
Automation isn’t new. But intelligent process automation (IPA)? That’s a game changer. For frontline operators, this isn’t about robots replacing jobs. It’s about empowering people—making their work faster, safer, and smarter. And for leaders like COOs and line supervisors, it’s a direct line to greater efficiency and stronger results.
Here’s how AI-driven automation transforms operations on the frontlines.
The Operator’s Burden
Operators are the lifeblood of any organization. Whether it’s managing equipment, assembling parts, or ensuring quality control, their work is crucial. Yet, inefficiencies often weigh them down.
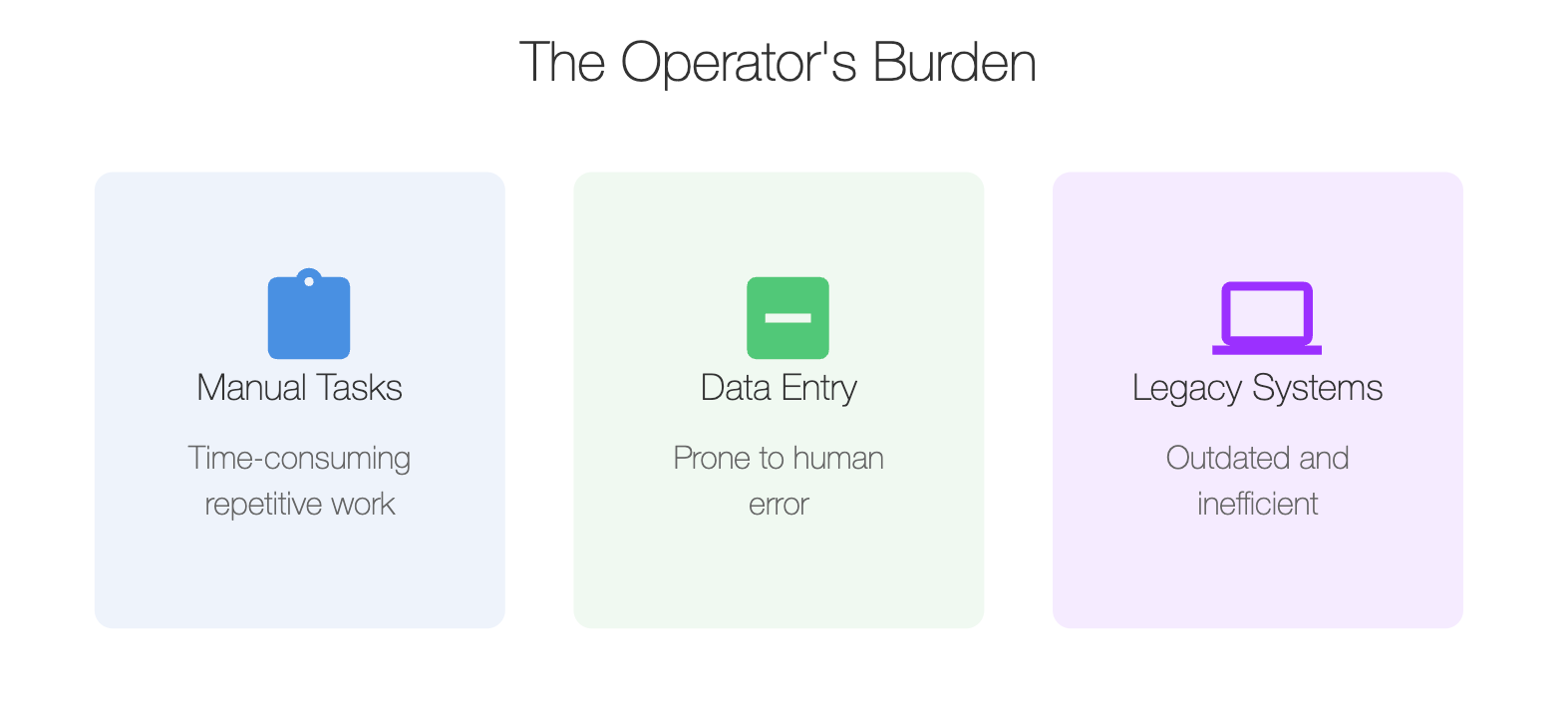
Repetitive tasks consume their time. Manual data entries lead to errors. And outdated systems slow them down. These are more than just annoyances—they’re roadblocks that affect productivity, morale, and ultimately, the bottom line.
Take, for instance, quality inspections. Traditionally, operators rely on manual checks. It’s labor-intensive and prone to human error. One missed defect can lead to expensive recalls or dissatisfied customers. Similarly, managing maintenance schedules often involves juggling spreadsheets or relying on intuition. It’s far from optimal.
These pain points beg for a solution that doesn’t just streamline processes but transforms them. That’s where IPA steps in.
What is Intelligent Process Automation?
Think of IPA as automation’s smarter sibling. It combines technologies like AI, machine learning, and robotic process automation (RPA) to not just execute tasks but to optimize and learn from them.
