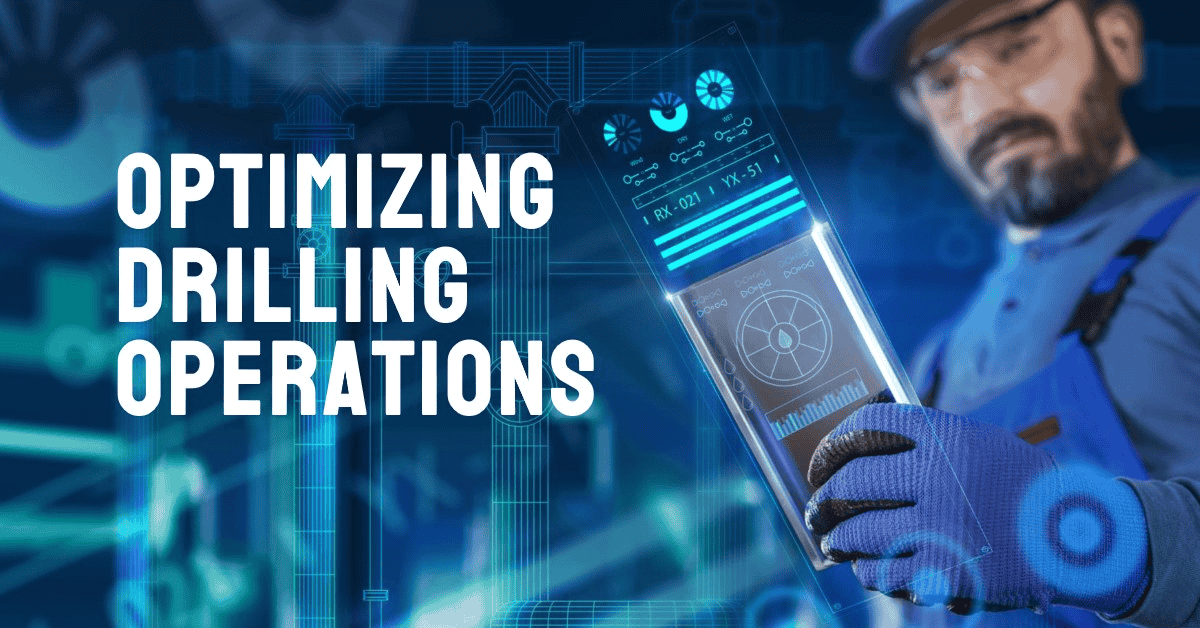
As the oil and gas industry continues to face unprecedented challenges, including volatile market conditions, increasing operational costs, and mounting environmental pressures, companies are turning to advanced technologies to optimize their operations and maintain a competitive edge. One area that holds immense potential for improvement is drilling operations, where equipment failures and unplanned downtime can lead to significant financial losses and safety risks. This is where predictive maintenance powered by large language models (LLMs) comes into play.
In this blog post, we will explore how LLMs can revolutionize predictive maintenance in drilling operations, drawing on real-world examples and best practices from industry leaders. As the CEO of Capella, a data management company, I have witnessed firsthand the transformative impact of LLMs on various sectors, and I am excited to share my insights with senior executives and decision-makers in the oil and gas industry.
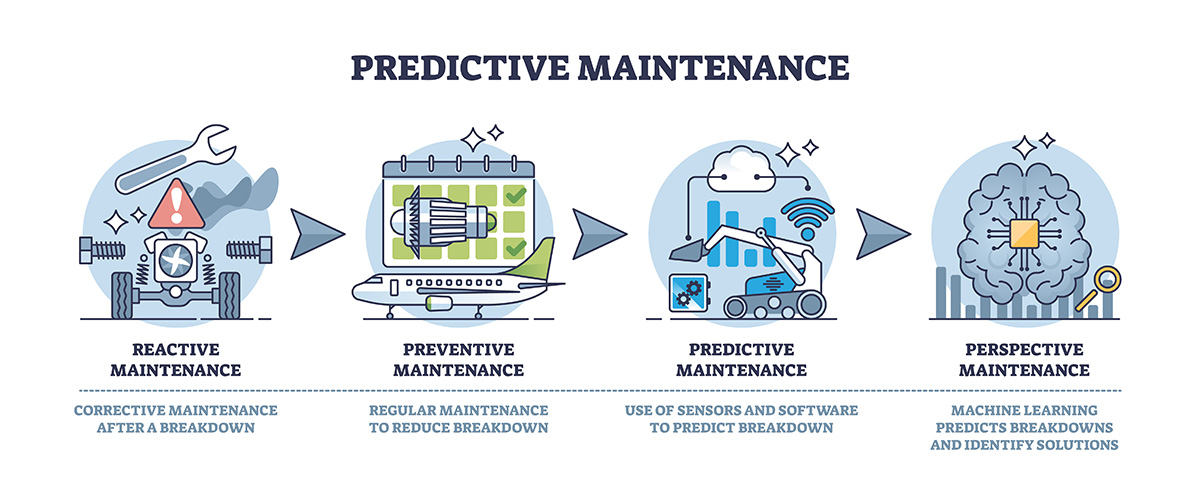
Predictive Maintenance and Its Potential in Drilling Operations
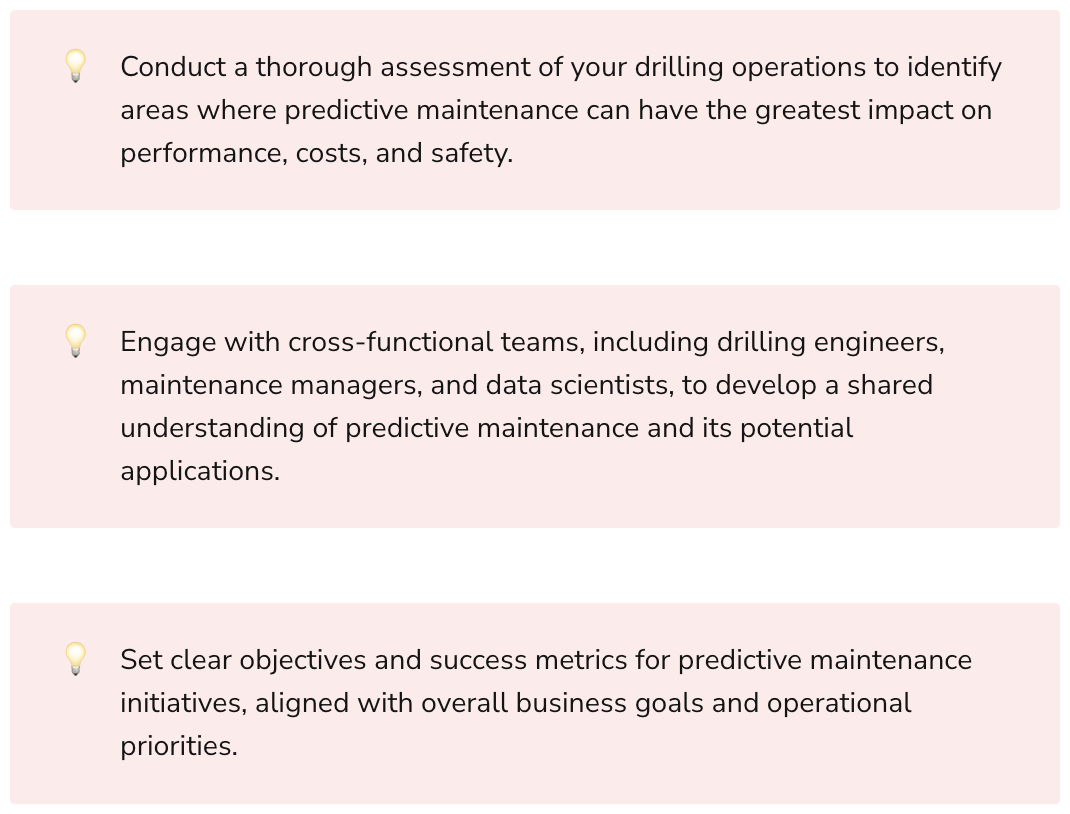
Predictive maintenance is a proactive approach to equipment management that employs data analytics, machine learning, and domain expertise to anticipate and prevent failures before they occur. By continuously monitoring the health and performance of critical assets, such as drilling rigs, mud pumps, and top drives, predictive maintenance enables companies to optimize maintenance schedules, reduce downtime, and extend equipment life.
