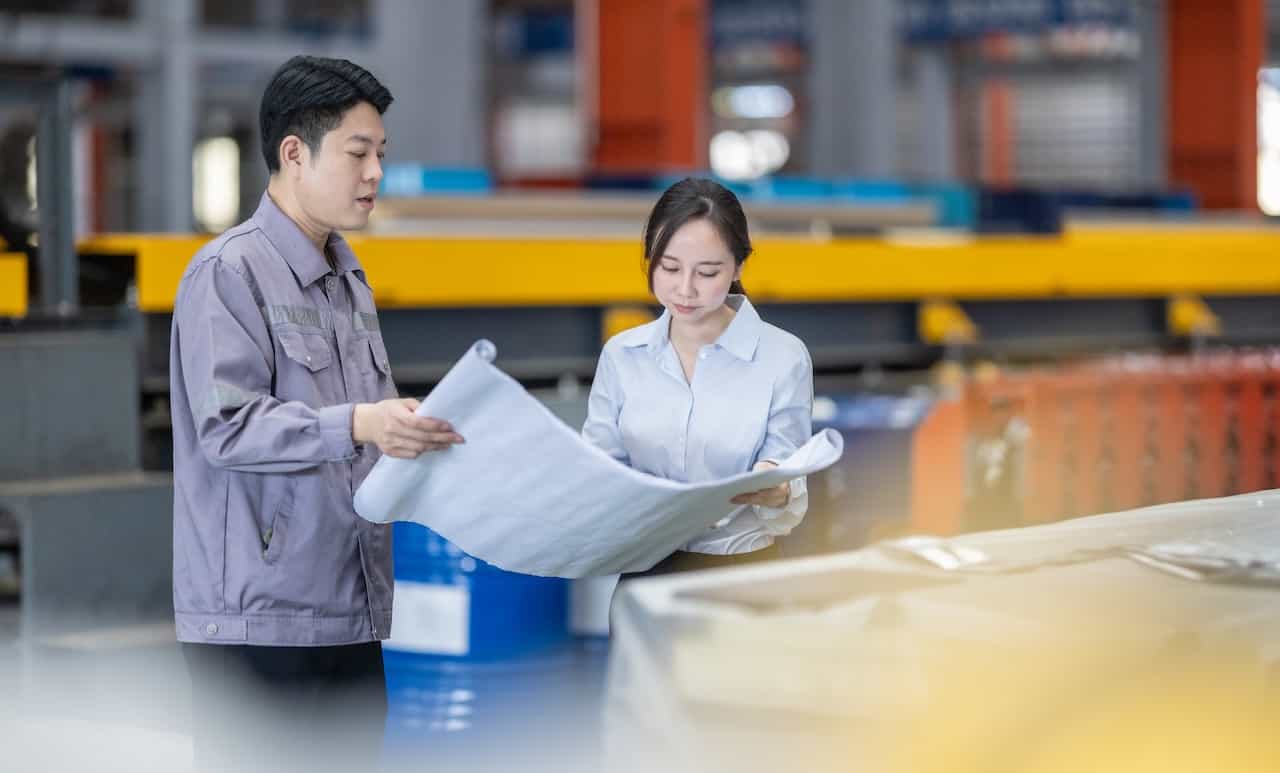
Walking through a manufacturing plant, I watched a maintenance technician flip through a massive binder of equipment manuals. The pages were dog-eared, some sections were highlighted, and sticky notes poked out from various spots. He was troubleshooting an issue with a CNC machine, but first had to find the right documentation. Time ticked by as production stood still.
This scene plays out countless times across manufacturing floors. We've modernized our equipment, upgraded our control systems, and automated various processes. Yet somehow, our critical production documentation remains trapped in the analog world of paper binders and PDF files scattered across shared drives. The inefficiency is striking, but more importantly, it's costing us time, money, and competitive advantage.
Over the past decade working with manufacturing operations, I've seen firsthand how digitizing production documentation can transform daily operations. But this isn't just about converting paper to PDFs – it's about making our documentation intelligent, accessible, and actually useful to the people who need it most.