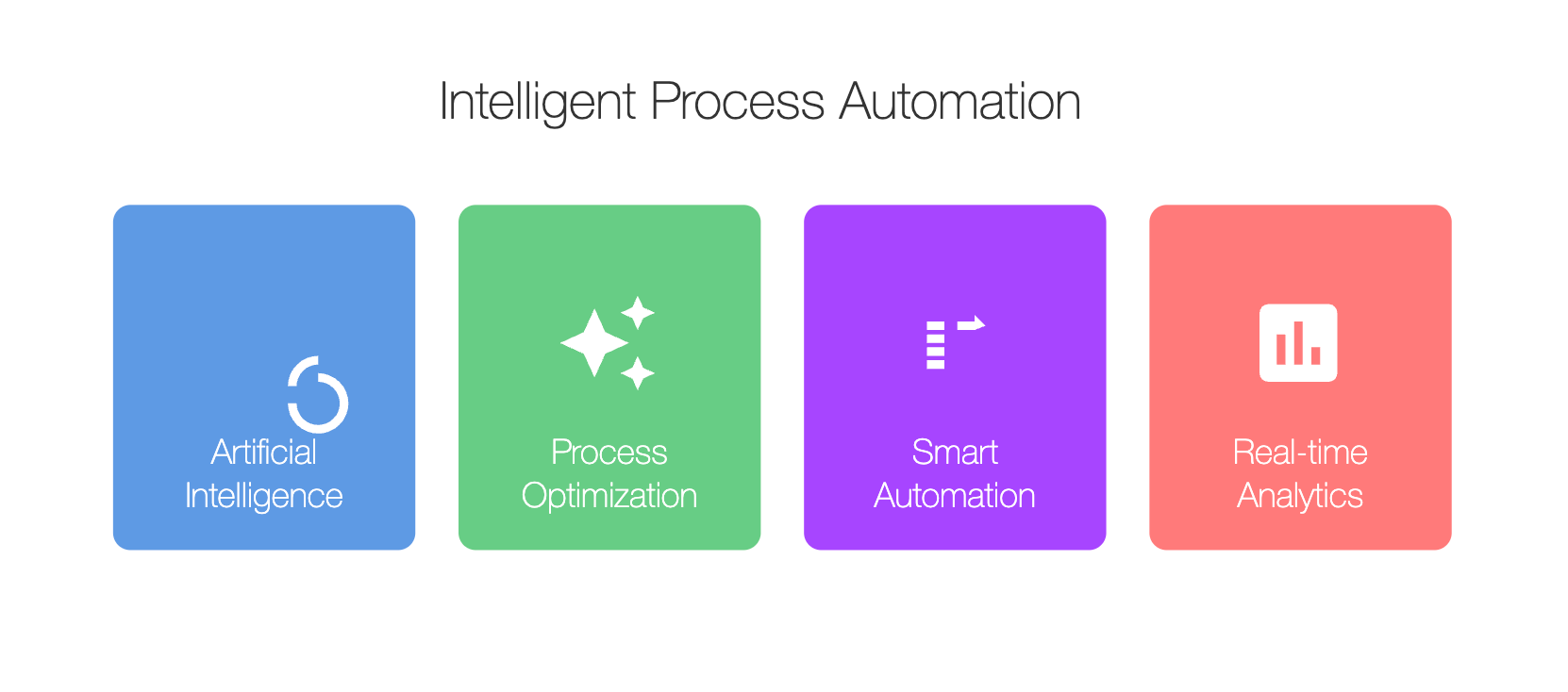
Here’s what makes IPA special:
- AI-Driven Insights: Machine learning algorithms analyze data in real-time, uncovering patterns that humans might miss.
- Dynamic Decision-Making: Unlike static automation, IPA adapts to changes, ensuring flexibility.
- Integration Across Systems: IPA connects different software and hardware seamlessly, creating a unified workflow.
For example, imagine a manufacturing line. With IPA, sensors on equipment continuously feed data to an AI system. This system predicts maintenance needs before breakdowns occur, avoiding costly downtime. Or think about inventory management—instead of manual counts, AI tracks stock levels, automatically reordering when needed.
The result? Operators spend less time on mundane tasks and more on strategic activities. COOs see fewer disruptions and smoother operations.
