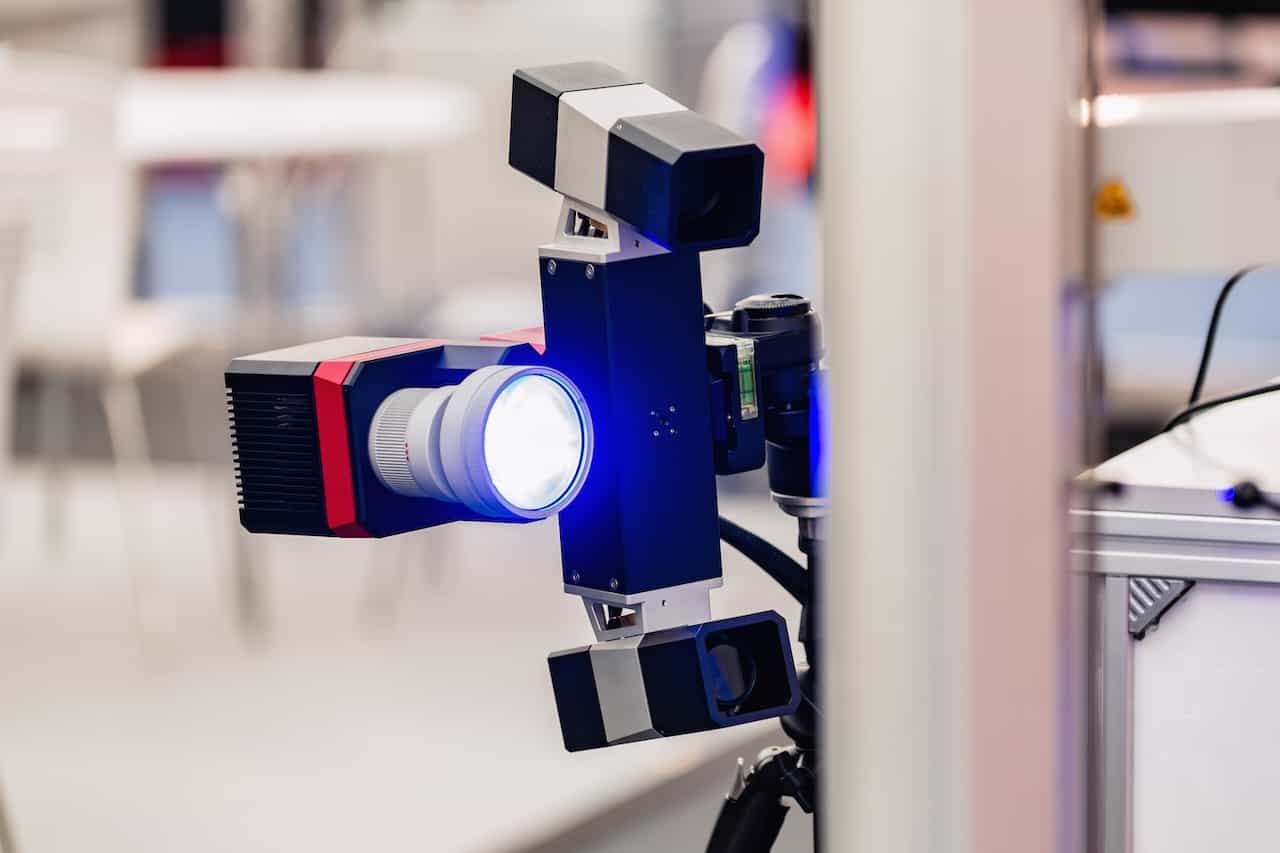
After spending years helping manufacturing companies optimize their operations, one truth stands out: quality control is the backbone of manufacturing excellence. I've walked factory floors where skilled inspectors scrutinized parts with practiced eyes, making split-second decisions that determined whether products met specifications. Their expertise is invaluable. But even the most experienced quality control specialist can't maintain the same level of attention across three shifts, seven days a week.