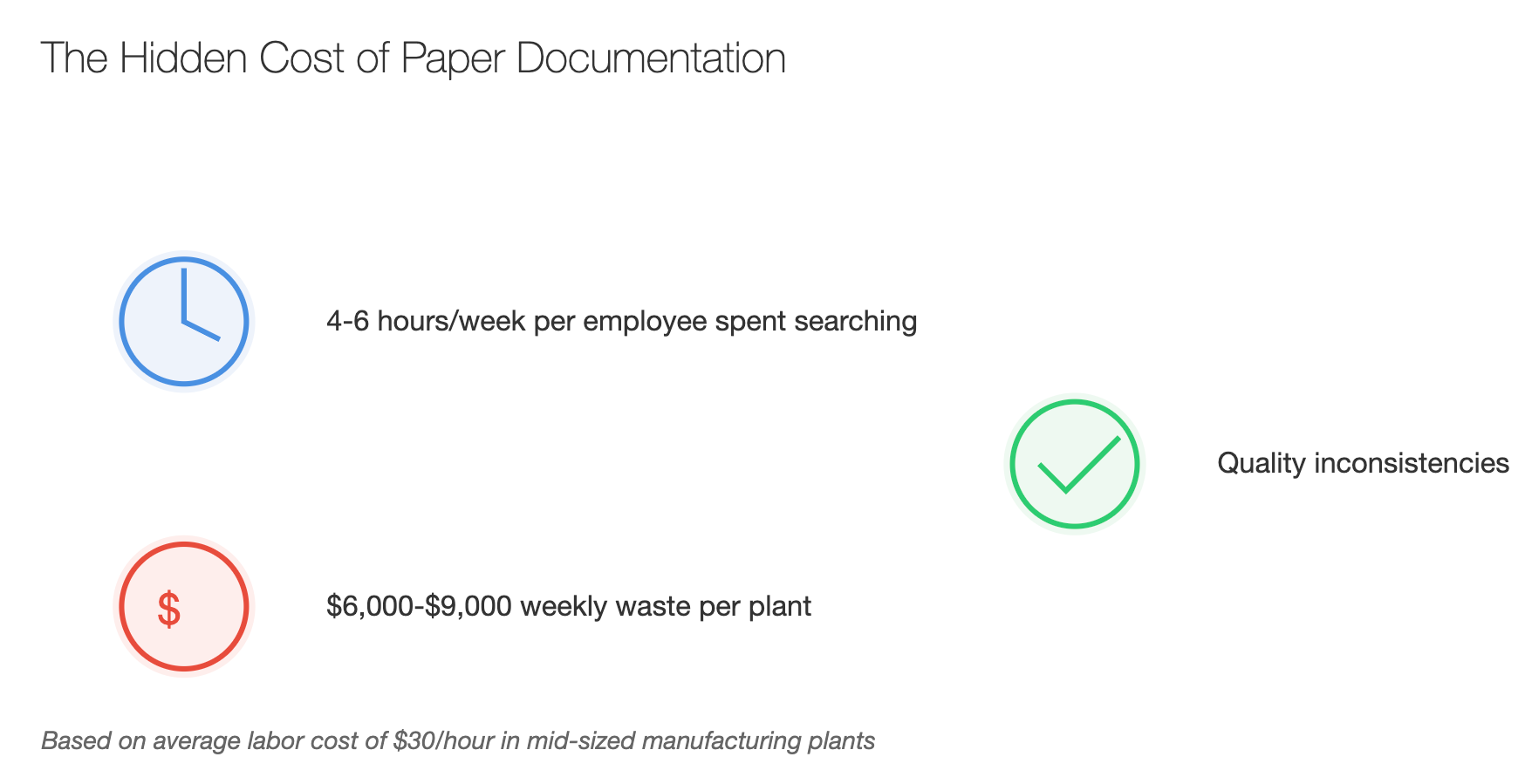
The Hidden Cost of Paper
The problems with paper-based documentation run deeper than just storage and accessibility. When production instructions live in binders, tribal knowledge gets lost between shifts. New employees struggle to find the information they need. Updates become a logistical nightmare – you either have multiple versions floating around or spend hours manually replacing pages across every binder.
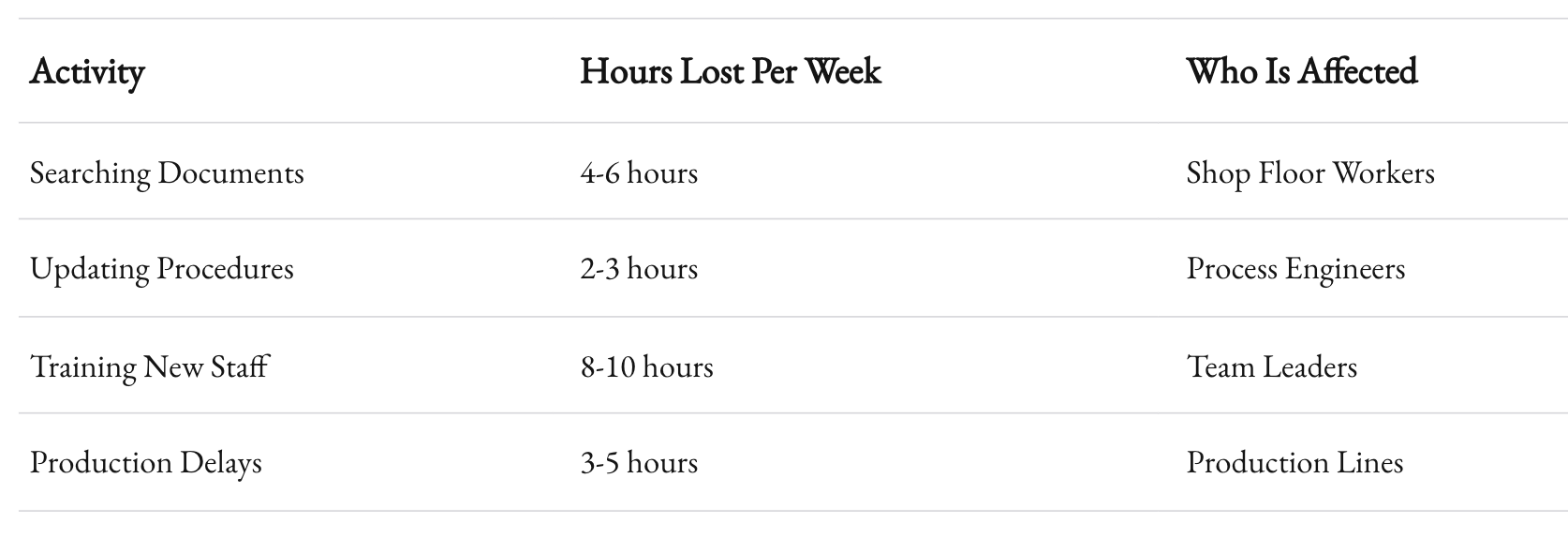
Consider the real financial impact. A typical manufacturer spends 4-6 hours per week per employee searching for the right information. For a mid-sized plant with 50 shop floor workers, that's 200-300 hours of lost productivity every week. At an average labor cost of $30 per hour, you're looking at $6,000-$9,000 in weekly waste – just from inefficient document management.
