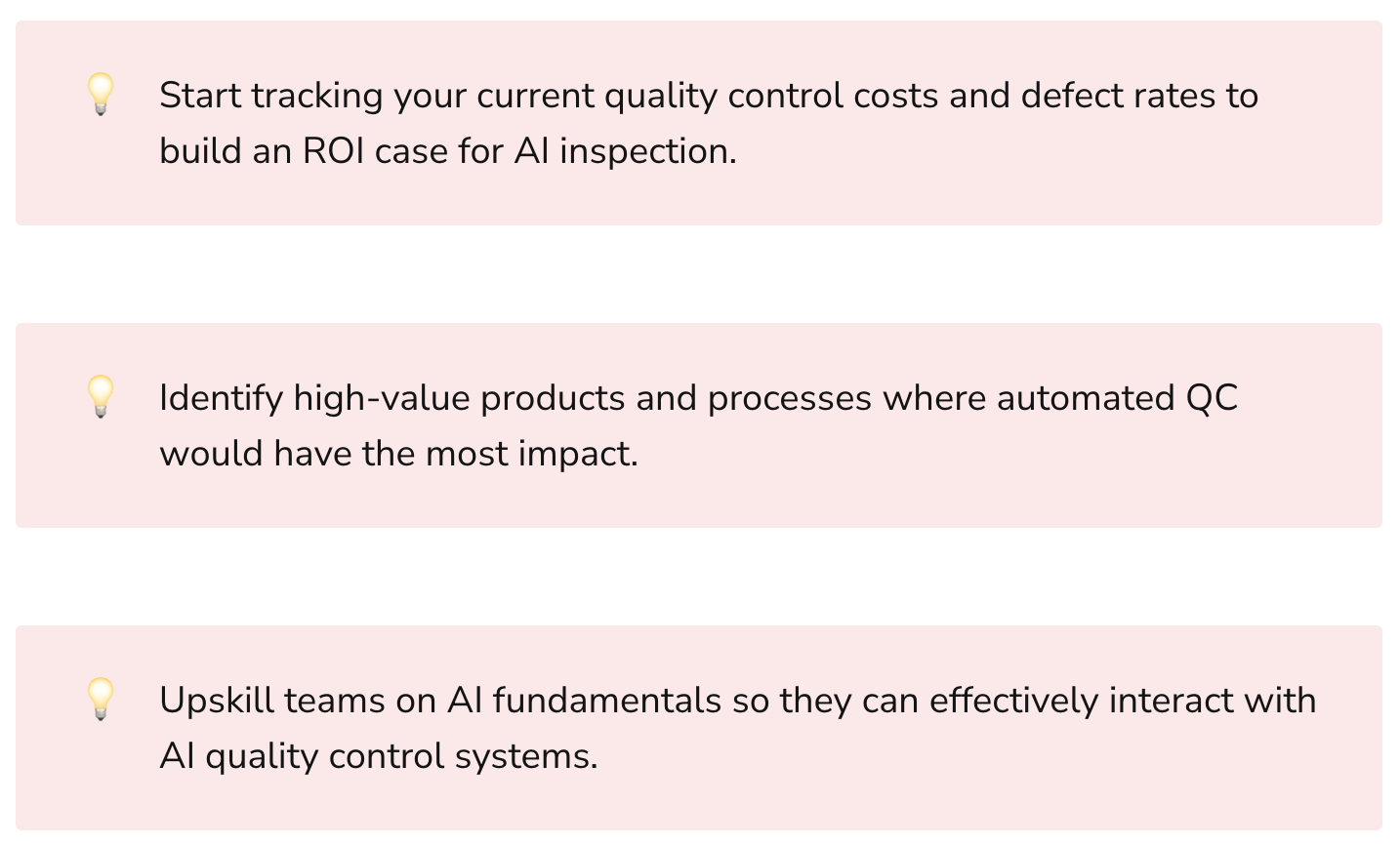
Effective quality control is critical for manufacturing success, but traditional QC approaches have several drawbacks:
- Human inspectors are inconsistent: Humans get tired and miss defects. Per a recent survey, the defect detection rate of human inspectors can vary from 60-90%.
- Manual inspection is slow: Humans can only inspect a limited number of products per hour. For fast-moving assembly lines, thorough manual inspection causes bottlenecks.
- Labor costs are high: Hiring enough qualified QC inspectors imposes a huge wage expense. This cost grows as production scales up.
- Real-time data is lacking: Without real-time QC data, defects may go undetected for long periods, leading to wastage and rework.
AI-driven QC solutions overcome these problems through automated optical inspection. AI algorithms reliably detect any defects, anomalies, and quality issues without any lapses in attention or accuracy. This real-time intelligence allows factories to pinpoint and resolve quality problems as soon as they occur. For large manufacturers, AI quality control can reduce costs by millions per year while also improving product quality.