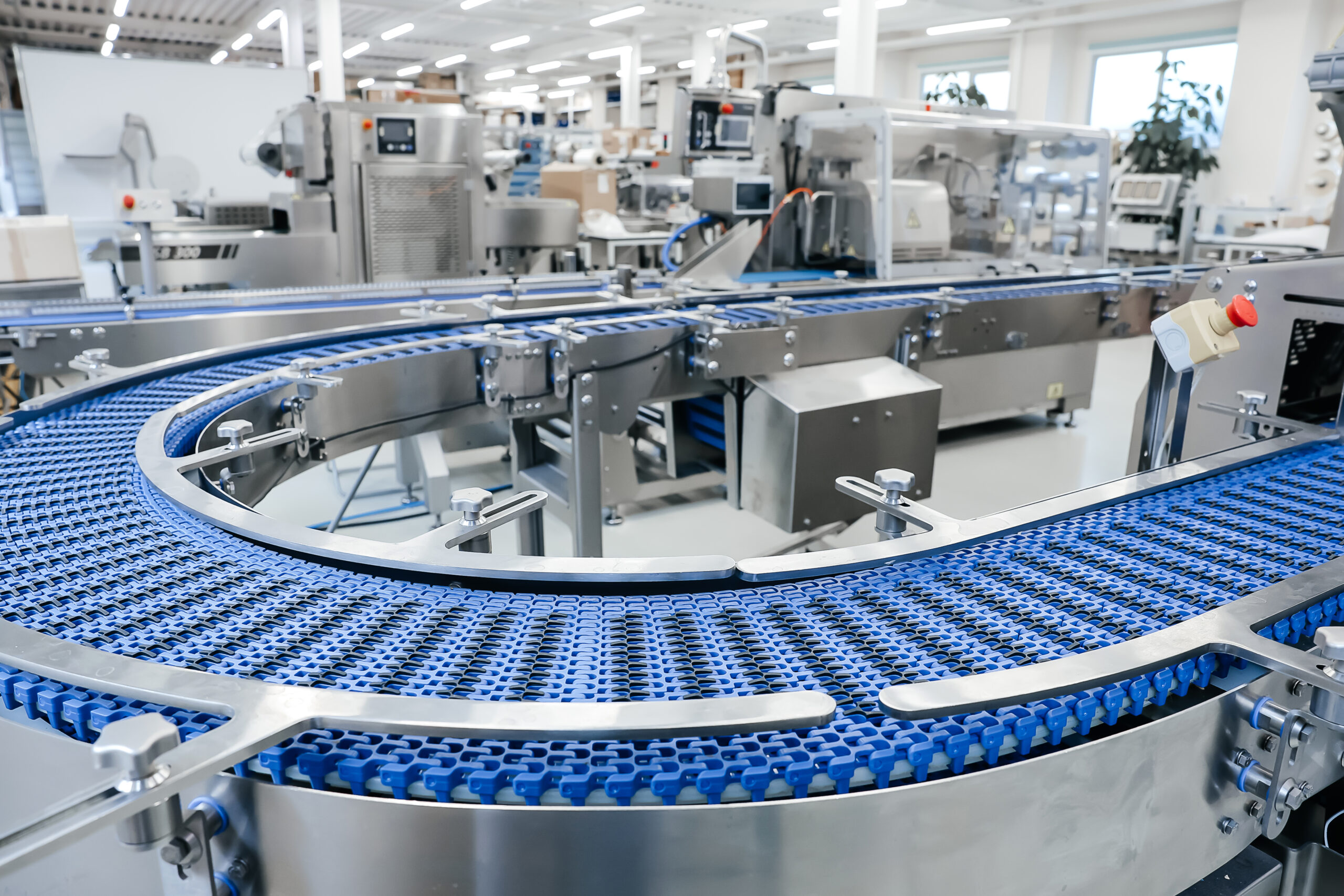
Real-World Benefits of IPA
The impact of IPA isn’t theoretical. It’s measurable, tangible, and transformative.
Increased Efficiency
Automation eliminates repetitive tasks. AI ensures precision. Together, they free up operators to focus on high-value activities.
One example comes from a mid-sized manufacturing firm. By implementing IPA, they reduced manual quality checks by 60%, reallocating that time to process improvement initiatives. This didn’t just boost productivity—it enhanced job satisfaction by removing mundane, repetitive work.
Improved Safety
For frontline workers, safety is paramount. IPA enhances this in multiple ways. AI can monitor workplace conditions in real-time, flagging potential hazards before they become incidents. Automation can also handle dangerous tasks, reducing the risk to human operators.
Take an oil and gas company that adopted IPA for equipment inspections. Instead of sending operators into potentially hazardous environments, drones equipped with AI-powered cameras performed the checks. Not only was the process faster, but it also significantly reduced workplace injuries.
Enhanced Decision-Making
Data drives decisions. But raw data is only as good as the insights you draw from it. IPA doesn’t just collect data—it interprets it, offering actionable recommendations.
Consider a logistics company struggling with delivery delays. By using IPA, they analyzed routes, traffic patterns, and driver behavior. The AI suggested optimized routes, cutting delivery times by 25%. Operators didn’t need to sift through mountains of data—the system did it for them, offering clear, actionable insights.