But the costs compound further. Production delays from waiting for documentation or following outdated procedures. Quality issues from inconsistent work instructions. Safety incidents from inaccessible maintenance procedures. The paper trail leads straight to your bottom line.
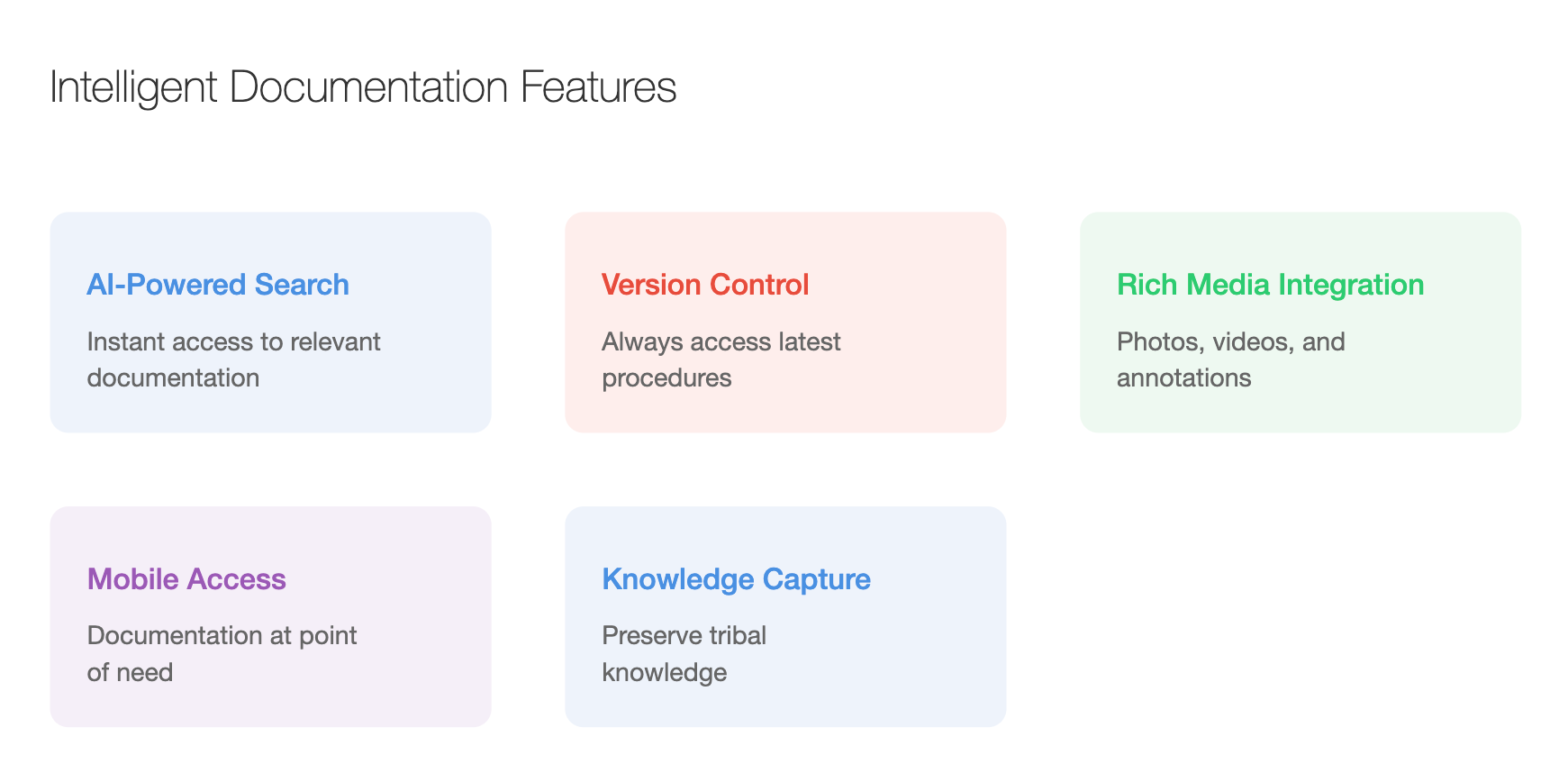
Beyond Simple Digitization
The solution isn't just scanning everything into PDFs. I've seen too many companies make this mistake – they digitize their documents but maintain the same linear, static format. The result? The same problems, just in digital form.
True transformation comes from making your documentation intelligent and interactive. Modern document management systems powered by AI can:
- Index every word of your documentation and make it instantly searchable
- Link related procedures and reference materials automatically
- Track document versions and ensure everyone accesses the latest procedures
- Embed rich media like photos and videos to enhance understanding
- Generate dynamic work instructions based on specific contexts
- Capture tribal knowledge through integrated commenting and annotation
- Provide mobile access to documentation right at the point of need
Let me share a recent example. One of our clients, a precision parts manufacturer, implemented an AI-powered documentation system last year. Their maintenance team now uses tablets to scan QR codes on equipment, instantly pulling up relevant manuals, maintenance histories, and troubleshooting guides. What used to take 15-20 minutes of searching through binders now takes seconds.