This challenge hit home during a recent project with a precision components manufacturer. Their quality control team was burning out from the sheer volume of inspections needed. Despite their best efforts, inconsistencies crept in during late shifts and high-pressure periods. The cost of missed defects was mounting, both in terms of rework and customer satisfaction.
Here's the thing about quality control - it's not just about catching defects. It's about understanding patterns, predicting issues before they become problems, and maintaining unwavering consistency. This is where automated detection through machine vision and AI enters the picture, not to replace human expertise, but to augment it in powerful ways.
The Hidden Costs of Manual Inspection
Traditional quality control relies heavily on human visual inspection. While experienced QC specialists bring invaluable expertise to the table, they also face inherent limitations. Fatigue sets in after hours of detailed inspection. Environmental factors like lighting variations can affect judgment. Even the most skilled inspector might have slightly different standards than their colleagues.
I've seen these limitations translate into real costs for manufacturers. One mid-sized automotive parts supplier was spending over $300,000 annually on rework and customer returns due to quality issues that slipped through manual inspection. Beyond the direct costs, their team was constantly fighting fires - rushing to investigate customer complaints, running extra production cycles to replace rejected parts, and struggling to maintain their quality certification standards.
The business impact extends beyond immediate finanal losses. Inconsistent quality control erodes customer trust, makes production planning more difficult, and creates unnecessary stress for everyone involved in the manufacturing process.
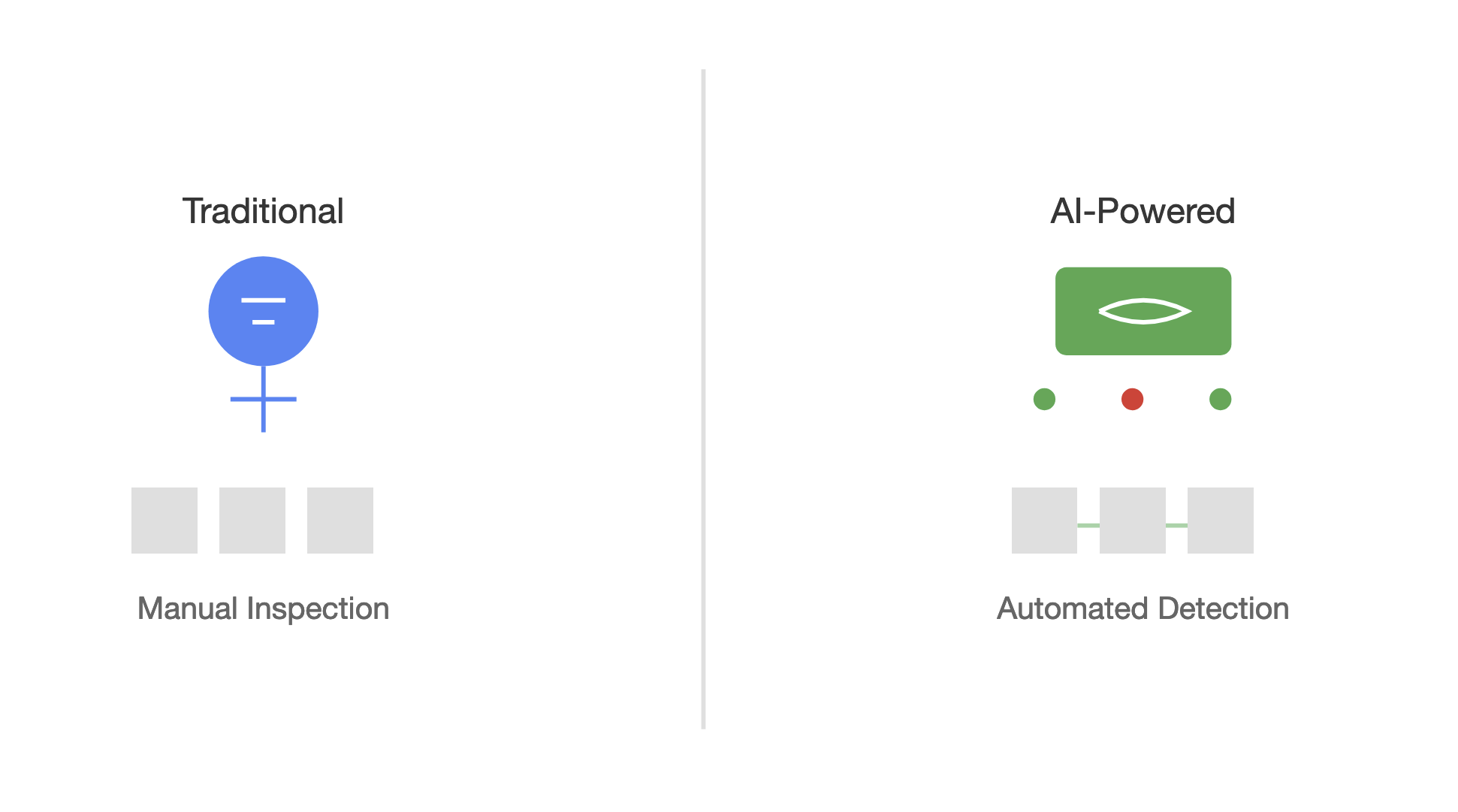
The Evolution of Automated Detection
Modern automated detection systems have come a long way from the simple pass/fail measurements of early machine vision. Today's systems combine high-resolution imaging with sophisticated AI algorithms that can learn and adapt to new scenarios. They can detect subtle variations that might escape the human eye and maintain consistent standards 24/7.
Let me break down the key components that make this possible:
- Advanced Imaging Hardware
- High-speed cameras capable of capturing microscopic details
- Multi-angle lighting systems that ensure consistent illumination
- Precision positioning equipment for reliable image capture
- Intelligent Software Systems
- Deep learning algorithms trained on thousands of product images
- Real-time analysis capabilities for instant quality decisions
- Adaptive systems that can handle product variations
- Integration Capabilities
- Seamless connection with production line controls
- Data logging for traceability and analysis
- Integration with quality management systems
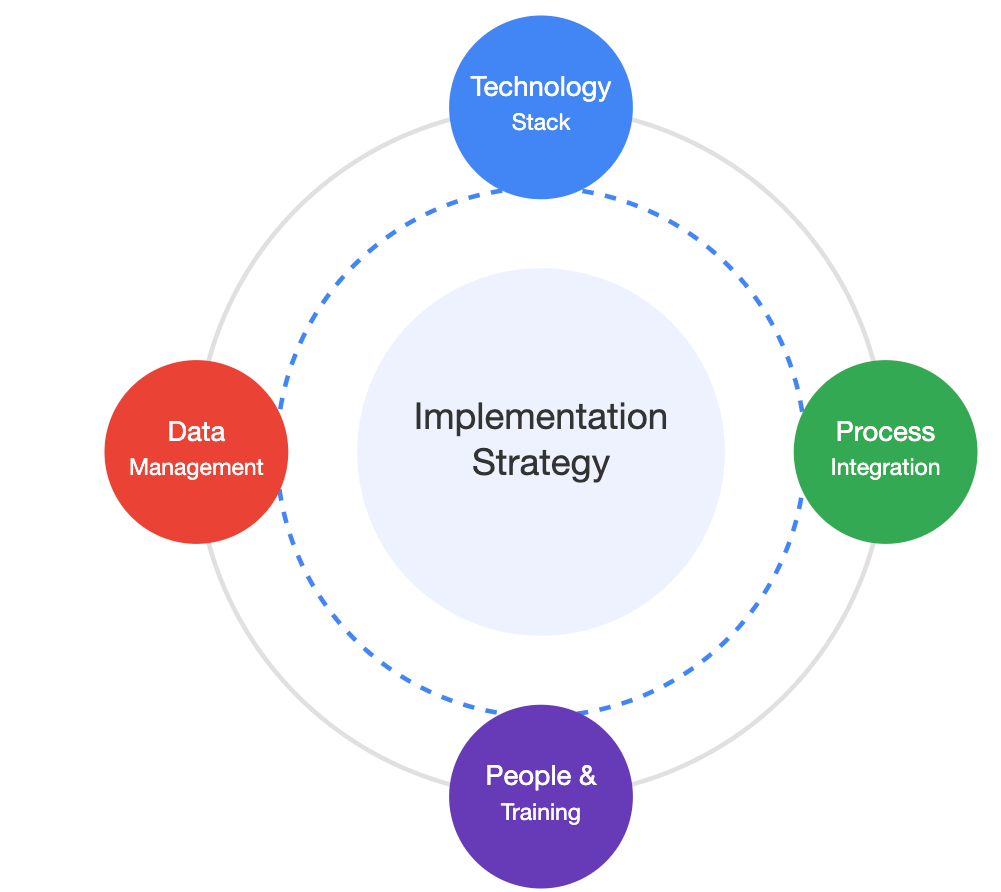
Real-World Implementation Strategies
Successfully implementing automated detection requires more than just installing cameras and software. It demands a systematic approach that considers your specific manufacturing environment and quality requirements.