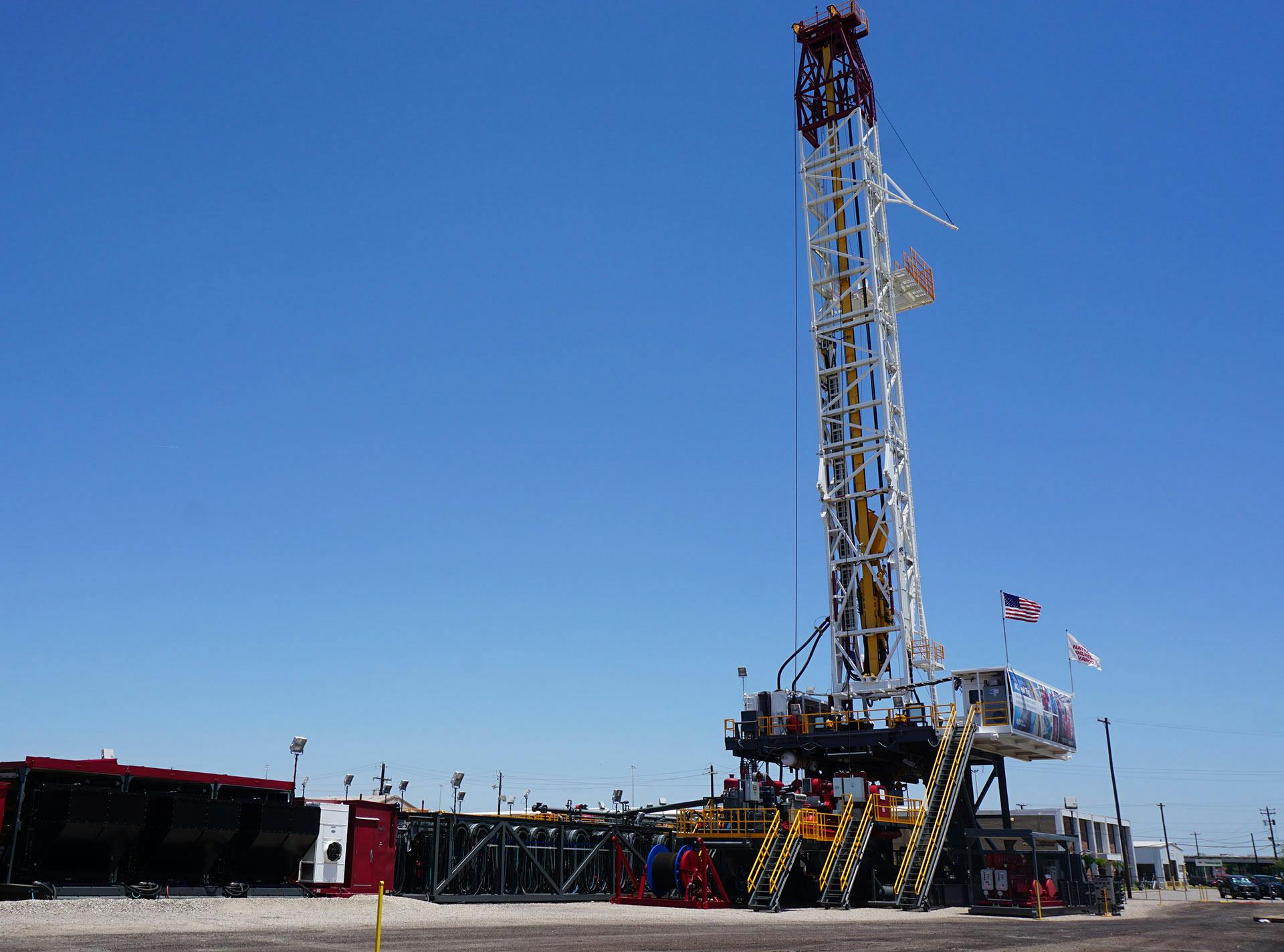
In the context of drilling operations, predictive maintenance can address a wide range of challenges, including:
- Unplanned downtime due to equipment failures
- High maintenance costs and spare parts inventory
- Inefficient maintenance scheduling and resource allocation
- Safety risks associated with equipment malfunctions
- Lack of visibility into asset health and performance
By tapping into the power of LLMs, which are advanced AI models trained on vast amounts of text data, companies can unlock new insights and capabilities in predictive maintenance. LLMs can process and analyze diverse data sources, such as sensor readings, maintenance logs, and operator notes, to identify patterns, anomalies, and risk factors that may indicate impending failures.
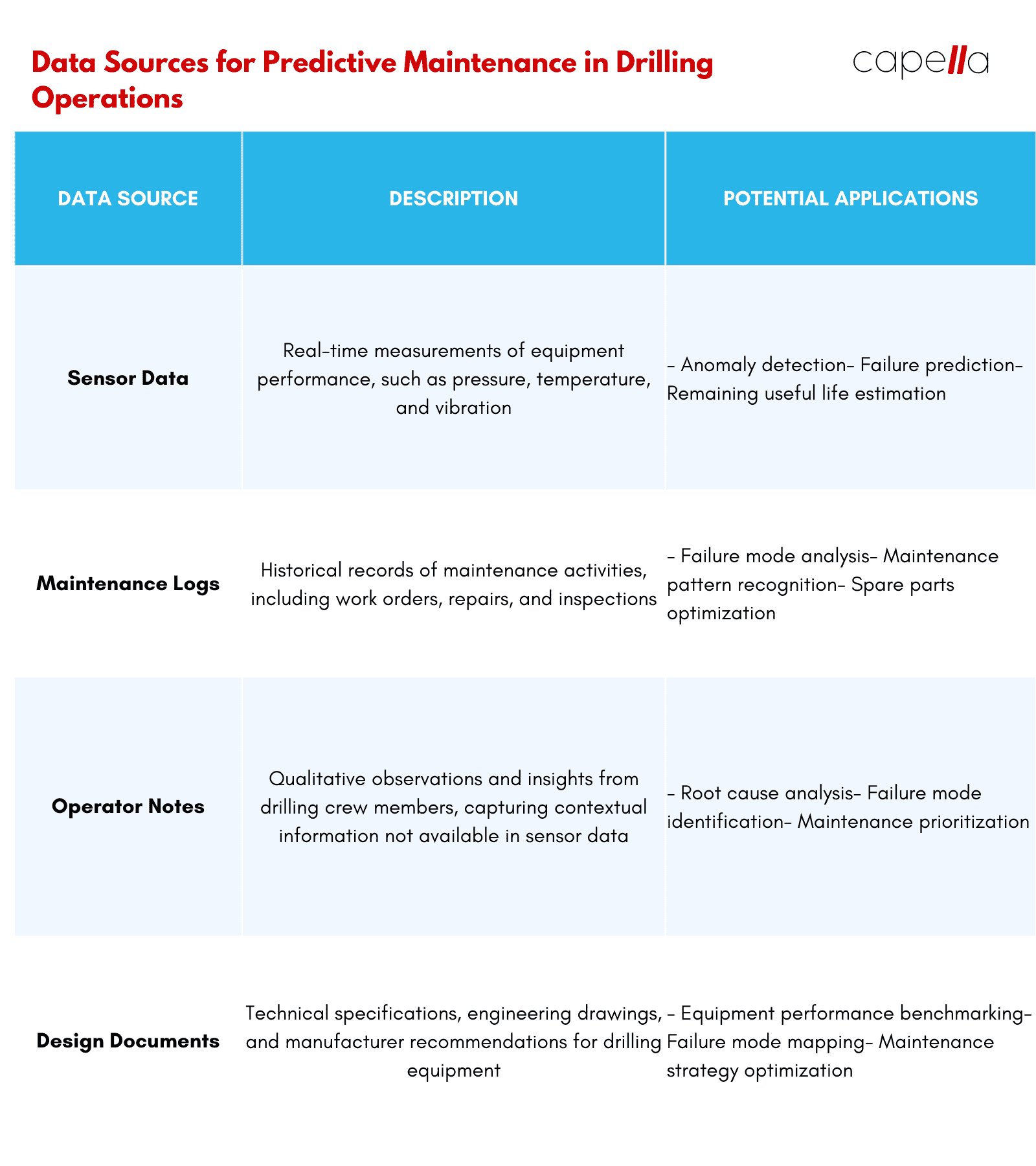
Real-World Examples of LLM-Powered Predictive Maintenance in Action
Several leading oil and gas companies have already begun to embrace LLMs for predictive maintenance in their drilling operations, with impressive results. For example:
- Shell has partnered with C3.ai to develop an AI-powered predictive maintenance platform for its drilling rigs. By analyzing sensor data from critical equipment, such as top drives and mud pumps, the platform can predict failures up to 60 days in advance, enabling proactive maintenance and reducing downtime by up to 80%.