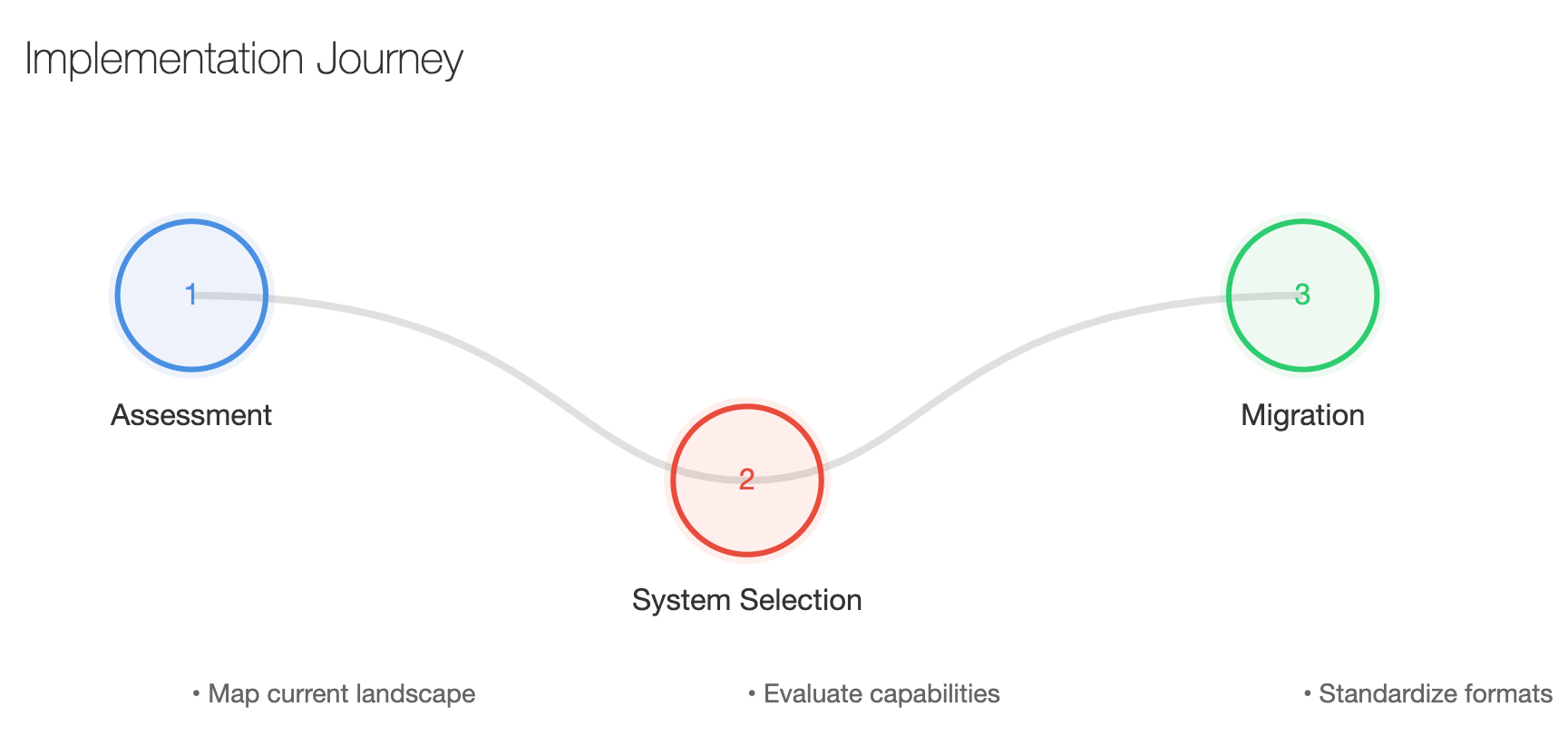
The Implementation Journey
Successfully digitizing production documentation requires careful planning and execution. Here's the framework I recommend to clients:
1. Document Assessment and Organization
Start by mapping your current documentation landscape:
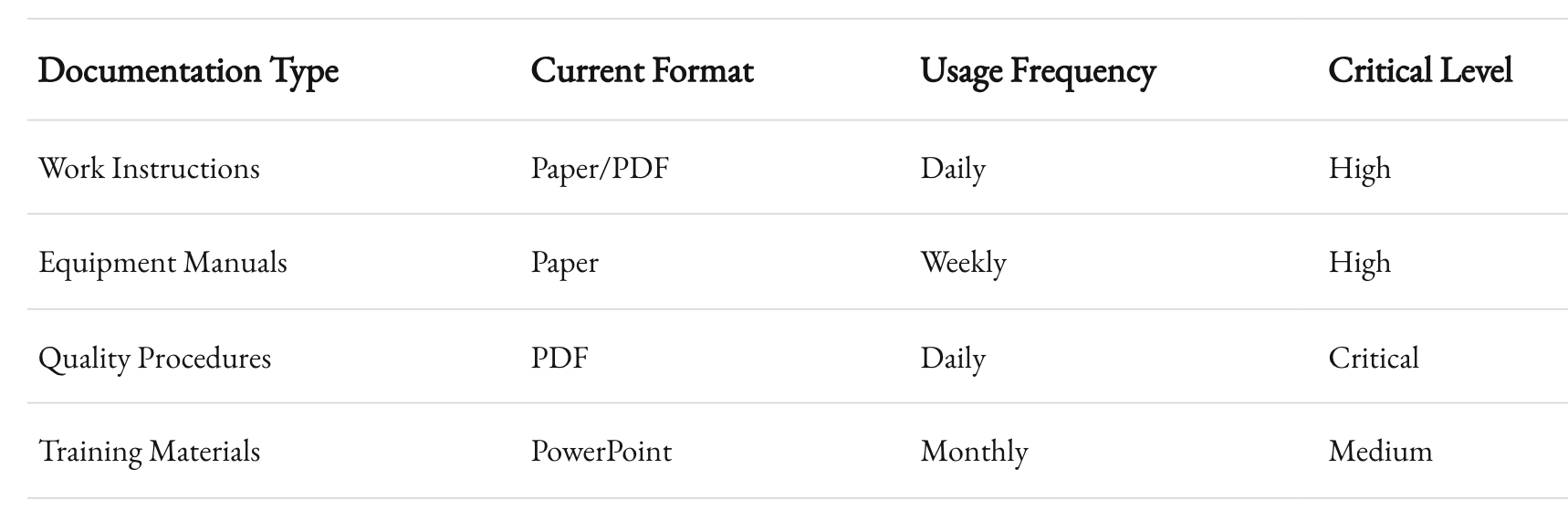
This assessment helps prioritize what to digitize first and identify gaps in your current documentation.