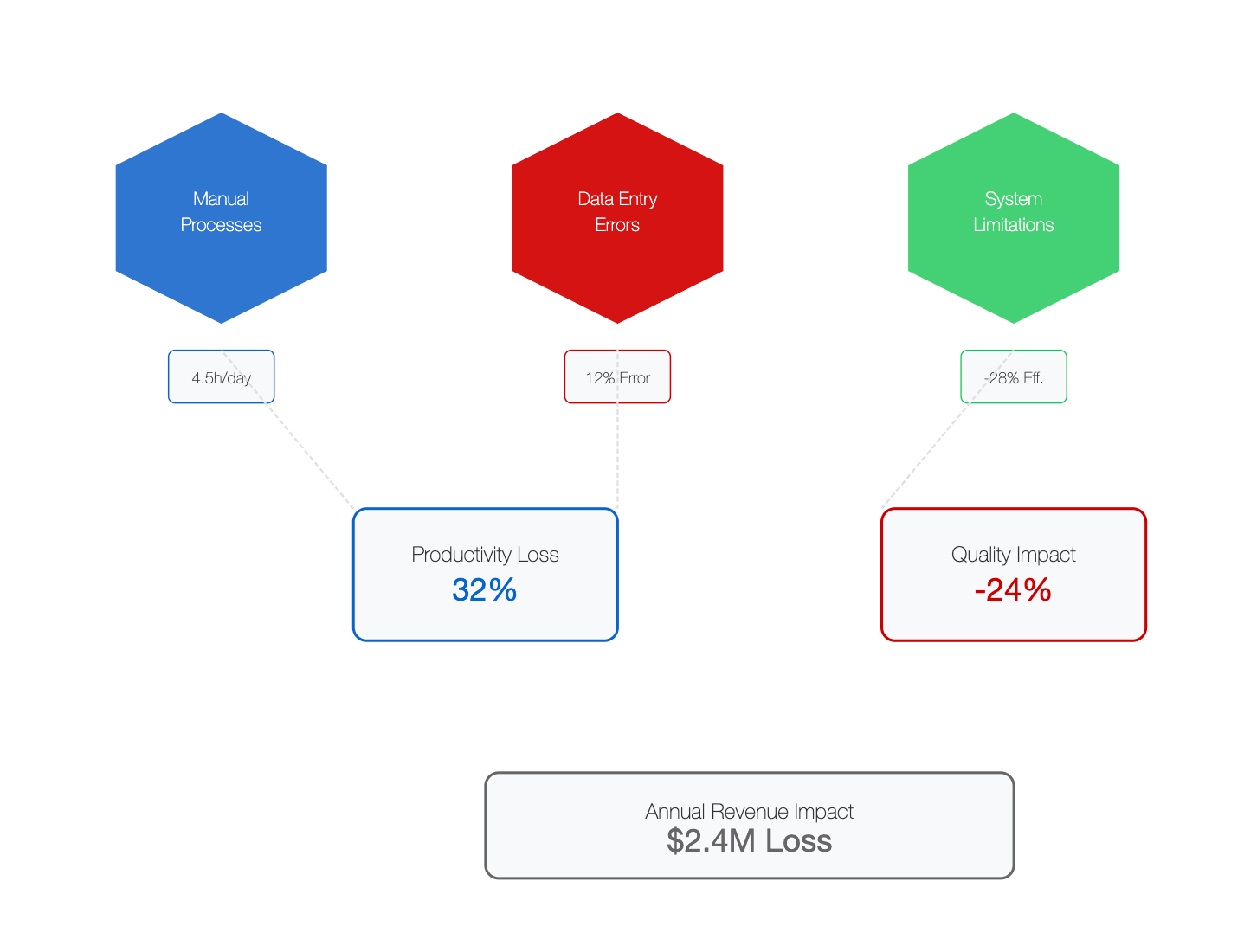
Cost Savings
Efficiency and safety improvements naturally lead to cost reductions. Whether it’s fewer errors, less downtime, or reduced waste, IPA’s financial impact is undeniable.
A real-world example? A retail chain used IPA to manage inventory. The AI system reduced overstock by 20%, cutting storage costs and freeing up capital. Across 50 stores, the savings ran into millions.
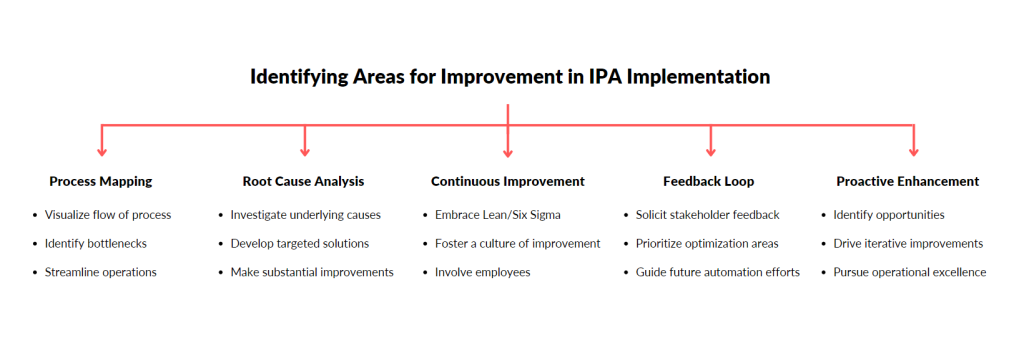
Implementing IPA: Steps for Success
Transitioning to IPA requires more than just adopting new tools. It demands a strategic approach. Here’s how to do it right:
1. Identify Pain Points
Start by mapping out operational inefficiencies. Where are operators spending too much time? What tasks are prone to errors? These pain points will guide your IPA implementation.