- Equinor has implemented a predictive maintenance solution for its offshore drilling operations, using LLMs to process and analyze data from various sources, including maintenance logs, work orders, and real-time sensor data. The solution has helped Equinor reduce unplanned downtime by 30% and increase equipment availability by 5%.
- Schlumberger has developed a predictive maintenance platform called DELFI, which uses LLMs to analyze data from drilling equipment, such as BOP (blowout preventer) systems and subsea trees. By predicting potential failures and optimizing maintenance schedules, DELFI has helped customers reduce unplanned downtime by up to 50% and lower maintenance costs by 20%.
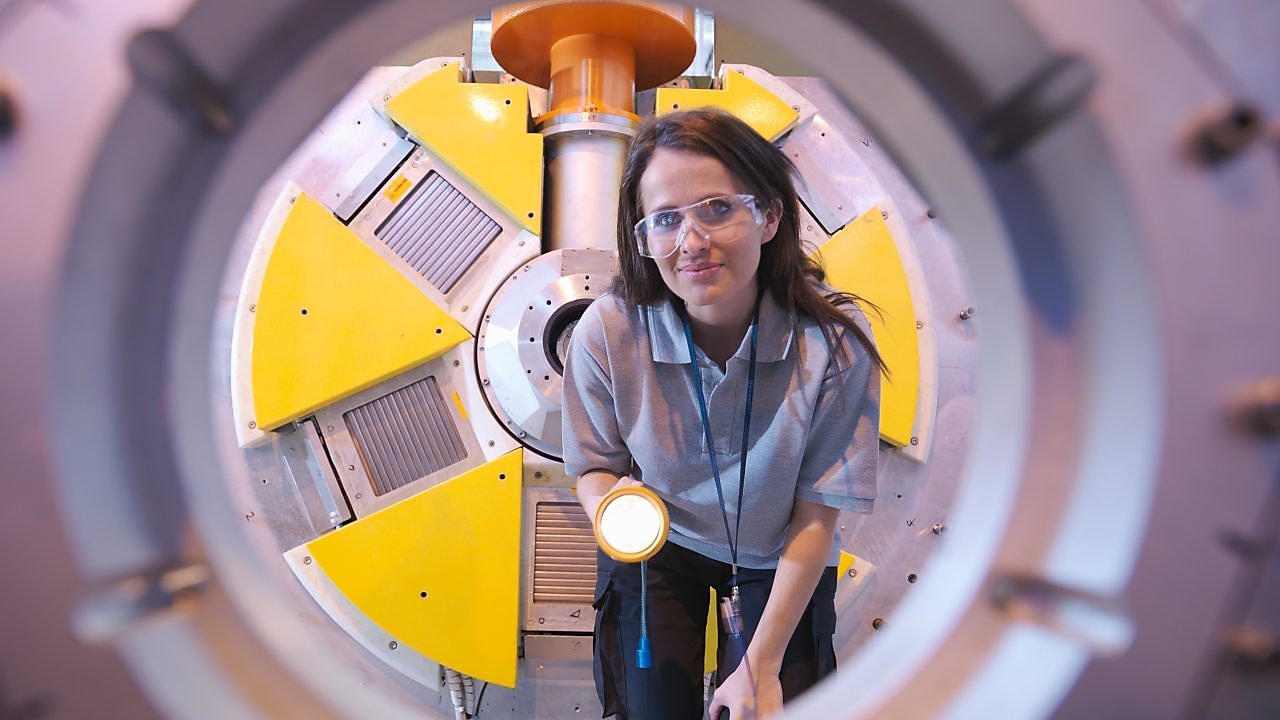
These examples demonstrate the tangible benefits of LLM-powered predictive maintenance in drilling operations, from reduced downtime and maintenance costs to improved equipment reliability and safety.

Benefits of LLM-Powered Predictive Maintenance in Drilling Operations
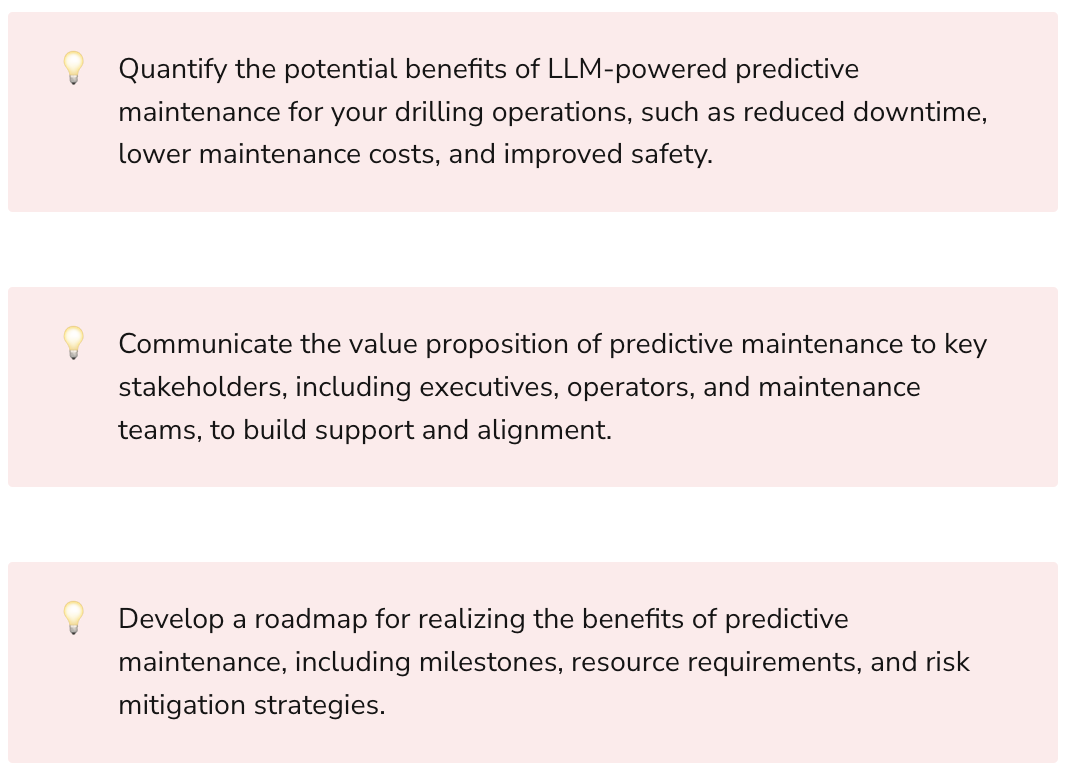
Implementing LLMs for predictive maintenance in drilling operations can yield a wide range of benefits, including:
Reduced Downtime: By predicting potential failures and scheduling maintenance proactively, companies can minimize unplanned downtime and keep their drilling rigs running smoothly.