2. System Selection
Choose a documentation management system that balances functionality with usability. Key capabilities should include:
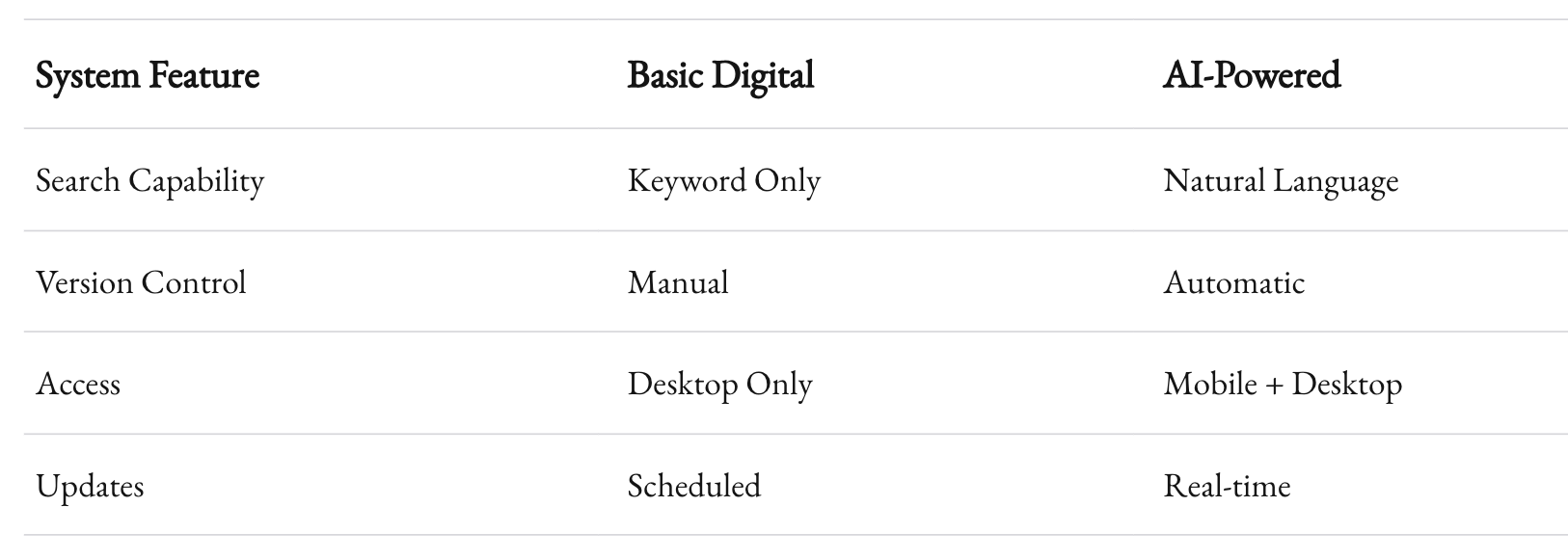
Strong search functionality with natural language processing
Version control and change management
Mobile accessibility and offline capabilities
Integration with existing systems (ERP, MES, CMMS)
Role-based access control
Annotation and collaboration features
Don't just evaluate the technology – consider the vendor's manufacturing industry expertise and implementation support.
3. Content Migration
This is where many projects stumble. Successful migration requires:
Clean-up of existing documentation to remove outdated content
Standardization of formats and templates
Metadata tagging for improved searchability
Quality control to ensure accuracy of migrated content
Preservation of critical tribal knowledge during digitization
Take time to properly structure your digital documentation. It will pay dividends in usability and adoption.