2. Choose the Right Technology
Not all IPA solutions are created equal. Look for tools that integrate seamlessly with your existing systems. Prioritize flexibility and scalability—your needs today might evolve tomorrow.
3. Engage Operators
Change can be daunting. Involve operators from the start. Show them how IPA will make their jobs easier, not replace them. Training and open communication are key.
4. Monitor and Optimize
IPA isn’t a set-it-and-forget-it solution. Continuously monitor performance, gather feedback, and refine processes. The goal is continuous improvement.
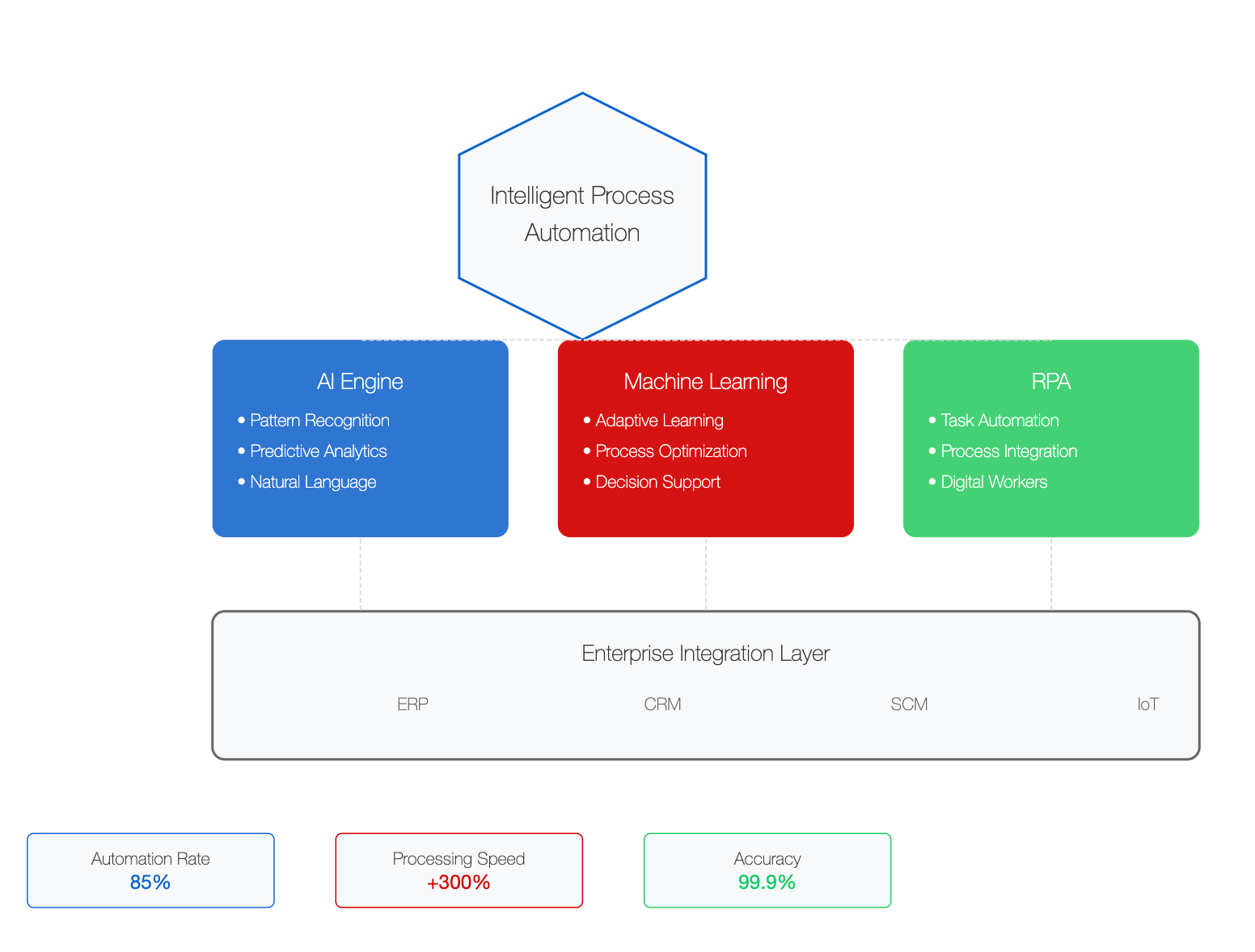
Challenges and How to Overcome Them
Like any innovation, IPA comes with challenges. But understanding them upfront helps mitigate risks.