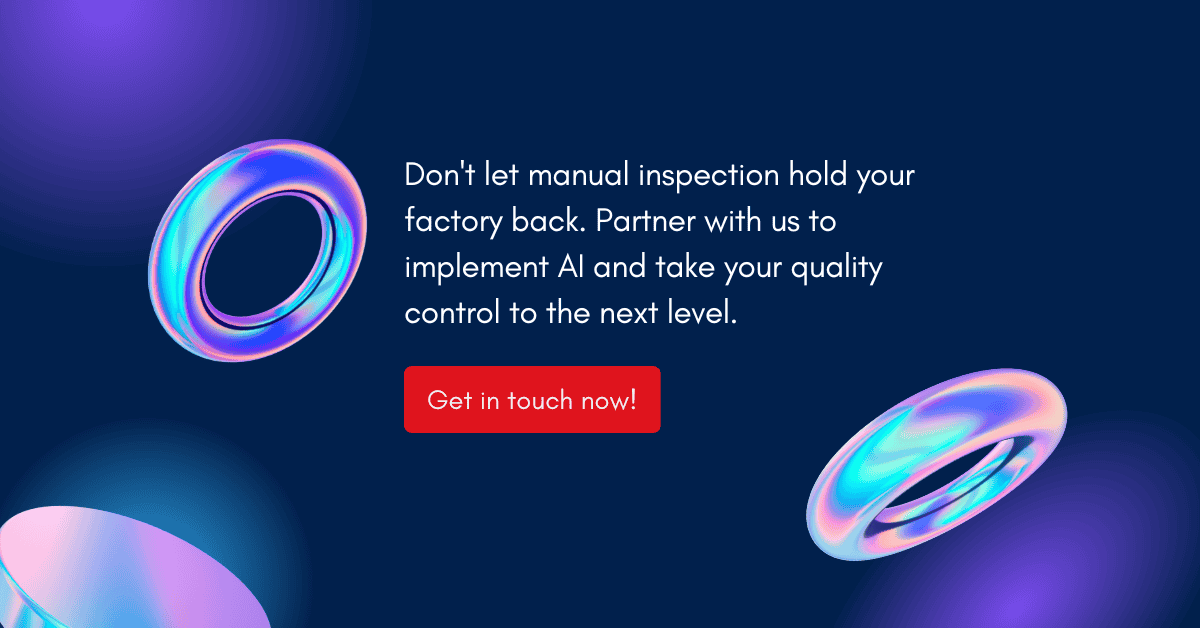
AI Quality Control Use Cases in Manufacturing
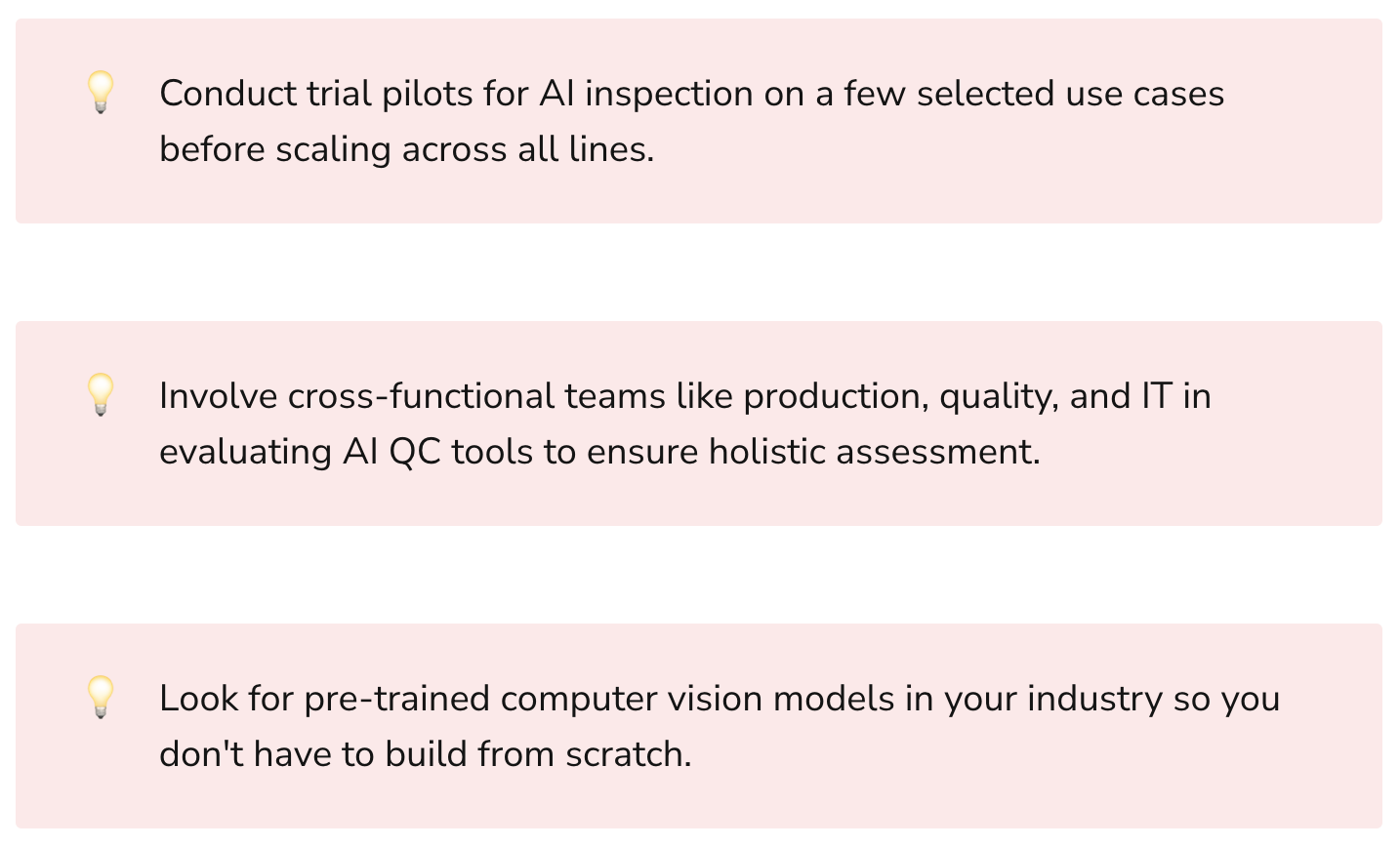
Here are some common use cases where AI is revolutionizing quality control and inspection:
Surface Defect Detection
AI-powered computer vision can automatically scan manufactured materials such as steel, fabrics, wood, glass etc. and identify any scratches, cracks, dents, and other surface abnormalities that human eyes would likely miss. For example, Intel uses AI on its chip fabrication lines to catch microscopic defects through thermal and voltage imaging.
Structural and Dimensional Checking
AI can accurately measure key product dimensions like length, diameter, angle etc. and flag any out-of-spec measurements in seconds. For products like machined auto parts with extremely tight tolerances, AI ensures every part meets exact design specifications.
Assembly Verification
AI algorithms can confirm whether an assembled product matches its required bill-of-materials (BOM). These checks verify that no parts are missing or incorrect in the final product.
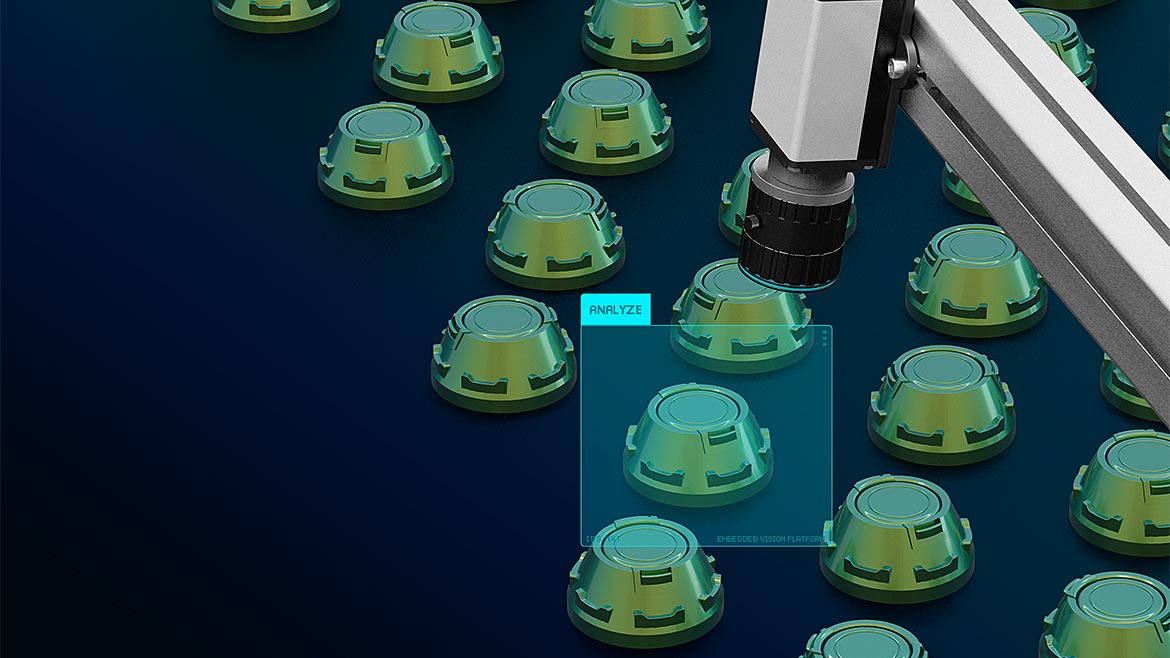
Label, Packaging, and Artwork Inspection
Computer vision techniques can check for proper packaging, labeling, and artwork based on trained models. This prevents issues like missing labels, incorrect translations, or color mismatches.