The first step is identifying the critical inspection points in your production process. These are areas where quality issues are most likely to occur or where defects would have the highest impact on product quality. For instance, in precision machining, this might include checking critical dimensions immediately after CNC operations.
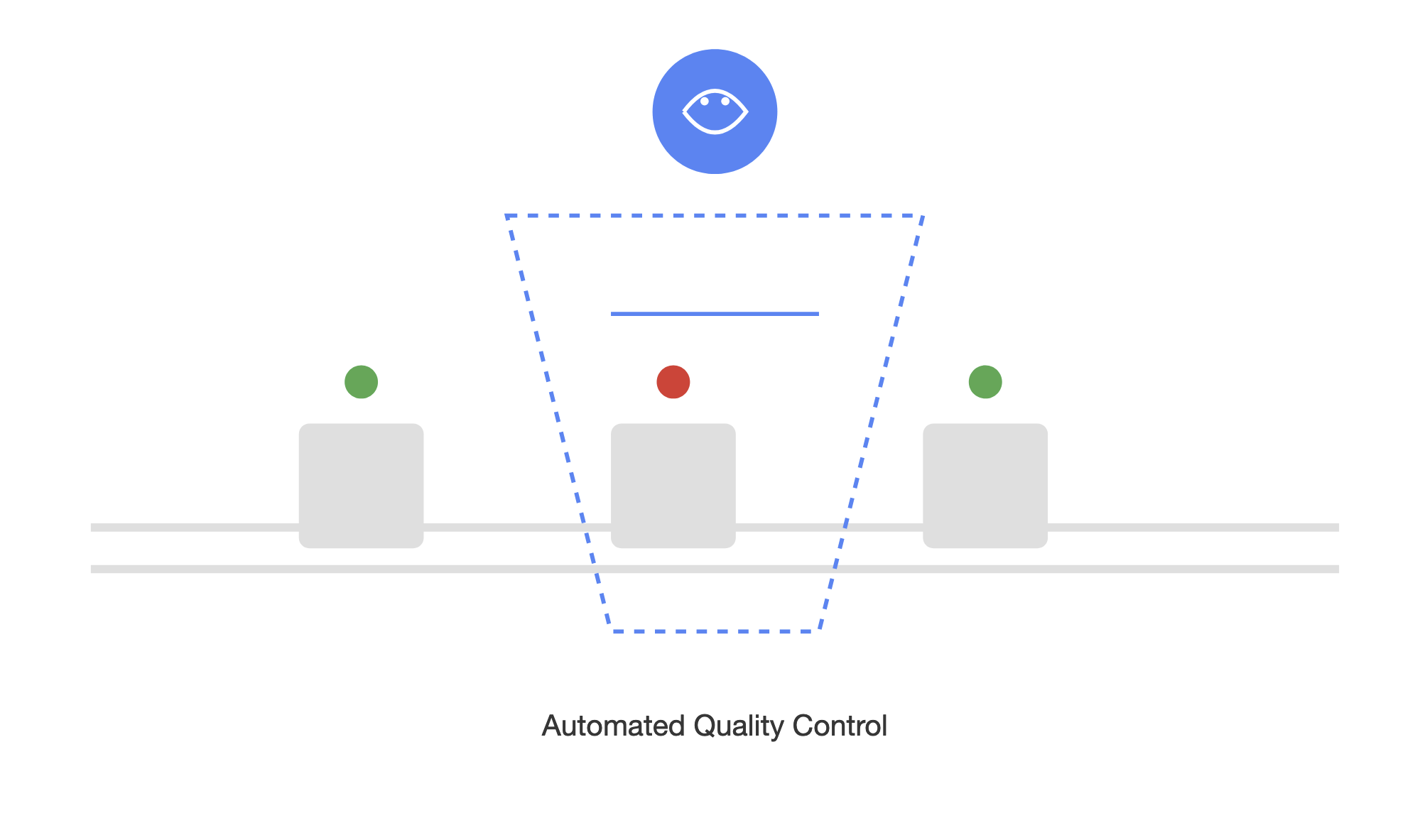
Next comes the process of teaching the system what to look for. This involves:
- Collecting a comprehensive dataset of both good and defective products