Improved Equipment Reliability: LLMs can help identify and address potential issues before they escalate into major failures, extending the life of critical equipment and reducing the risk of catastrophic events.
Lower Maintenance Costs: Predictive maintenance enables companies to optimize their maintenance schedules and spare parts inventory, reducing overall maintenance costs and avoiding unnecessary repairs.
Enhanced Safety: By preventing equipment malfunctions and failures, LLM-powered predictive maintenance can help create a safer working environment for drilling crews and minimize the risk of accidents and injuries.
Increased Operational Efficiency: With better visibility into asset health and performance, companies can make data-driven decisions to optimize their drilling operations, from well planning to rig deployment and crew scheduling.
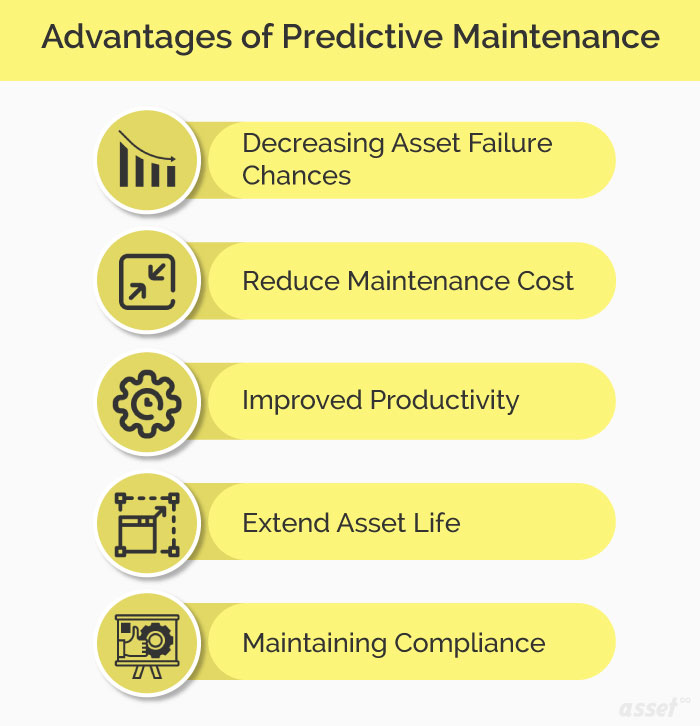
Implementing LLMs for Predictive Maintenance: Technical Considerations and Best Practices
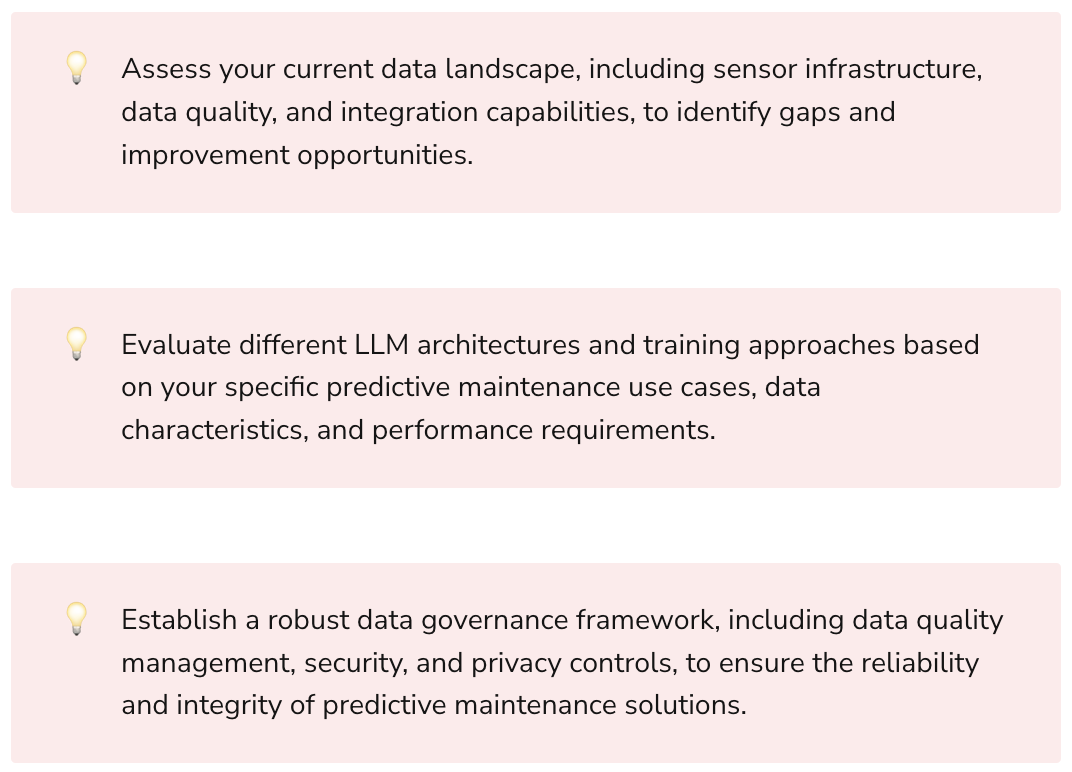
To successfully implement LLMs for predictive maintenance in drilling operations, companies need to consider several technical aspects and follow best practices, including:
Data Requirements and Preprocessing
LLMs require vast amounts of high-quality data to learn patterns and make accurate predictions. In the context of drilling operations, this data can come from various sources, such as:
- Sensor data from critical equipment (e.g., pressure, temperature, vibration)
- Maintenance logs and work orders
- Operator notes and observations
- Equipment specifications and design documents
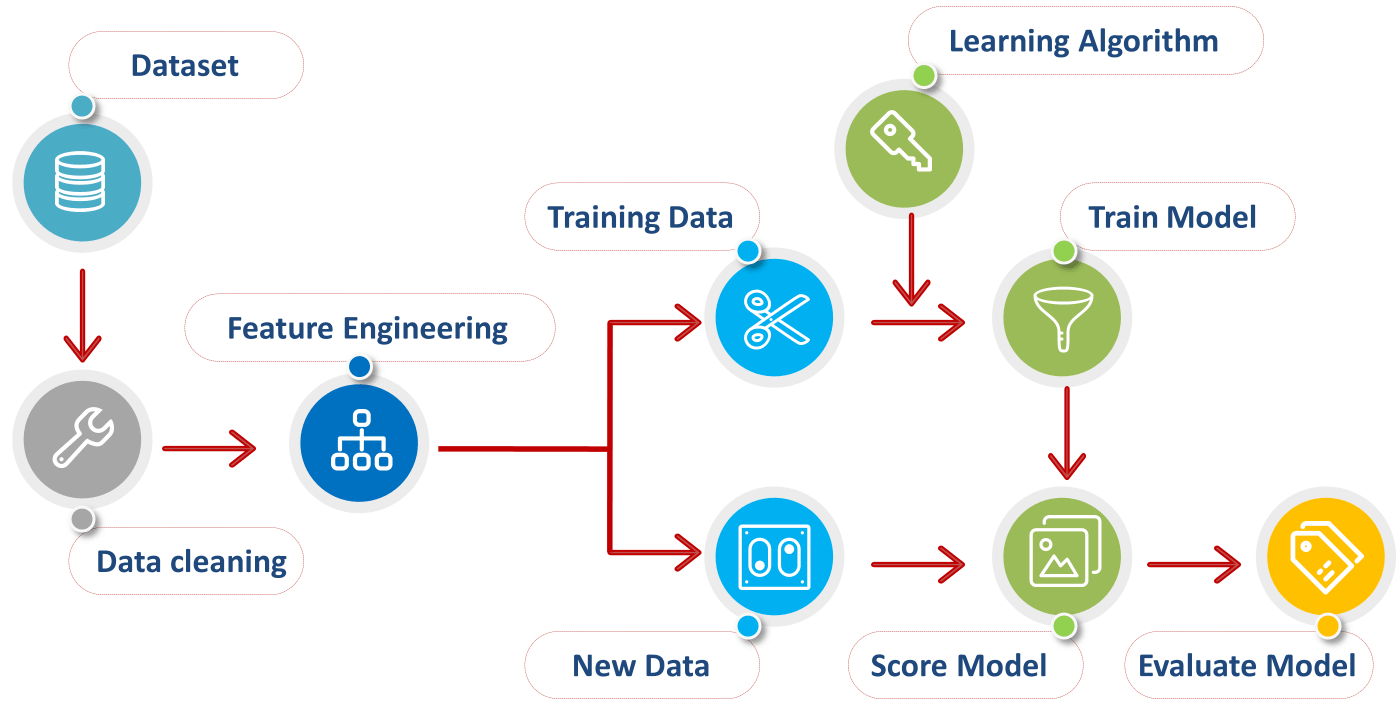
Before feeding this data into LLMs, it needs to be preprocessed and cleaned to ensure consistency, accuracy, and relevance. This may involve tasks such as data normalization, outlier detection, and feature engineering.