Cosmetic Flaw Detection
Tiny blemishes imperceptible to humans can be caught by AI inspectors. For example, displays and screens are checked for dead pixels. Luxury goods are verified to have no scratches or irregular markings.
Anomaly Detection
By baselining the visual appearance of defect-free products, AI can flag anomalous issues that deviate from the norm. Products with unusual shapes, colors, textures etc. are flagged for further quality checks.
With its superhuman speed, consistency, and precision, AI enables manufacturers to perform more comprehensive quality inspections in real-time. This prevents faulty products from proceeding further along the production line and minimizing wastage. Next, let's look at how AI-based inspection systems work.
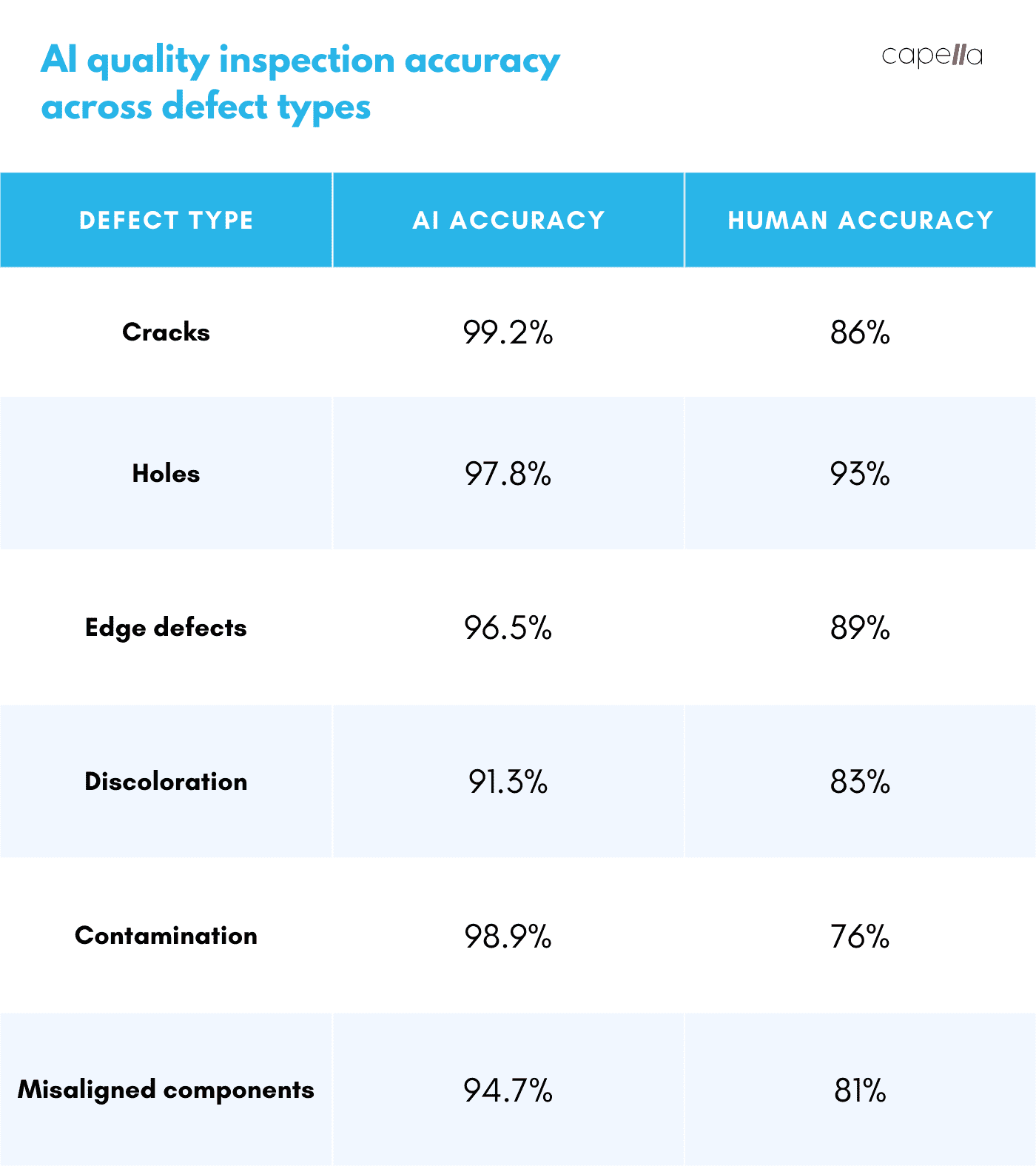
Technical Overview of AI Quality Control Systems
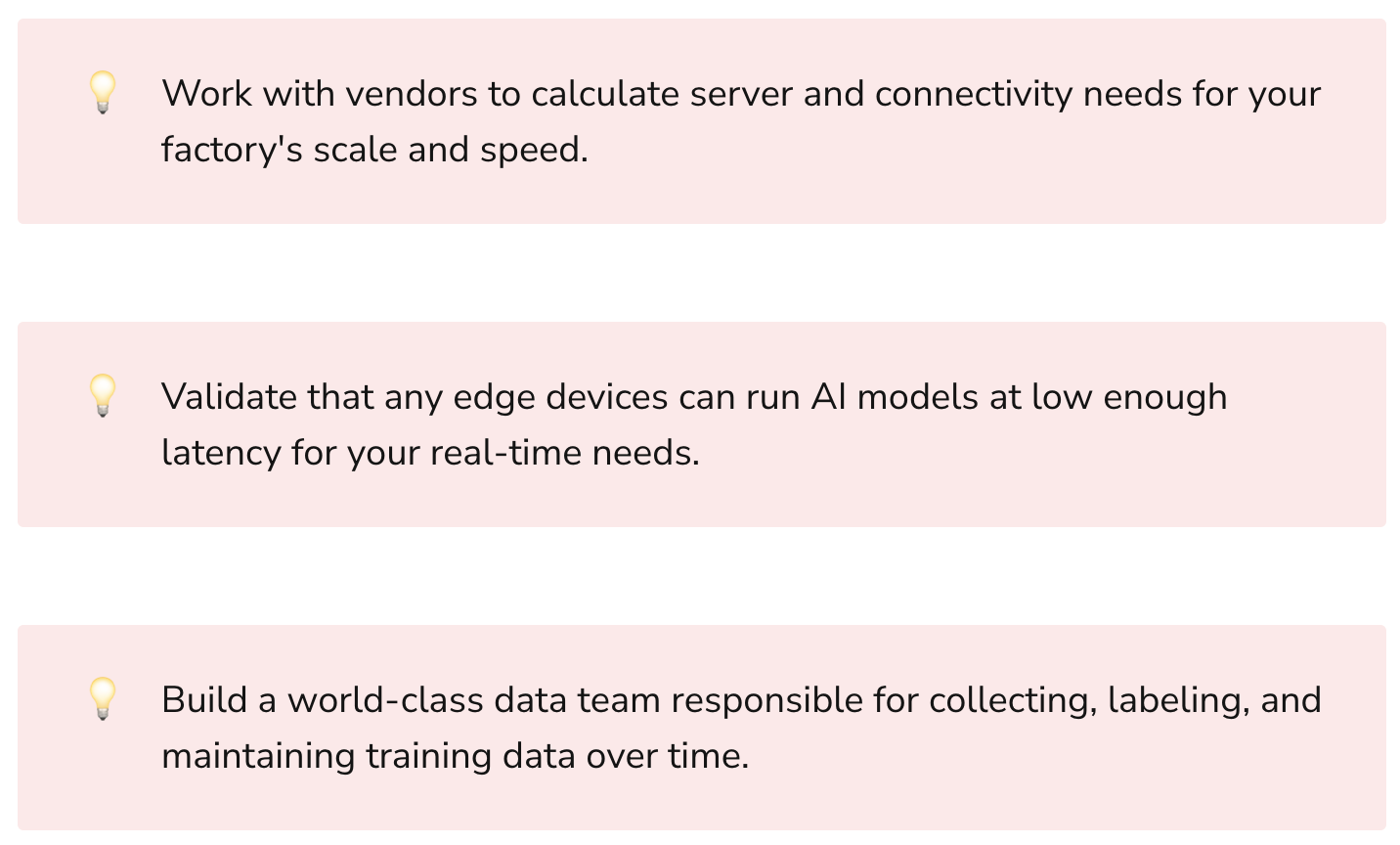
At a high level, AI quality control systems comprise of the following components:
- Image capture devices like cameras and sensors to collect visual data across the production line
- A neural network model trained on images of defective and non-defective products
- An inference engine that runs input images through the trained model to classify any defects