- Training the AI algorithms to recognize acceptable variations
- Fine-tuning detection parameters for optimal sensitivity
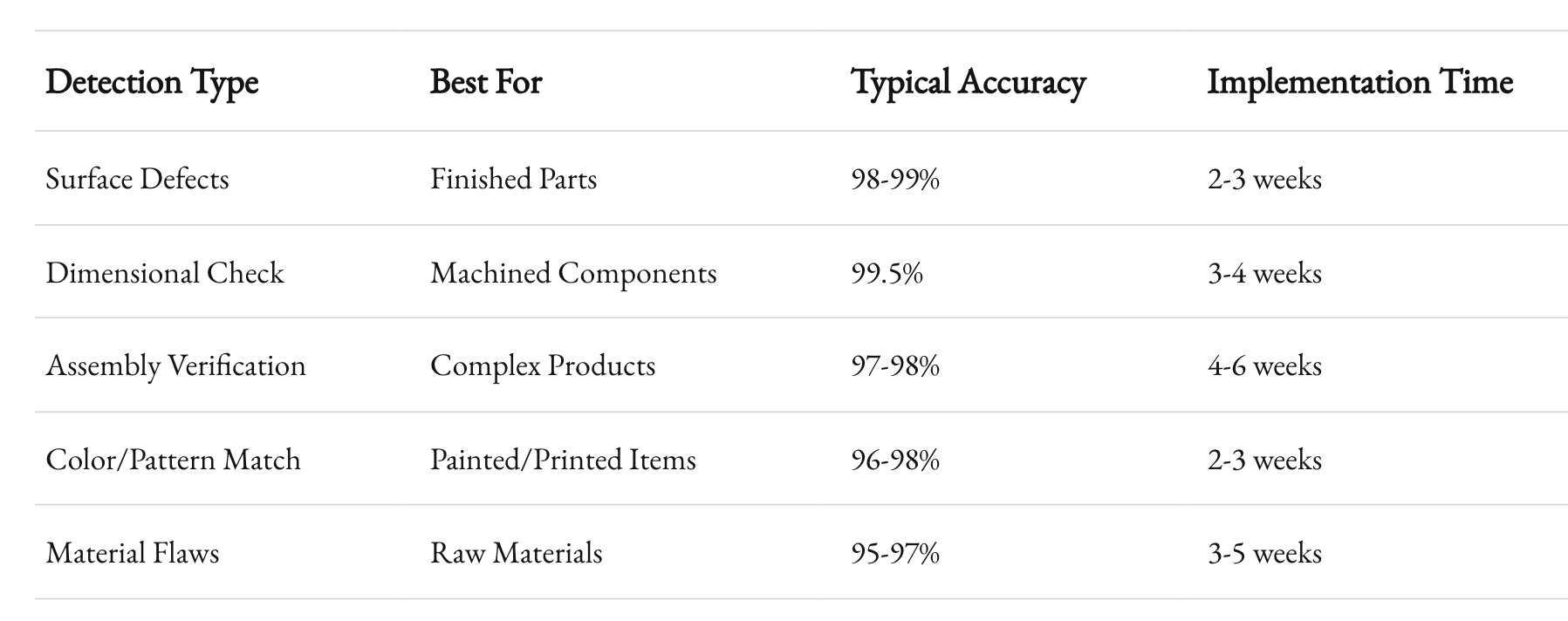
One crucial aspect often overlooked is change management. Your quality control team needs to understand that automation is there to support them, not replace them. Their expertise becomes even more valuable in analyzing trends, investigating root causes, and continuously improving the detection system.