Driving Adoption
Even the best digital documentation system fails if people don't use it. Change management is crucial. Some effective strategies I've seen:
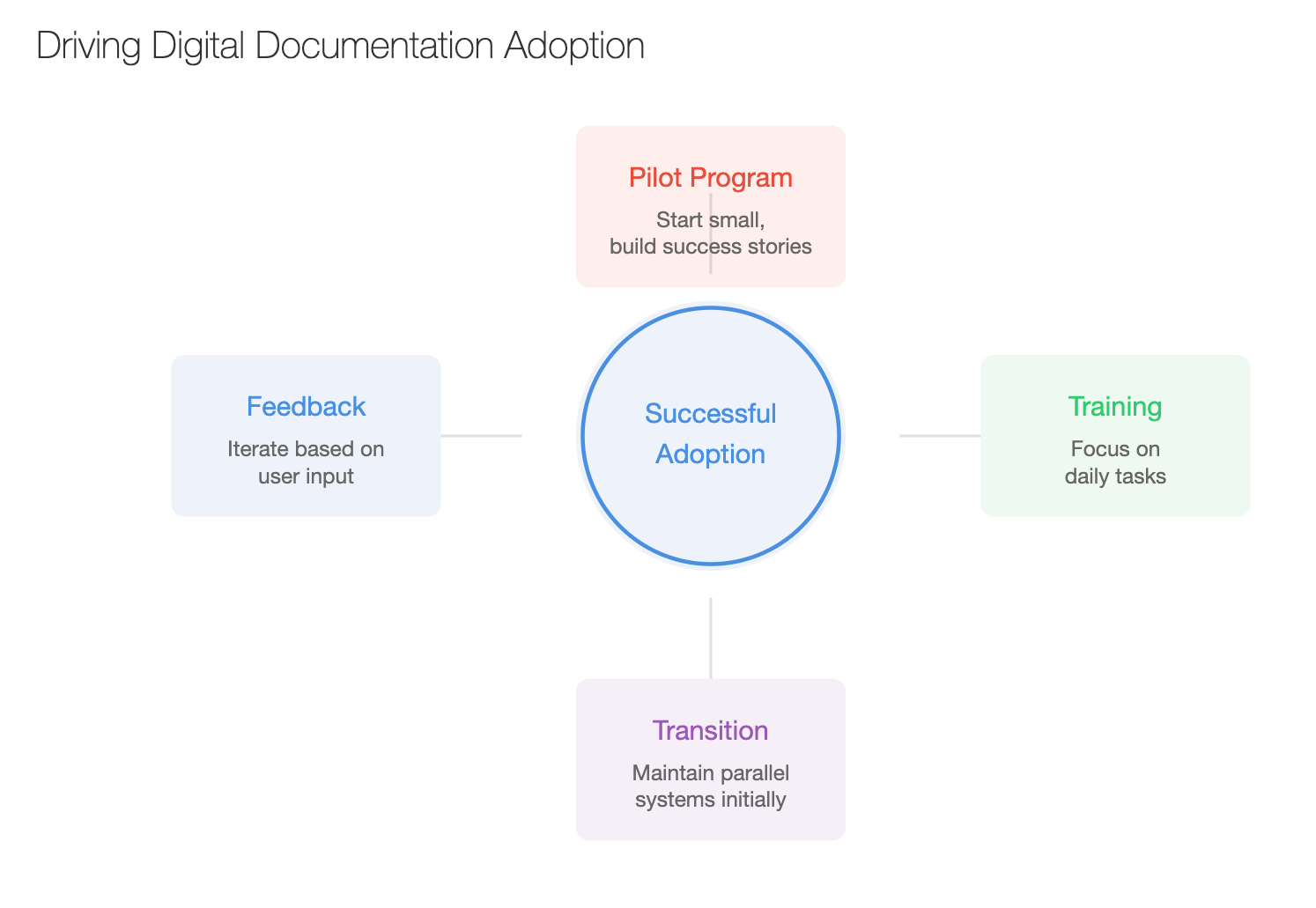
Start with a pilot area or department to work out issues and build success stories. Shop floor champions are invaluable for driving adoption among their peers.
Provide hands-on training focused on daily tasks. Show people how the new system makes their jobs easier, don't just lecture about features.
Maintain some parallel systems initially. While you want to move away from paper, a hard cutoff can be disruptive and risky.
Get feedback and iterate. Your first implementation won't be perfect. Create channels for users to report issues and suggest improvements.
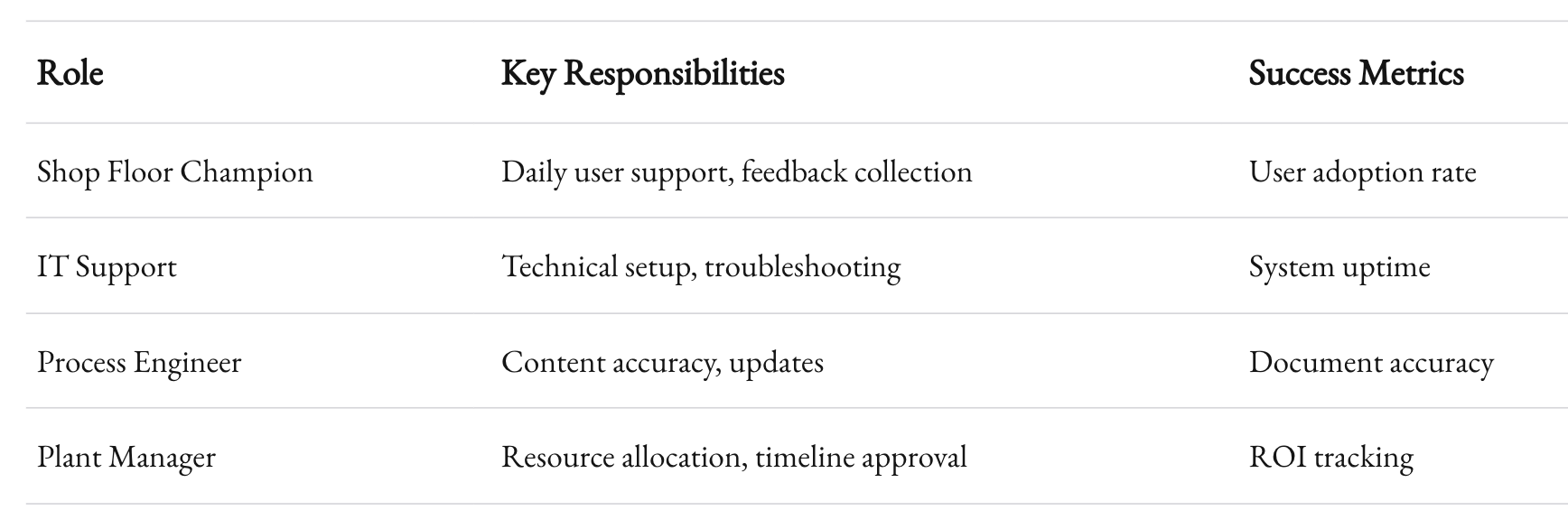
The Path Forward
Digital transformation of production documentation isn't a one-time project – it's an ongoing journey. As technology evolves, new capabilities emerge. AI and machine learning will make documentation even more intelligent and predictive. Augmented reality may change how we interact with procedures and manuals.