- Software to visualize results and integrate with other factory systems
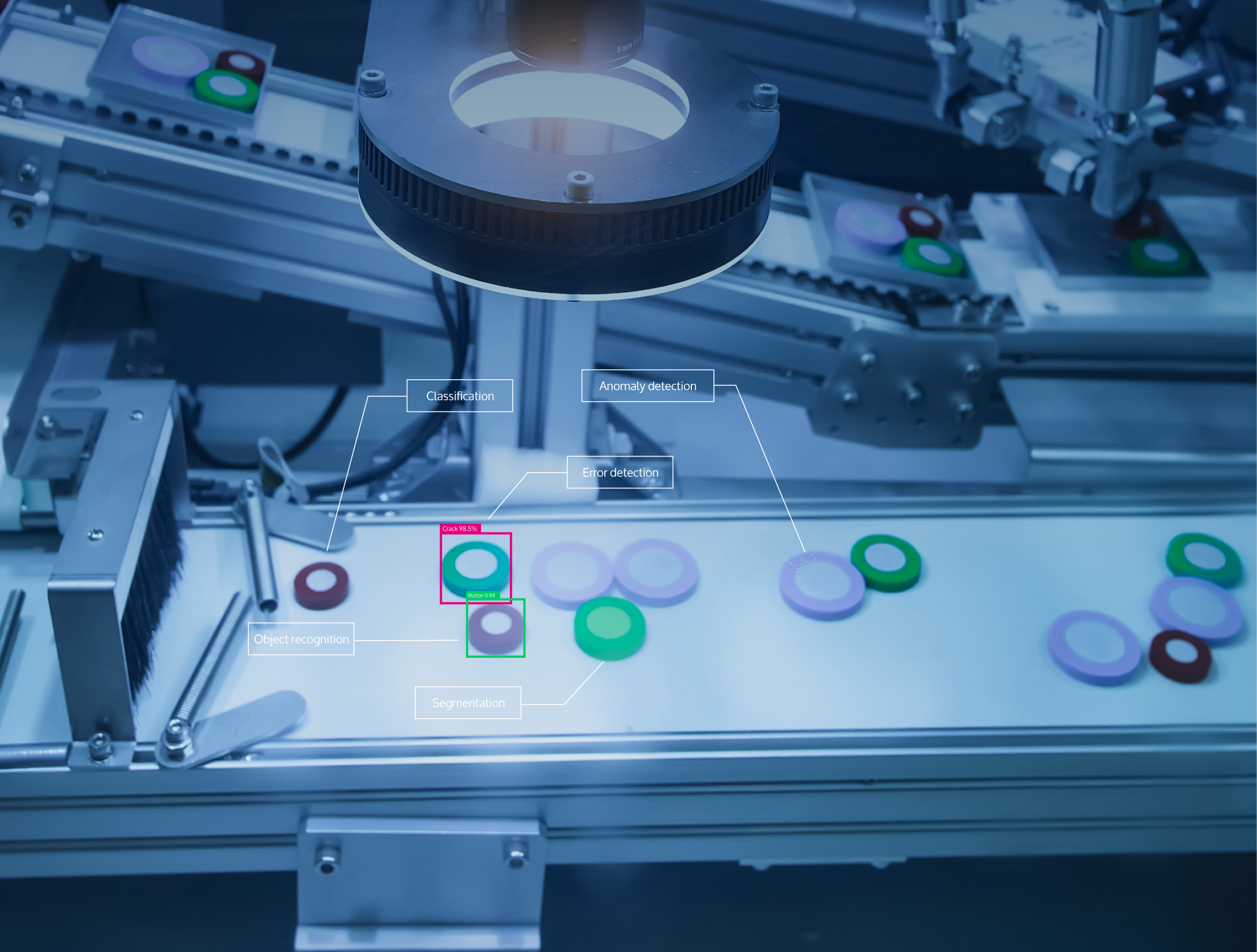
Let's look at each component in more detail:
Data Capture
High-resolution RGB cameras or specialty sensors like infrared are strategically positioned across the production line to collect images or video for analysis. The key requirements are:
- Capture views from multiple angles to completely cover the product surface
- Avoid motion blur with fast exposure speeds
- Provide sufficient lighting for clear image capture
- Include camera calibration to ensure pixel accuracy for defect detection
Neural Network Model
A convolutional neural network (CNN) is trained on large labeled datasets containing images of normal and defective products. Common CNN models like ResNet and VGGNet are used. The key steps are:
- Gather a diverse range of labeled product images covering all critical defect categories
- Train a CNN model architecture on this dataset
- Tune model hyperparameters like learning rate for optimal accuracy
- Perform techniques like data augmentation to increase the size and diversity of the training dataset
Popular open-source frameworks like PyTorch and TensorFlow help streamline model development.