Measuring Success
The impact of automated detection systems can be measured across multiple dimensions. Here's a typical breakdown of improvements I've observed:
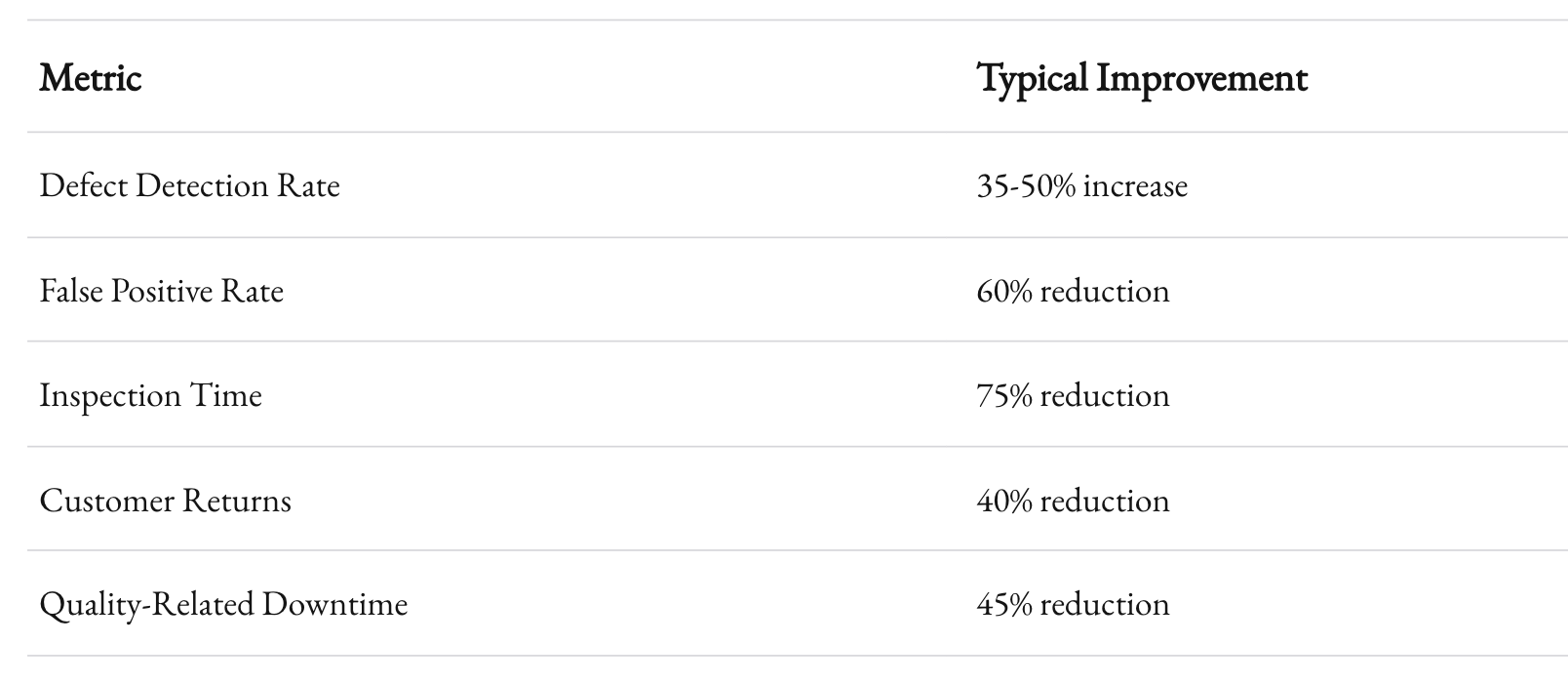
However, the real value often extends beyond these metrics. Automated detection provides consistency and traceability that were previously impossible to achieve. Every inspection is documented, creating a rich dataset that can drive continuous improvement.