Resistance to Change
Operators might fear automation will replace their jobs. COOs need to frame IPA as a tool for empowerment, not replacement. Highlight success stories and provide hands-on training.
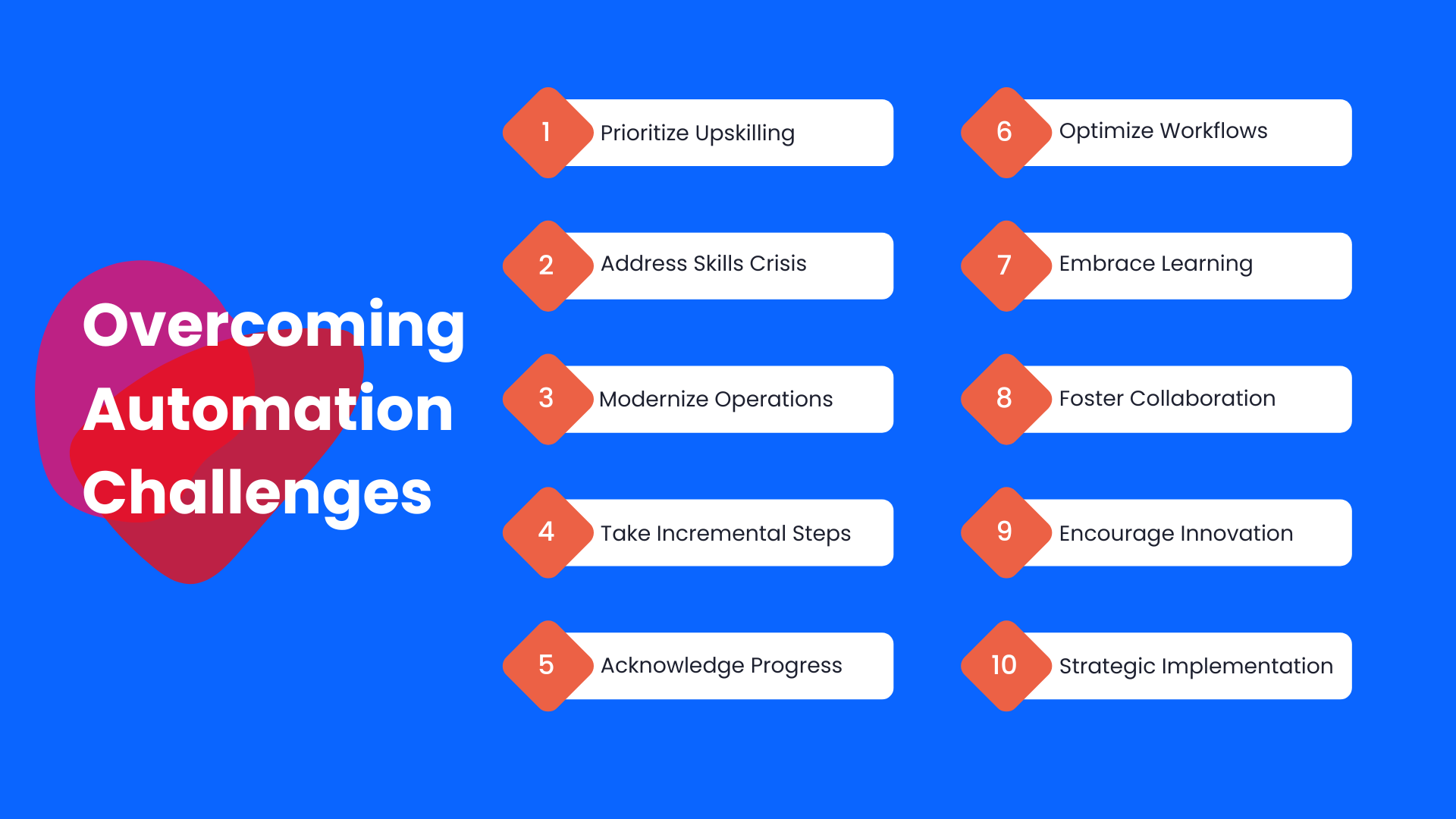
Integration Issues
Legacy systems can pose hurdles. Invest in solutions that prioritize interoperability. And don’t shy away from overhauling outdated processes if needed.
Initial Costs
While IPA delivers long-term savings, the upfront investment can be significant. Build a solid business case, highlighting ROI through case studies and projected savings.