Inference Engine
This module runs live input images through the trained neural network model to identify any defects. The model outputs a probability score for each defect classification. An interface displays these results to factory operators or feeds them to downstream analytics systems.
Popular inference engines like TensorRT and Intel OpenVINO are optimized to deliver low-latency defect predictions, even on edge devices. This enables real-time quality inspection on fast assembly lines.
Results Interface
Operators can clearly visualize defect analysis via software dashboards or on their mobile devices. Defect locations are overlayed on product images to simplify root cause analysis. The results interface also displays product pass/fail status, metrics like hourly defect rate, and can connect to enterprise databases.
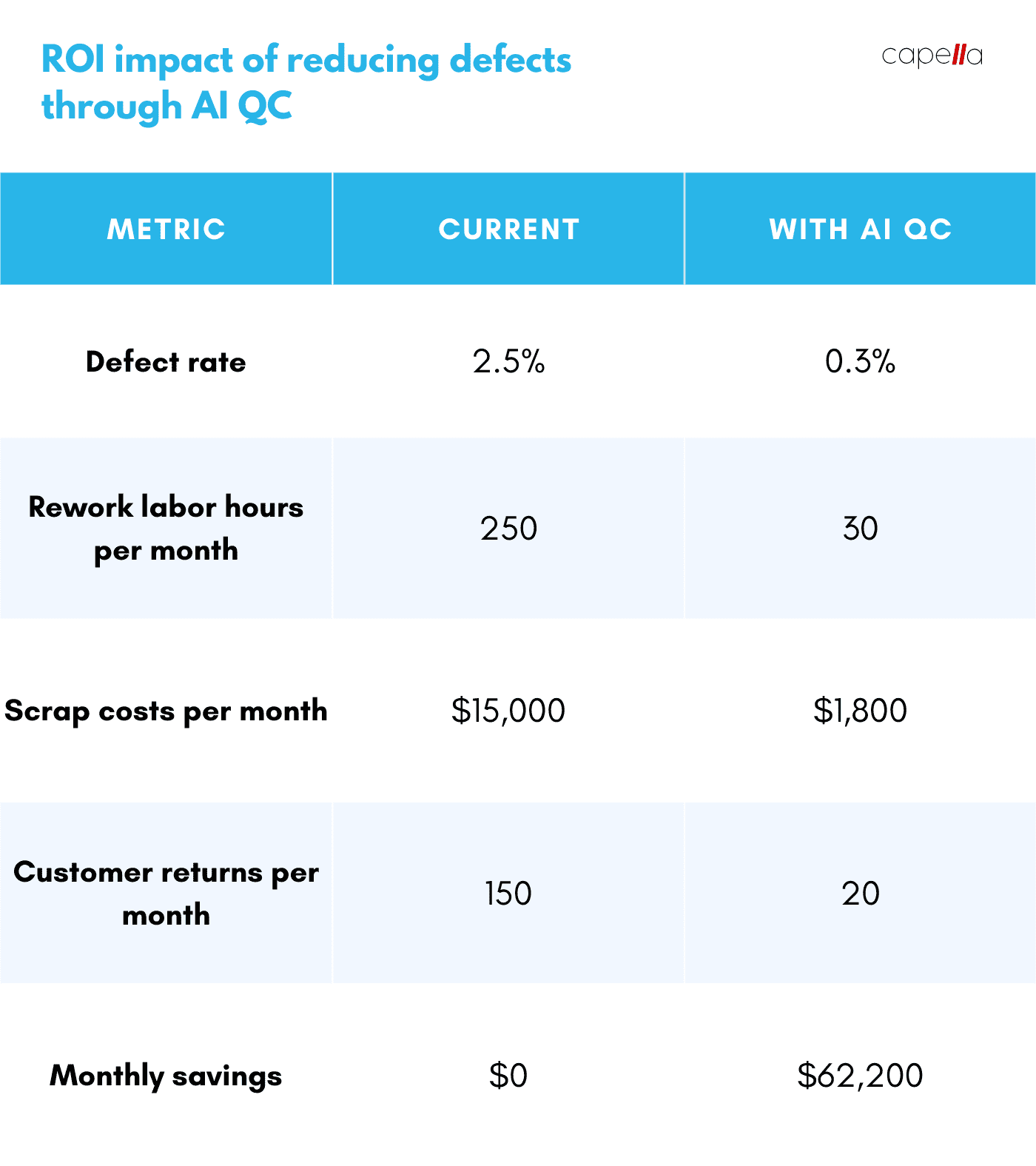
Deploying AI Inspection - Challenges and Best Practices
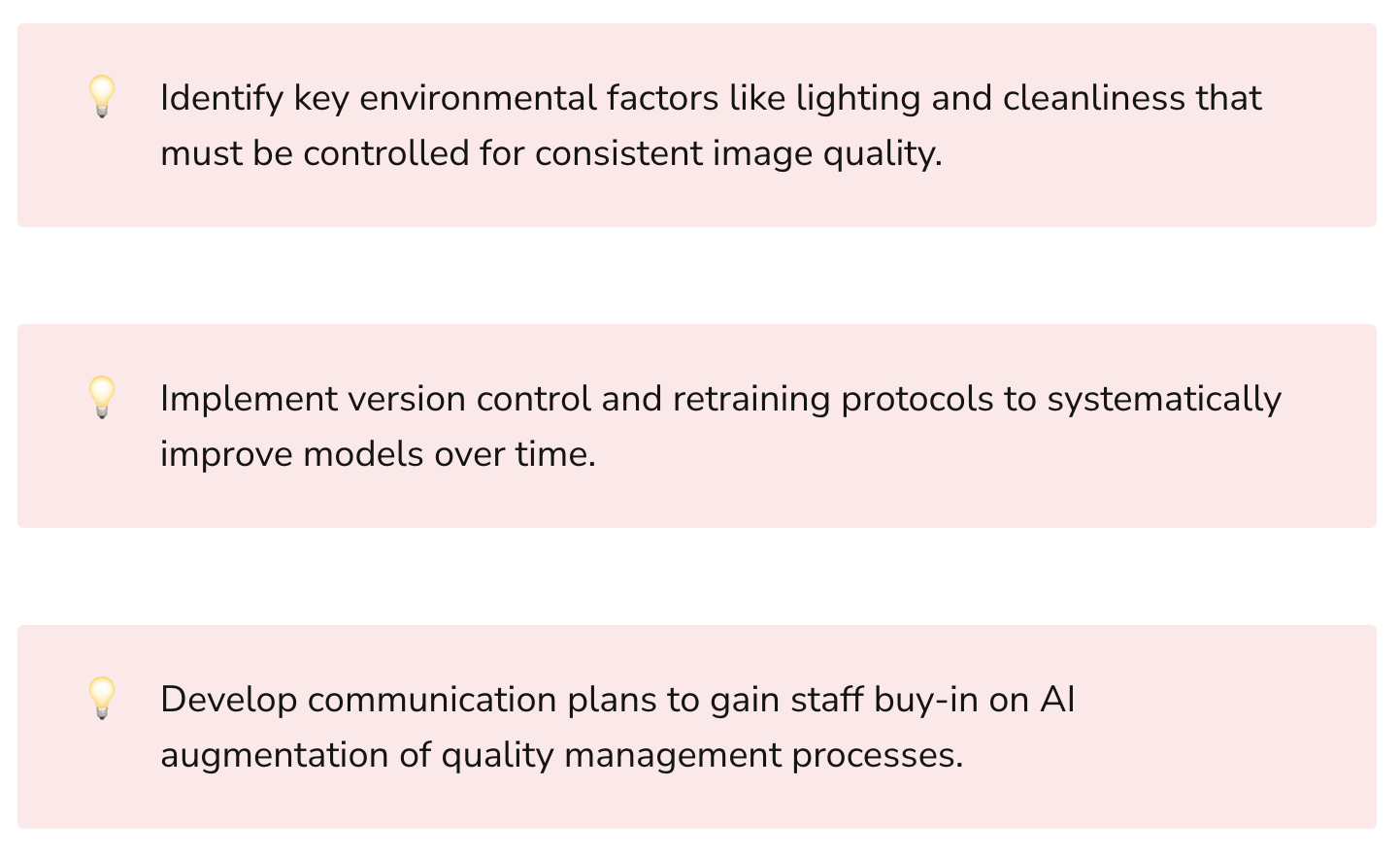
While AI inspection delivers immense quality and productivity gains, manufacturers should be aware of some common challenges:
- Image quality - Blurry, dark, or obstructed images lead to inaccurate model predictions. Proper lighting, camera setup, and lens cleaning is essential.
- Training data gaps - If defect samples for a particular product or machine are limited, the model may overlook these issues. Cross-training on data from other factories helps.
- Model accuracy - Like humans, AI models can also make errors in classification. Regular validation and tuning helps improve precision.
- Hardware constraints- Camera resolution, computer vision model complexity, and edge device memory are key hardware constraints. Lightweight efficient models are preferred.
- Model drift - If product materials or specifications change over time, the AI model needs re-training on updated data to avoidmissed defects.
Here are some tips for successfully rolling out AI quality control:
- Start small - Run pilots on a limited product range before expanding. This allows testing configuration settings and training data.
- Simplify data collection - Provide cameras and sample collection kits at key locations. Clean, standardized data ensures accurate models.
- Monitor model metrics - Track performance indicators like precision, recall and regularly update models.
- Enable rapid retraining - Have mechanisms to rapidly retrain models on any new products or defect patterns.
- Embed across the line - Deploy at multiple stages from workstations to packaging to provide complete coverage.
- Combine with IoT data - Correlate AI findings with IoT sensor streams for deeper insights.
- Smooth IT integration - Ensure AI findings automatically update centralized quality databases.
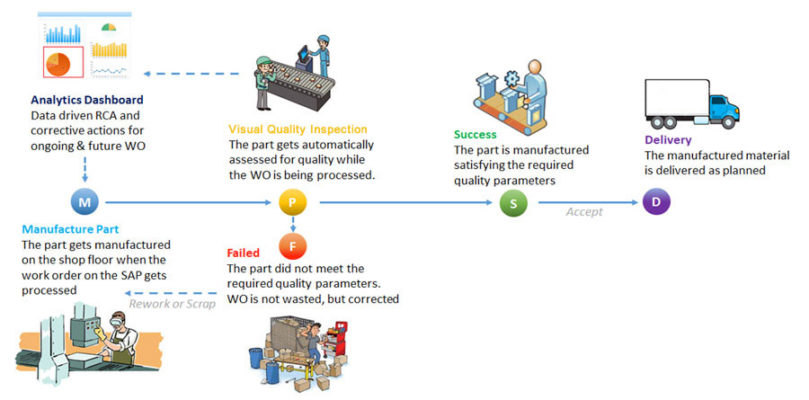
Real-World Examples of AI Quality Inspection
Global manufacturers across industries are adopting AI-based visual inspection and reaping major benefits:
- BMW uses AI robotic arms equipped with cameras to autonomously scan for exterior paint defects that are invisible to the human eye. This deep inspection capability has improved vehicle quality standards.
- Pepsi Co has deployed computer vision on its packaging lines. This has reduced missed package defects by up to 50%, minimizing waste and rework according to internal estimates.
- L'Oréal implemented automated visual inspection of labels, artwork, and sealing integrity across 20 quality checkpoints along its assembly lines. This has decreased defects by 60%.
- Johnson & Johnson increased defect detection rates from 75% to over 95% by augmenting human inspection with AI. This statistical analysis shows the power of combining human and AI abilities.
These examples highlight the scope of AI-based quality control across discrete and process industries. The rapid ROI, elevated quality, and operational efficiencies are accelerating AI adoption.