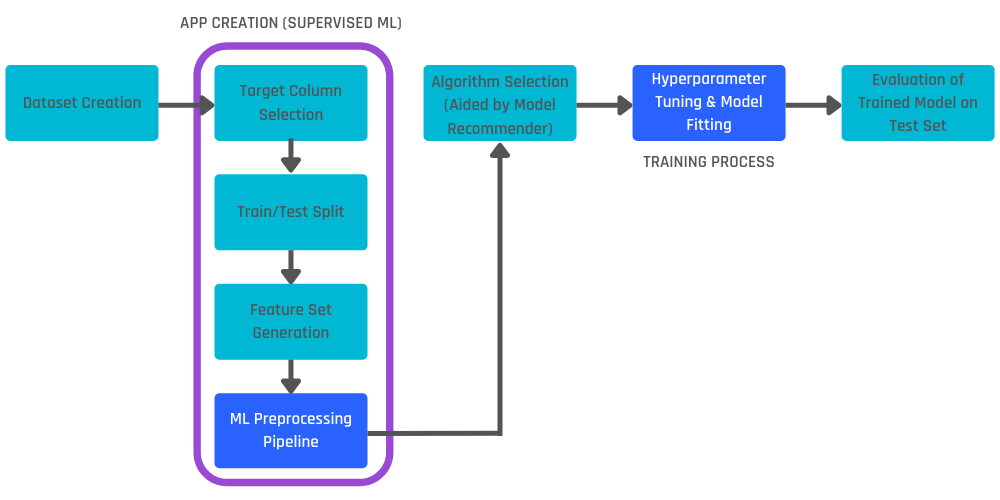
Model Selection and Training
Choosing the right LLM architecture and training approach is crucial for building effective predictive maintenance solutions. Some popular LLM architectures for this task include:
- Transformer-based models (e.g., BERT, GPT)
- Recurrent neural networks (RNNs)
- Long short-term memory (LSTM) networks
When training LLMs for predictive maintenance, it is important to:
- Use a sufficiently large and diverse dataset that covers various failure modes and operating conditions
- Employ techniques such as transfer learning and fine-tuning to adapt pre-trained LLMs to the specific domain and task
- Optimize hyperparameters, such as learning rate, batch size, and regularization, to achieve the best performance
- Evaluate model performance using relevant metrics, such as precision, recall, and F1 score
Integration with Existing Systems and Workflows
To maximize the impact of LLM-powered predictive maintenance, it is essential to integrate the solution with existing drilling workflows and maintenance management systems, such as:
- SCADA (Supervisory Control and Data Acquisition) systems
- EAM (Enterprise Asset Management) platforms
- CMMS (Computerized Maintenance Management Systems)
This integration enables seamless data flow, real-time monitoring, and actionable insights for maintenance teams and decision-makers.
Collaboration Between Domain Experts and Data Scientists
Building effective predictive maintenance solutions requires close collaboration between domain experts, such as drilling engineers and maintenance managers, and data scientists who specialize in LLMs and AI.
Domain experts bring valuable insights into equipment behavior, failure modes, and maintenance practices, while data scientists contribute their expertise in data analytics, model development, and deployment.
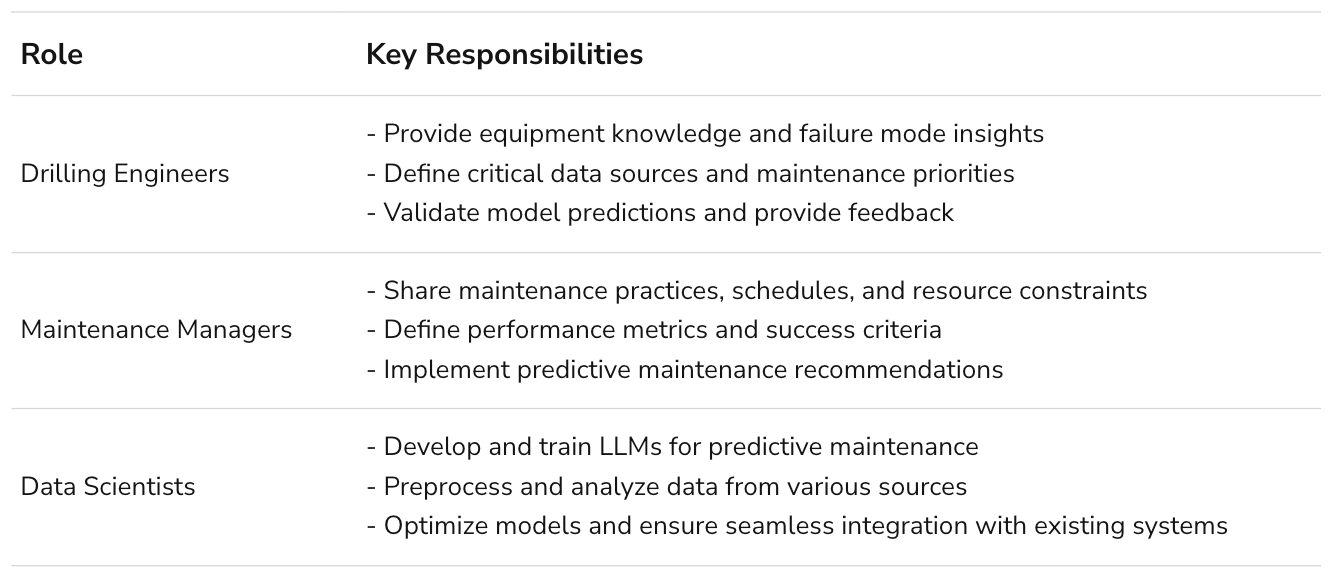
By fostering open communication, knowledge sharing, and iterative development, this cross-functional collaboration can lead to more accurate, reliable, and actionable predictive maintenance solutions.