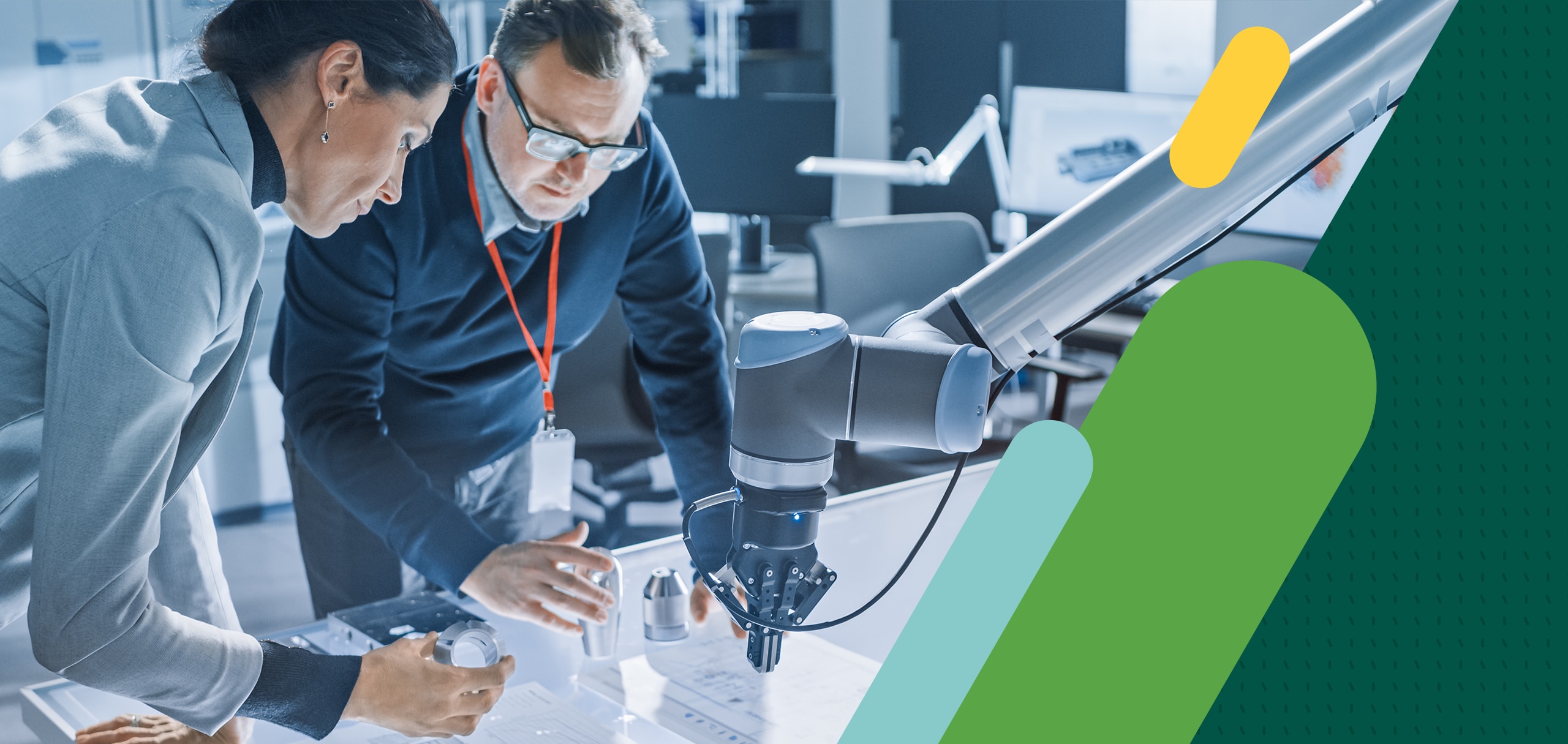
The Future of Work with IPA
IPA is not just a trend. It’s the future of efficient operations. For frontline operators, it’s about removing barriers and enabling them to excel. For COOs, it’s a strategic advantage—a way to drive growth and innovation.
The journey to IPA might seem daunting, but the rewards are worth it. Reduced inefficiencies, improved safety, better decisions, and significant cost savings—these aren’t just possibilities. They’re outcomes that companies around the world are already experiencing.
As someone passionate about transforming operations, I’ve seen firsthand how IPA reshapes industries. It’s not just about doing more with less. It’s about doing better, smarter, and faster. Let’s embrace this opportunity to elevate operations and empower people.
Ready to explore how IPA can transform your operations? Let’s connect and turn challenges into opportunities.