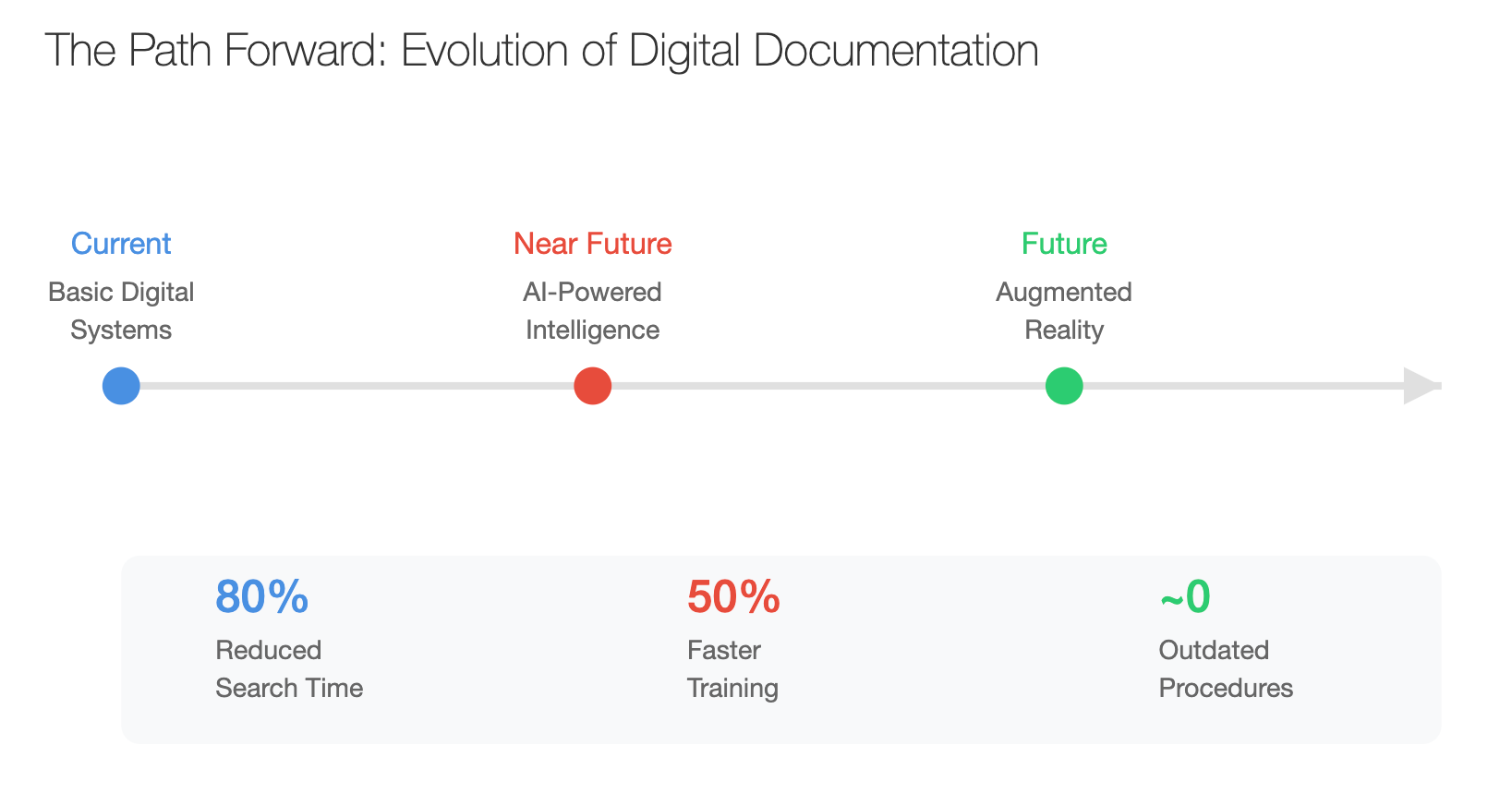
But the fundamental goal remains the same: getting the right information to the right people at the right time. When we achieve that, we reduce waste, improve quality, and empower our workforce to perform at their best.
I've seen companies cut document search time by 80%, reduce training time for new employees by 50%, and virtually eliminate issues from outdated procedures. The potential impact is massive, but it requires commitment and proper execution.
Start small if needed, but start moving your production documentation into the digital age. Your competition already is. If you'd like to discuss specific strategies for your operation, feel free to connect with me on LinkedIn.
The future of manufacturing is digital. Make sure your documentation keeps pace.
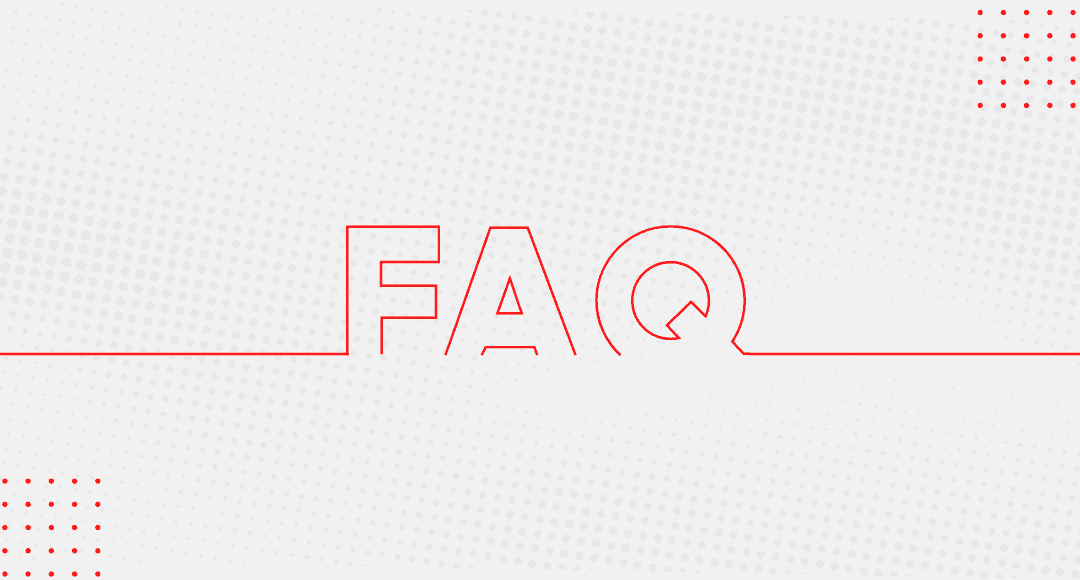
Q1: How long does it typically take to digitize all production documentation?