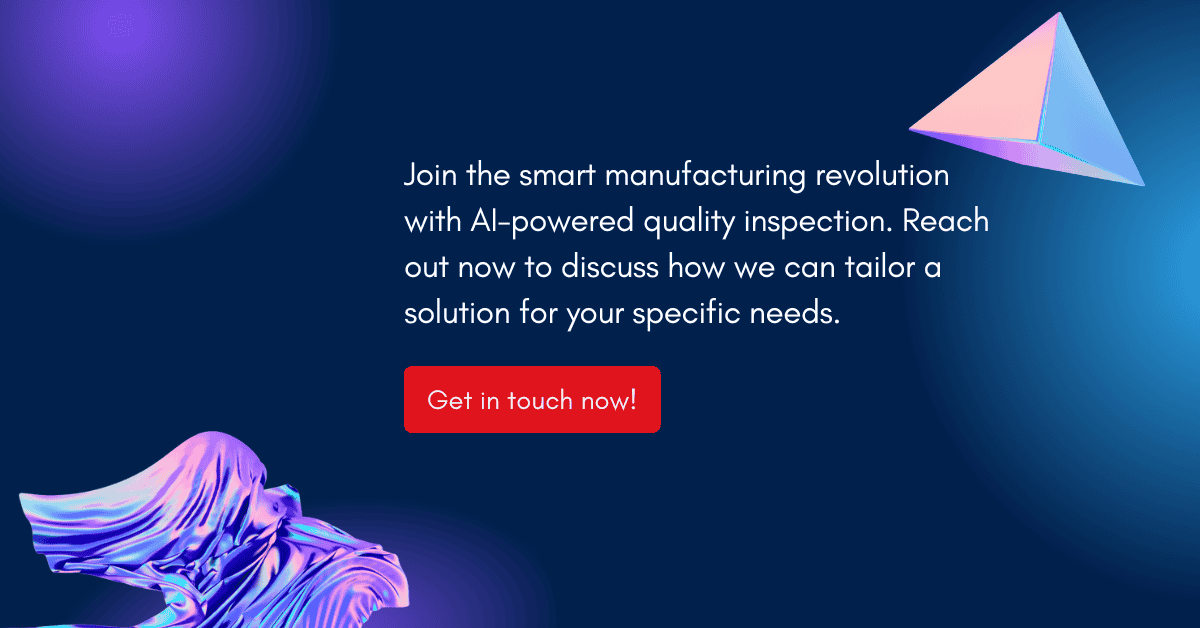
The Future of AI in Quality Control and Inspection
AI-driven quality management is steadily becoming integral to smart manufacturing. According to PwC analysis, AI inspection systems could add over $500 billion in global manufacturing productivity over the next decade.
Here are some innovations that will expand the impact of AI on quality:
- Multimodal data integration - Combining camera data with thermal, ultrasonic, spectroscopy, and other sensing will allow more comprehensive inspection.
- On-device analytics - Quality analysis systems will leverage edge-based analytics to enable real-time decisions without cloud connectivity issues.
- Holistic monitoring - Accumulating lifetime data histories across the supply chain will help predict failure modes and recommend preventative maintenance.
- Generative modeling - GANs and other deep learning techniques can synthesize additional training data to improve model accuracy.
- Simulation environments - Physics-based simulators will generate synthetic manufacturing data to pretrain models and augment real-world datasets.
As AI capabilities grow, these technologies will permeate virtually every link of the manufacturing value chain - from materials sourcing to inventory tracking to predictive maintenance. With reliable machine intelligence safeguarding quality, the future of industrial production looks bright.
So in summary, AI-driven quality control powered by computer vision and deep learning is transforming traditional tedious and inconsistent inspection processes. Automated AI now allows manufacturers to achieve new benchmarks in defect detection, zero-error assembly, reduced rework, and higher customer satisfaction. While deploying these systems comes with some challenges, the benefits far outweigh the effort. With the latest AI techniques, factories can assure perfection in every product that rolls off their lines.
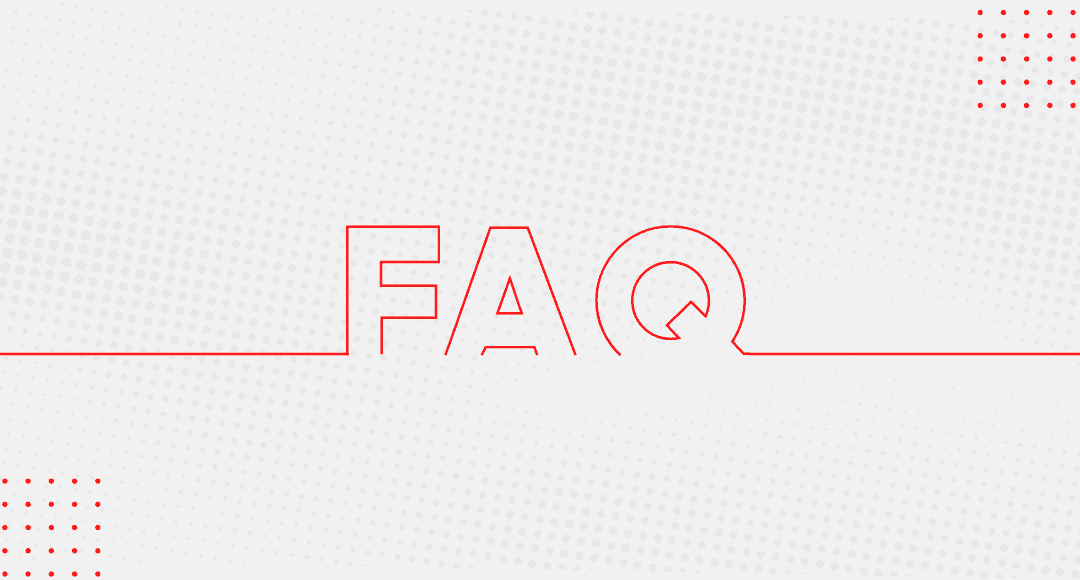
1. What are some key benefits of using AI for quality control in manufacturing?
AI-driven quality control offers several major benefits compared to traditional human inspection:
- Much higher inspection accuracy and consistency in detecting flaws and anomalies. AI models are trained on vast labeled datasets and do not suffer lapses in focus like people.
- Faster inspection time and real-time detection of defects on fast assembly lines. AI systems can analyze images and make pass/fail predictions in under a second.
- Lower operating costs by reducing dependency on large QC teams. Expensive manual rework and scrapping of faulty products is also minimized.
- Continuous operation 24/7 without any downtime or variability in performance. AI systems work round the clock.
- More comprehensive data collection from images, sensors, IoT systems etc. for proactive analysis of quality issues.
- Rapid scalability across multiple production lines and factory locations with centralized model deployment.
2. How much training data is required to implement AI quality inspection for a new product line?
While data needs vary based on product complexity, generally thousands of images are required to train an accurate AI inspection model for a new product:
- Images should cover all angles/sides of the product for complete inspection. Multiple cameras or views are needed.
- Hundreds of images per major defect category are recommended to generalize robustly. Common defects include cracks, dents, surface flaws, shape anomalies etc.
- Both positive (defect-free) and negative (with defect) examples are required for the model to learn effectively.
- Additional data helps deal with product variability. For example, fabrics with different patterns and colors.
- Plan to collect 15-20% more images than immediate training needs to support re-training and model enhancement in the future.
Data collection and labeling is an ongoing activity as products evolve over time. Starting with core products and defects helps build foundation models faster.
3. What infrastructure and skills are required to implement AI quality inspection?
The core infrastructure components required are:
- Cameras and sensors with sufficient resolution and speed to capture clear product images without motion blur. Both standard RGB and specialized cameras like infrared or hyperspectral may be used depending on the application.