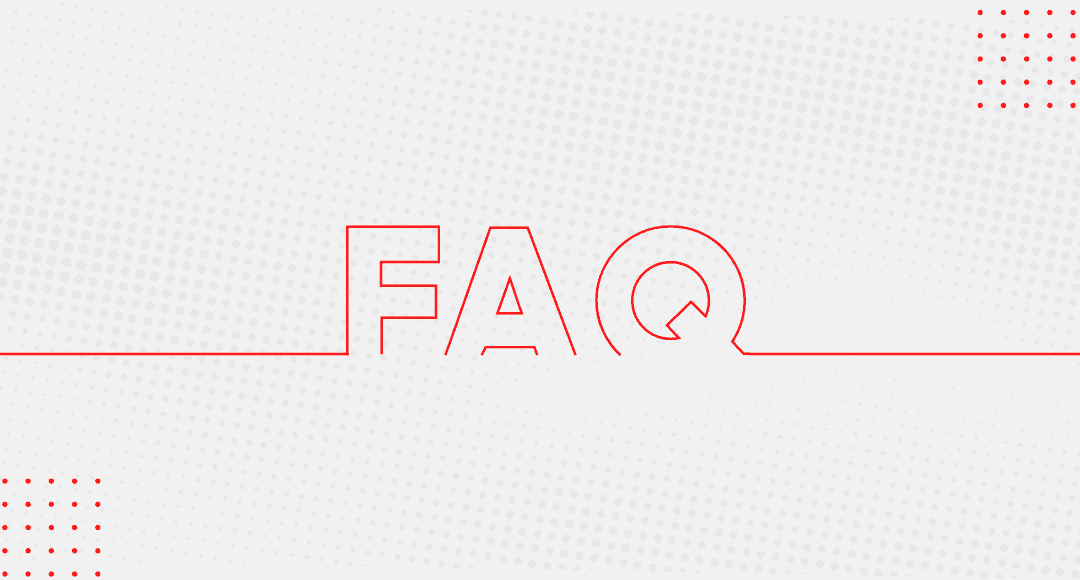
1. What is Intelligent Process Automation (IPA)?
Intelligent Process Automation (IPA) combines traditional automation with advanced technologies like AI and machine learning. It doesn’t just execute repetitive tasks; it learns, adapts, and optimizes workflows. IPA is designed to streamline processes, reduce errors, and enhance decision-making across operations.
2. How does IPA differ from traditional automation?
Traditional automation follows static, rule-based processes. It can’t adapt to changes or analyze data for insights. IPA, on the other hand, integrates AI and machine learning to adapt dynamically, make data-driven decisions, and continuously improve workflows.
3. What are the key benefits of IPA for frontline operators?
IPA reduces repetitive manual tasks, enabling operators to focus on strategic and value-driven activities. It improves safety by automating hazardous tasks, enhances accuracy through AI precision, and provides real-time insights for better decision-making. This leads to higher efficiency, reduced errors, and greater job satisfaction.
4. How does IPA improve workplace safety?
IPA enhances safety by automating dangerous tasks such as equipment inspections in hazardous environments. For instance, AI-powered drones can replace human inspections in high-risk areas. It also monitors workplace conditions in real-time, flagging risks before they escalate into incidents.
5. Can IPA work with legacy systems?
Yes, many IPA solutions are designed to integrate with legacy systems. However, seamless integration depends on the tools selected and the existing infrastructure. Companies may need to upgrade or modernize certain systems to maximize the benefits of IPA.
6. Will IPA replace frontline operators?
IPA is not about replacing workers; it’s about empowering them. By handling repetitive and mundane tasks, IPA allows operators to focus on more complex and rewarding activities. It’s a tool for job enhancement, not displacement, and often leads to higher job satisfaction.
7. What challenges can companies face when implementing IPA?
Key challenges include resistance to change among employees, integration with legacy systems, high upfront costs, and potential data privacy concerns. These challenges can be mitigated with proper planning, communication, training, and selecting the right IPA tools.
8. How can a company calculate the ROI of IPA implementation?
To calculate ROI, consider the time and cost savings from automation, reductions in errors and downtime, and efficiency gains in workflows. Compare these benefits with the initial investment in IPA tools and infrastructure. Many companies experience significant cost savings and productivity improvements within months of implementation.
9. What industries benefit the most from IPA?
Industries with repetitive tasks, high data processing needs, and complex workflows benefit greatly from IPA. These include manufacturing, logistics, healthcare, retail, and financial services. IPA’s ability to adapt and optimize processes makes it versatile across sectors.
10. How should a company start its IPA journey?
Begin by identifying pain points and inefficiencies in your operations. Choose IPA tools that align with your needs and ensure they integrate well with your systems. Engage your team early, providing clear communication and training to build confidence in the new processes. Start with a pilot project to demonstrate value and gradually scale up. Monitoring and optimizing continuously will ensure long-term success.
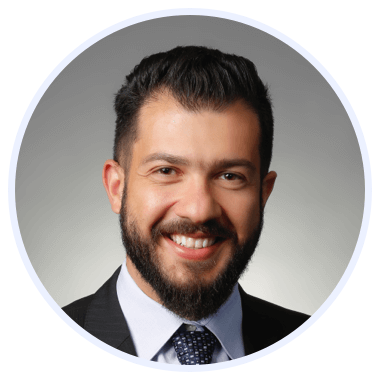
Rasheed Rabata
Is a solution and ROI-driven CTO, consultant, and system integrator with experience in deploying data integrations, Data Hubs, Master Data Management, Data Quality, and Data Warehousing solutions. He has a passion for solving complex data problems. His career experience showcases his drive to deliver software and timely solutions for business needs.