Emerging Trends and Techniques in LLMs for Predictive Maintenance
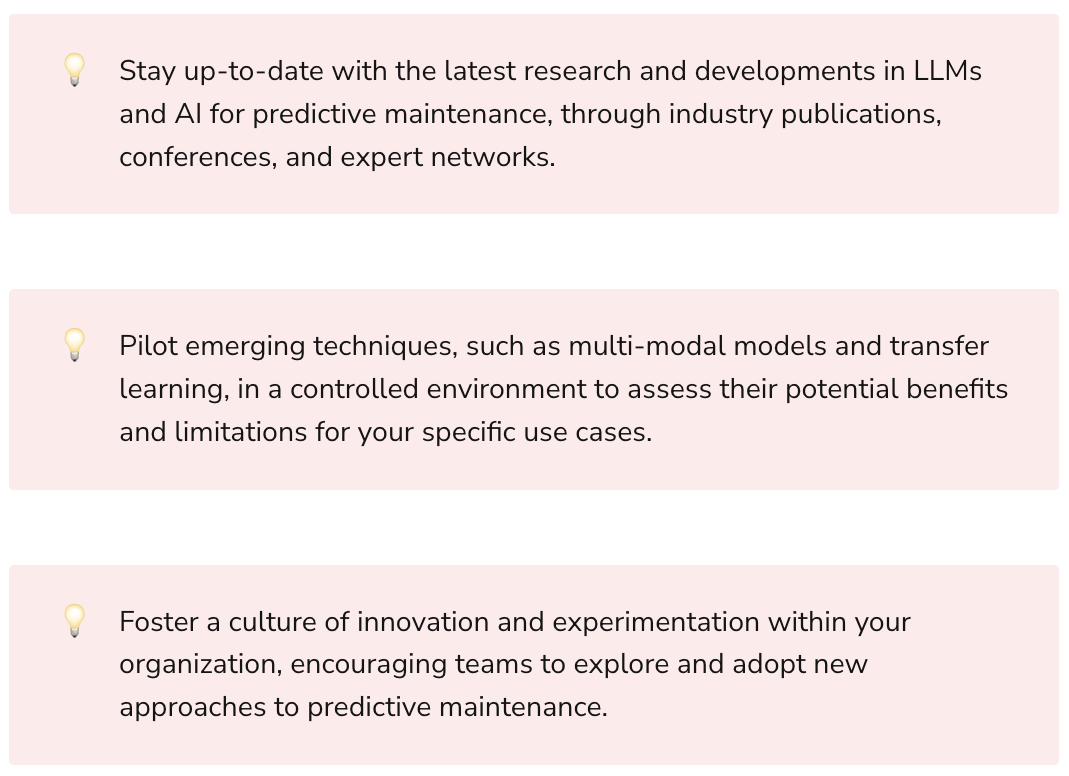
As LLMs continue to evolve, several emerging trends and techniques hold promise for further enhancing predictive maintenance in drilling operations, including:
Multi-modal Models: LLMs that can process and analyze multiple data modalities, such as text, images, and time-series data, can provide a more comprehensive understanding of equipment health and failure modes.
Transfer Learning: By deploying pre-trained LLMs and adapting them to specific domains and tasks, companies can accelerate the development of predictive maintenance solutions and achieve better performance with limited data.
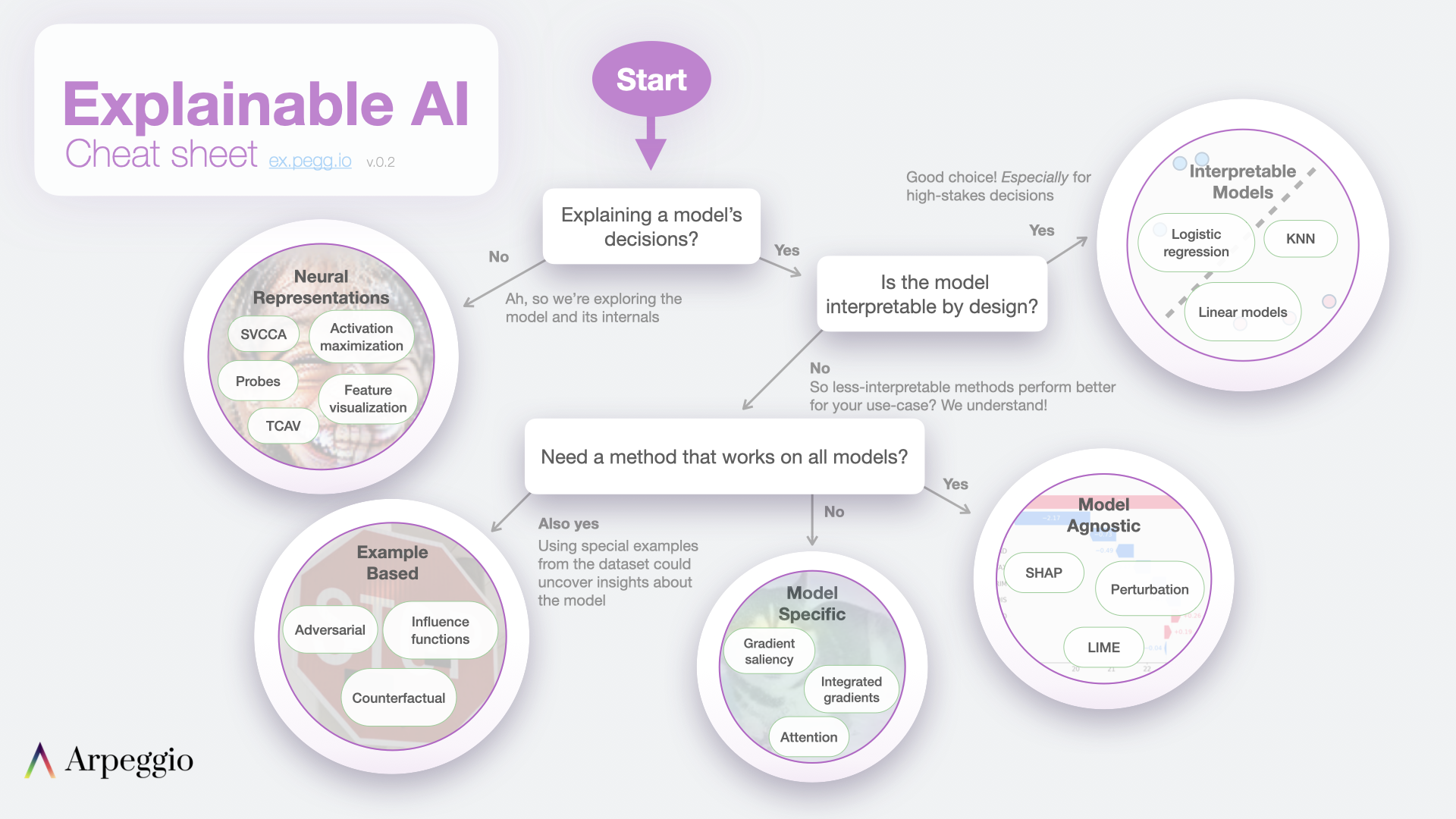
Explainable AI: As predictive maintenance solutions become more complex, it is crucial to ensure that their predictions and recommendations are transparent and interpretable. Explainable AI techniques, such as attention mechanisms and feature importance analysis, can help build trust and facilitate adoption among domain experts.
Federated Learning: To address data privacy and security concerns, companies can employ federated learning approaches, where LLMs are trained on decentralized data sources without the need for data sharing or centralization.