- Compute infrastructure like GPU servers to train and deploy AI models. Edge accelerators are also an option for localized inference.
- Connectivity between cameras, local edge devices, and central cloud servers to transmit image data. Both wired and wireless networks may be leveraged.
- Software for modeling, deployment and monitoring including data labeling tools, AI development frameworks like TensorFlow or PyTorch, and visualization dashboards.
Some key skills needed in the team are:
- Computer vision and deep learning expertise to develop, optimize and maintain AI models over time. Both data scientists and ML engineers are critical.
- Edge infrastructure skills to deploy performant inference solutions on local devices.
- Cybersecurity knowledge to transmit, store and serve image data securely.
- Software development capabilities to build custom interfaces and integrations with other factory IT systems.
4. How long does it take to implement an AI quality inspection system for a factory?
For a moderately complex manufacturing process, a typical project timeline is:
- 2-4 weeks for infrastructure installation like cameras, edge devices, networking etc.
- 3-6 weeks for data collection of thousands of product images under diverse conditions. Concurrent labeling activity.
- 4-8 weeks for model development and training iterations before finalizing an optimal CNN architecture.
- 2-3 weeks for integration with related IT systems in the factory including result dashboards.
- 1-2 weeks for user testing and pilot deployment on a portion of the production line.
- 4-6 weeks for full deployment across all stations on the line.
In total, an initial AI quality control system can be operational within 4-6 months for an experienced team with readily available infrastructure and data. Quick wins can be achieved in 2-3 months by focusing on high-impact use cases first.
5. How much does it cost to implement AI quality inspection at a factory?
Costs vary greatly based on factory size, product complexity, quality inspection needs etc. But a sample breakdown for a medium-sized production line is:
- Cameras and sensors - $15,000
- Compute hardware (on-prem servers or cloud) - $5,000 per month
- Software and data labeling - $7,500 setup + $2,500 per month
- Integration services - $20,000
- Team costs - $10,000 per month
So for the first 6 months, approximate costs are $100,000 for setup and $50,000 per month for operations. But this investment can deliver very high ROI - often 3-5X cost reduction from lower defects and rework.
Larger plants with more variabilities may cost 2-3X more than the above estimates. Costs tend to scale sub-linearly due to reuse of models, software, and tooling across lines.
6. How does AI quality inspection integrate with existing manufacturing systems?
Typical integration touchpoints for AI quality inspection data are:
- Live dashboards and defect alerts pushed to mobile devices of production and quality team members on the floor. This facilitates rapid corrective actions.
- Flagging defective products in manufacturing execution system (MES) to prevent further processing and trigger rework.
- Logging all results to centralized quality management system (QMS) for analysis of issues, failure rates, root causes etc.
- Providing inputs for predictive maintenance of machinery based on defect patterns.
- Connecting with ERP or supply chain management systems to adjust production planning based on defect rates.
- Using past data to continuously retrain models for accuracy improvements over time.
The AI system effectively becomes a core component of the broader manufacturing analytics ecosystem to drive higher quality and efficiency.
7. What challenges can arise in implementing AI quality inspection?
Some potential challenges faced by manufacturers are:
- Insufficient or biased training data that fails to adequately represent all product defects and variations. Garbage in, garbage out applies strongly to AI.
- Camera limitations like poor image quality or positioning that hinders defect detection accuracy, requiring revamps.
- Edge hardware limitations that constrain model complexity and throughput for real-time inference.
- Integration complexities with legacy factory systems that run on outdated platforms.
- Organizational resistance from teams worried about losing jobs to automation or lacking trust in AI.
- Compliance requirements around data governance, security, regulatory validation etc. based on industry.
- Model deterioration over time if not periodically retrained on latest data.
However, with the right strategy and expertise, these challenges can be anticipated and managed during the project. Change management and clear communication are also key.
8. How should a factory prioritize which processes to implement AI quality inspection for?
Some criteria for prioritization are:
- Where defect detection rates are currently lowest and quality issues most frequent. Directly improves critical pain points.
- Products with very high-value or stringent quality requirements like electronics or medical devices. AI prevents expensive defects.
- Points where manual inspection slows down production throughput due to complexity. Automates bottleneck.
- Large-scale processes where AI scaled across multiple lines offers highest cost savings. Maximizes ROI.
- Where comprehensive data from AI will most inform other quality initiatives like predictive maintenance and process optimization.
- New products or processes where AI capabilities can be designed in from the start. Avoid retrofitting challenges.
The best results come from piloting AI on limited high-impact use cases and then progressively expanding based on value.
9. How can the accuracy of AI quality inspection models be improved over time?
Some best practices for continuous accuracy improvements are:
- Regularly collect and label new production line data to retrain models on latest conditions.
- Add new defect categories being found on the line to expand model coverage.
- Perform thorough root cause analysis of any errors and correct data issues.
- Use techniques like synthetic data generation to expand model training diversity.
- Evaluate more complex neural network architectures like newer CNNs.
- Tune hyperparameters like learning rate scheduling for better model convergence.
- Blend model outputs with actual inspection results to learn from human reviewer feedback.
- Monitor accuracy KPIs like precision, recall, F1-score etc. to quantify improvements over time.
A culture of constant measurement, experimentation, and refinement drives AI quality inspection maturity.
10. What is the future outlook for AI-driven quality control in manufacturing?
AI quality inspection is poised for massive growth and broader applications including:
- Expanding from visual data to multimodal sensing for defects - thermal, ultrasonic, spectroscopy etc.
- Leveraging edge computing and smart sensors for distributed quality intelligence.
- End-to-end supply chain traceability and monitoring powered by AI and IoT.
- Generative deep learning techniques like GANs to synthesize more training data.
- Simulation and digital twin environments for synthetic defect modeling.
- Knowledge transfer between processes and products using techniques like transfer learning.
- Democratization of quality control from data scientists to business users with low-code/no-code AI tools.
As AI capabilities grow exponentially according to Moore's Law, manufacturers will be able to assure near-perfect quality standards at all stages of production and delivery. This will drive tremendous efficiency, consistency, and customer satisfaction.
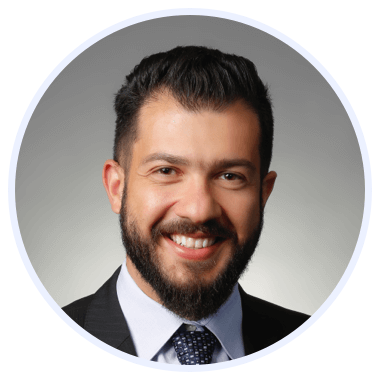
Rasheed Rabata
Is a solution and ROI-driven CTO, consultant, and system integrator with experience in deploying data integrations, Data Hubs, Master Data Management, Data Quality, and Data Warehousing solutions. He has a passion for solving complex data problems. His career experience showcases his drive to deliver software and timely solutions for business needs.