The timeline varies significantly based on your documentation volume and complexity. For a mid-sized manufacturing plant, expect 3-4 months for critical documentation and up to a year for complete transformation. Rather than attempting everything at once, start with high-impact documents like daily work instructions and maintenance procedures. This approach allows you to demonstrate value quickly while refining your digitization process.
Q2: We tried digitizing our documents before, but people kept reverting to paper. What's different now?
Previous digitization efforts often failed because they simply converted paper into PDFs without adding real value. Modern systems offer contextual search, mobile access, and intelligent linking between documents. The key difference is that today's solutions actually make work easier for users. When a maintenance technician can scan a QR code and instantly access relevant procedures on their tablet, the digital version becomes the path of least resistance.
Q3: Our workforce isn't very tech-savvy. Won't this create more problems than it solves?
This is a common concern, but I've found that user adoption depends more on system design than technical expertise. The key is choosing an interface that mirrors familiar paper-based workflows while adding clear benefits. For instance, if your current process involves checking a binder for work instructions, the digital version should require no more than 2-3 taps to access the same information. Good training and on-floor support during the first few weeks are crucial.
Q4: What's the actual ROI of digitizing production documentation?
Most manufacturers see ROI within 6-8 months of implementation. The returns come from multiple areas: reduced search time (typically 80% reduction), fewer errors from outdated procedures (30-40% reduction), faster training for new employees (40-50% time savings), and improved audit compliance. One client saved over $200,000 annually just by eliminating production delays caused by missing or outdated documentation.
Q5: How do we ensure documentation stays updated in the digital system?
This requires a combination of technology and process. The system should automatically track versions, notify relevant people of needed updates, and maintain an audit trail of changes. However, you also need clear ownership and review cycles. I recommend assigning document owners who receive automated reminders for periodic reviews. The system can also flag documents that haven't been accessed or updated within a certain timeframe.
Q6: What about cybersecurity? Isn't paper safer?
While paper seems secure, it's actually more vulnerable to loss, damage, and unauthorized copying. Digital systems offer controlled access, detailed audit trails, and encrypted storage. They also enable rapid disaster recovery - try replicating thousands of paper documents after a flood or fire. The key is choosing a system with robust security features and working with your IT team to ensure proper integration with your existing security infrastructure.
Q7: We operate in a highly regulated industry. How do we maintain compliance when going digital?
Digital systems often improve compliance by providing better document control and audit trails. Look for solutions that offer features like electronic signatures, change tracking, and automated version control. Many systems are specifically designed to meet requirements for ISO, FDA, and other regulatory frameworks. During implementation, involve your quality team early to ensure all compliance requirements are mapped to system capabilities.
Q8: What's the best way to handle legacy documents that are still relevant but poorly organized?
Start with a thorough audit of your legacy documentation. Create a simple matrix ranking documents by current relevance and usage frequency. High-relevance, high-usage documents should be fully rebuilt in the new system. For moderately relevant documents, basic digitization with good metadata tagging might suffice. Some legacy documents might be archived or discarded entirely. The goal is to be selective and strategic rather than digitizing everything.
Q9: How do we integrate digital documentation with our existing systems (ERP, MES, etc.)?
Integration capabilities should be a key factor in selecting your documentation system. Modern platforms offer APIs and standard connectors for common manufacturing systems. Start by mapping critical workflows where documentation intersects with other systems. For instance, linking maintenance procedures directly to work orders in your CMMS. Work with vendors who have experience integrating with your specific systems and can demonstrate successful implementations.
Q10: What happens if the system goes down? Won't this stop production?
A robust digital documentation system should have offline capabilities and redundancy built in. Critical documents can be cached on local devices for offline access. Consider maintaining backup devices with offline copies of essential procedures. However, system reliability is generally high - most platforms maintain 99.9% uptime. The occasional brief system outage typically causes far less disruption than the constant inefficiencies of paper-based systems.
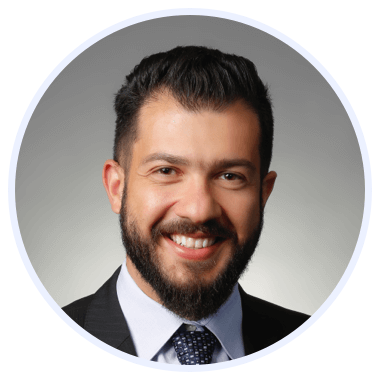
Rasheed Rabata
Is a solution and ROI-driven CTO, consultant, and system integrator with experience in deploying data integrations, Data Hubs, Master Data Management, Data Quality, and Data Warehousing solutions. He has a passion for solving complex data problems. His career experience showcases his drive to deliver software and timely solutions for business needs.