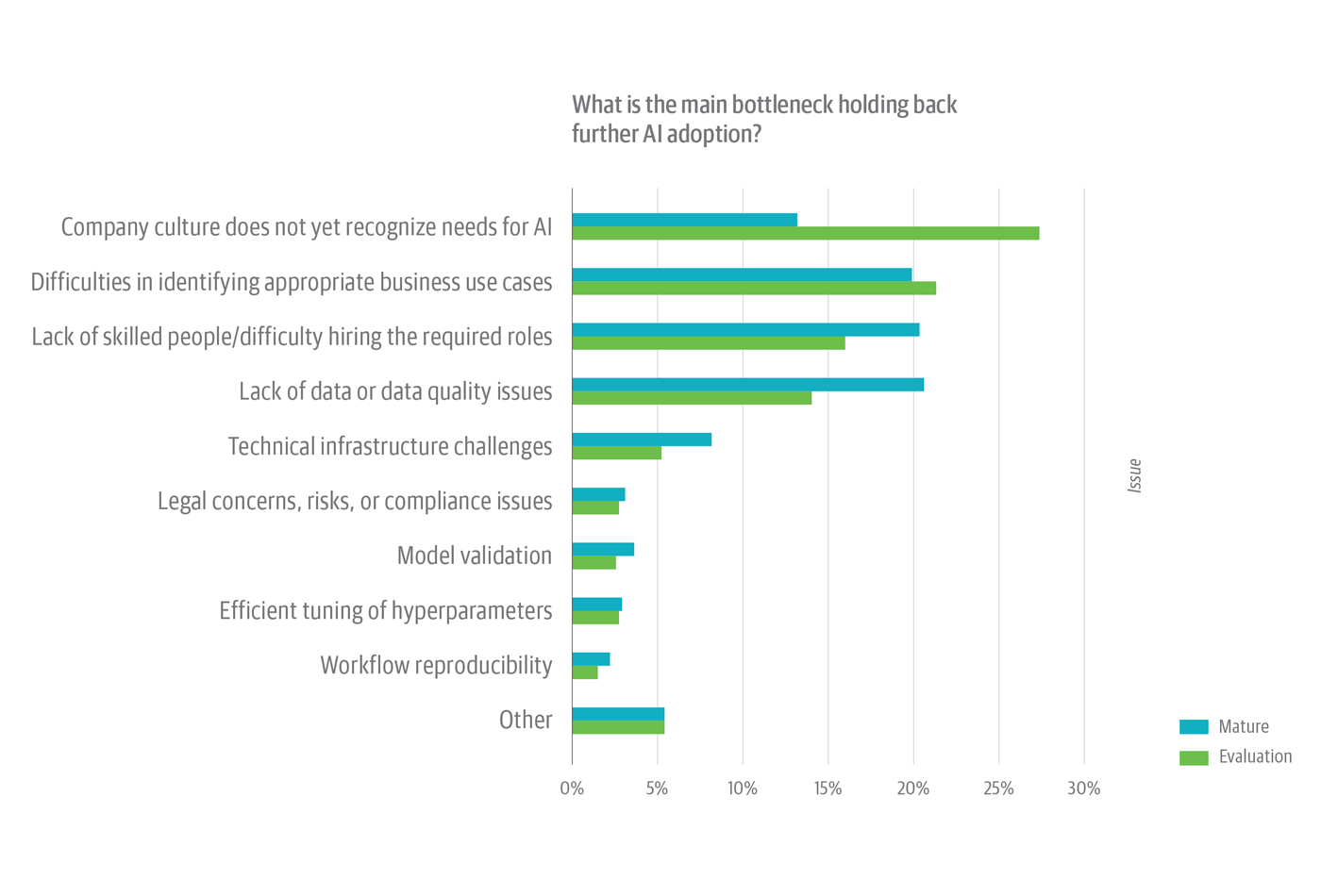
The Role of Business Leaders in Driving LLM Adoption and Digital Transformation
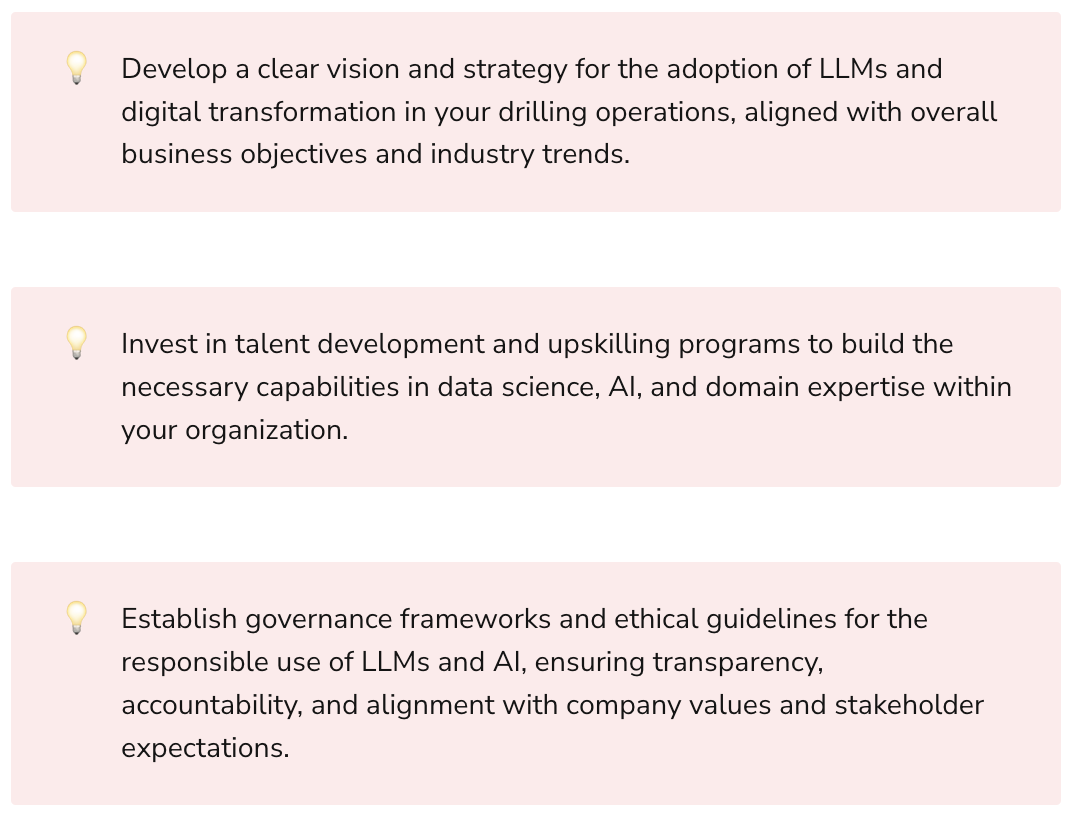
As the oil and gas industry undergoes a digital transformation, business leaders play a crucial role in driving the adoption of LLMs and other advanced technologies for predictive maintenance and beyond. To ensure successful implementation and long-term value creation, leaders should:
- Align predictive maintenance initiatives with overall business strategy and objectives
- Foster a culture of innovation, experimentation, and continuous improvement
- Invest in talent development and upskilling to build the necessary capabilities in data science, AI, and domain expertise
- Establish governance frameworks and ethical guidelines for the responsible use of LLMs and AI
- Collaborate with technology partners, industry peers, and academic institutions to stay at the forefront of emerging trends and best practices
"As business leaders, we have a responsibility to embrace the power of LLMs and AI to transform our operations, enhance our competitiveness, and create sustainable value for all stakeholders. By investing in talent, fostering innovation, and collaborating with experts, we can unlock the full potential of predictive maintenance and build a more resilient, efficient, and sustainable future for the oil and gas industry."
Conclusion
LLM-powered predictive maintenance represents a game-changing opportunity for optimizing drilling operations in the oil and gas industry. By harnessing the power of advanced AI and data analytics, companies can predict and prevent equipment failures, reduce downtime, lower maintenance costs, and improve safety and operational efficiency.
To successfully implement LLMs for predictive maintenance, companies need to focus on data quality, model selection and training, integration with existing systems, and collaboration between domain experts and data scientists. By staying at the forefront of emerging trends and techniques, such as multi-modal models, transfer learning, and explainable AI, companies can continue to push the boundaries of what is possible with predictive maintenance.
Ultimately, the adoption of LLMs and digital transformation in drilling operations requires strong leadership, vision, and commitment from business leaders. By embracing these technologies and investing in the necessary capabilities, oil and gas companies can position themselves for long-term success in an increasingly competitive and dynamic industry landscape.
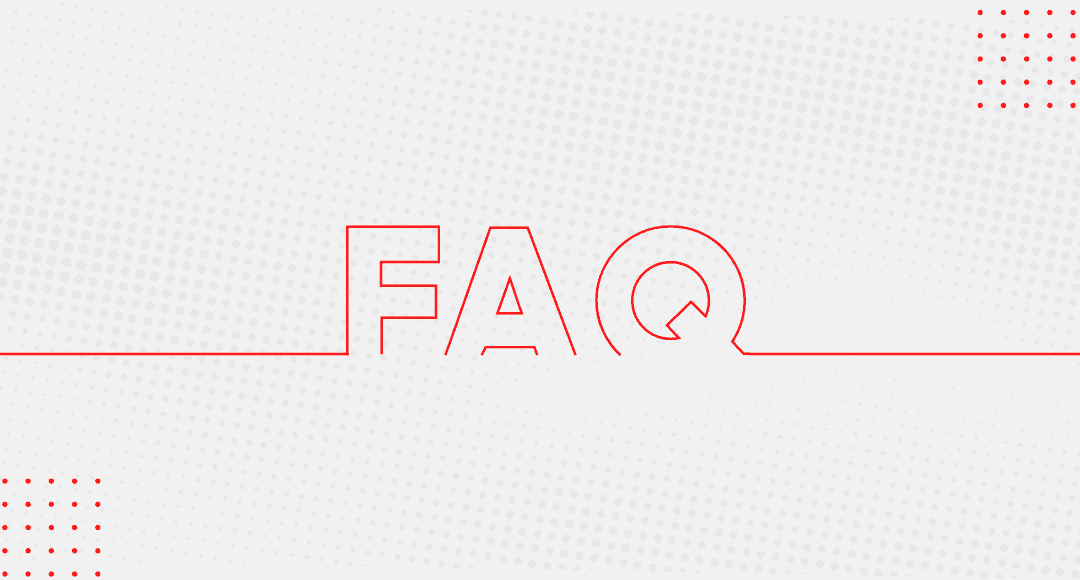
Q1: What is predictive maintenance, and how does it differ from reactive and preventive maintenance?
A1: Predictive maintenance is a proactive approach that uses data analytics and machine learning to predict equipment failures before they occur, allowing for timely interventions. Unlike reactive maintenance, which fixes problems after they happen, or preventive maintenance, which follows a fixed schedule, predictive maintenance optimizes maintenance based on the actual condition of the equipment.
Q2: How can large language models (LLMs) be applied to predictive maintenance in drilling operations?
A2: LLMs can process and analyze vast amounts of textual data, such as maintenance logs, sensor readings, and operator notes, to identify patterns and anomalies that indicate potential equipment failures. By learning from historical data and real-time inputs, LLMs can predict failures, estimate remaining useful life, and optimize maintenance schedules.
Q3: What are the key benefits of implementing LLM-powered predictive maintenance in drilling operations?
A3: The main benefits include reduced unplanned downtime, improved equipment reliability, lower maintenance costs, enhanced safety, and increased operational efficiency. By predicting and preventing failures, LLM-powered predictive maintenance helps drilling companies minimize disruptions, extend equipment life, and optimize resource allocation.
Q4: What kind of data is required for LLM-powered predictive maintenance, and how is it collected?
A4: LLM-powered predictive maintenance relies on diverse data sources, such as sensor readings (e.g., pressure, temperature, vibration), maintenance logs, operator notes, and design documents. This data is collected through various means, including IoT sensors, SCADA systems, and manual inputs, and is stored in centralized data repositories for analysis.
Q5: How do LLMs handle the challenges of data quality and availability in predictive maintenance?
A5: LLMs can be trained on incomplete or noisy data using techniques like data augmentation, transfer learning, and unsupervised pre-training. These approaches help LLMs learn robust representations and generalize to new scenarios, even with limited or imperfect data. Additionally, data preprocessing and quality control measures ensure that the input data is reliable and consistent.
Q6: What are some real-world examples of companies successfully implementing LLM-powered predictive maintenance in drilling operations?
A6: Shell, Equinor, and Schlumberger are among the leading oil and gas companies that have deployed LLM-powered predictive maintenance solutions. These companies have reported significant improvements in uptime, cost savings, and operational efficiency by incorporating AI and machine learning for failure prediction and maintenance optimization.
Q7: How can LLM-powered predictive maintenance be integrated with existing drilling workflows and systems?
A7: LLM-powered predictive maintenance can be integrated with existing systems, such as SCADA, EAM, and CMMS, through APIs, data pipelines, and middleware solutions. This integration enables seamless data flow, real-time monitoring, and actionable insights for maintenance teams and decision-makers, without disrupting current processes.
Q8: What are the key considerations for selecting and training LLMs for predictive maintenance in drilling operations?
A8: When selecting LLMs for predictive maintenance, consider factors such as model architecture (e.g., Transformer, LSTM), pre-training data, computational requirements, and explainability. Training LLMs involves data preparation, hyperparameter tuning, and performance evaluation using relevant metrics (e.g., precision, recall, F1 score). Collaboration between domain experts and data scientists is crucial for successful model development and deployment.
Q9: How can businesses ensure the responsible and ethical use of LLMs in predictive maintenance?
A9: Businesses should establish clear guidelines and governance frameworks for the ethical use of LLMs, addressing aspects such as data privacy, security, fairness, and transparency. This includes implementing data protection measures, conducting regular audits, and providing explanations for model predictions. Engaging stakeholders and fostering a culture of responsible AI are also essential.
Q10: What is the future outlook for LLM-powered predictive maintenance in drilling operations?
A10: The future of LLM-powered predictive maintenance looks promising, with the potential for increased adoption, integration with other technologies (e.g., IoT, digital twins), and the development of self-learning and adaptive models. As the technology matures, we can expect to see fully autonomous and optimized drilling operations, driven by cognitive AI systems and seamless integration of predictive maintenance into end-to-end workflows.
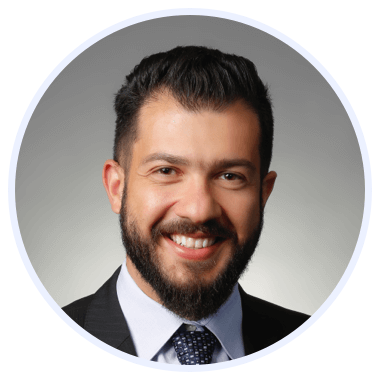
Rasheed Rabata
Is a solution and ROI-driven CTO, consultant, and system integrator with experience in deploying data integrations, Data Hubs, Master Data Management, Data Quality, and Data Warehousing solutions. He has a passion for solving complex data problems. His career experience showcases his drive to deliver software and timely solutions for business needs.