Common Implementation Challenges
While the benefits of automated detection are clear, implementation isn't without its challenges. Here are some common hurdles I've helped companies overcome:
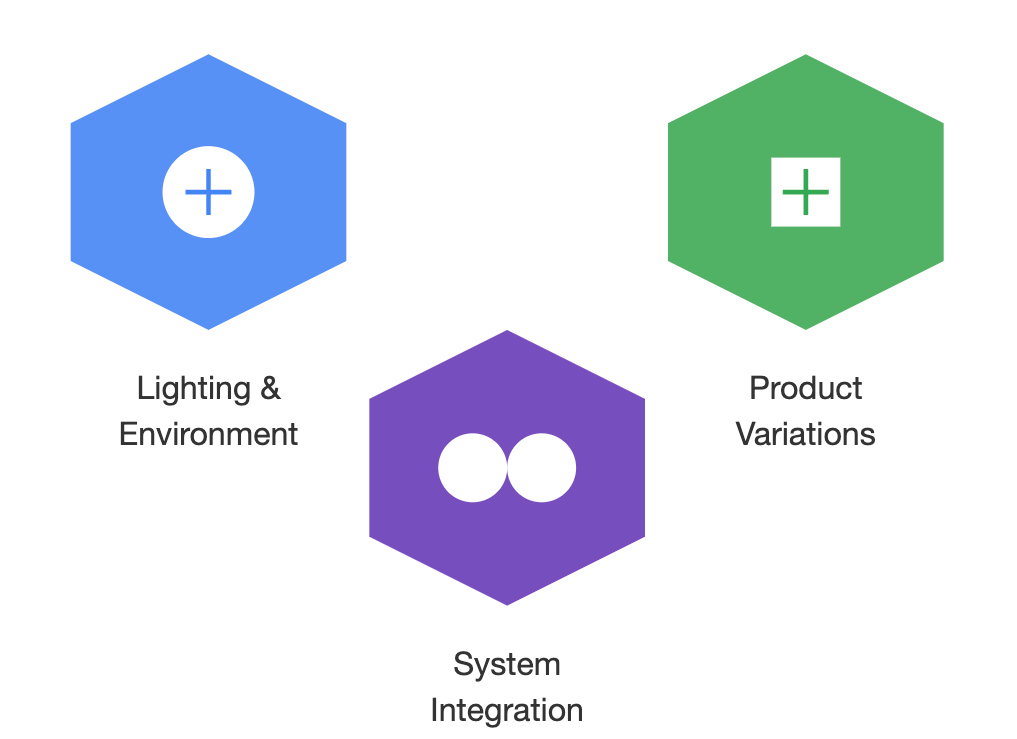
Lighting and Environmental Variables
Consistent lighting is crucial for reliable inspection. Even minor variations can affect image quality and detection accuracy. The solution often involves carefully designed lighting systems and regular calibration procedures.
Product Variations
Manufacturing processes naturally produce slight variations in products. The challenge is teaching the system to distinguish between acceptable variations and actual defects. This requires careful training and ongoing fine-tuning of detection parameters.
Integration with Existing Systems
Many factories have legacy equipment and systems that weren't designed with automation in mind. Creating seamless integration often requires creative solutions and careful planning to avoid disrupting existing operations.

Future Trends
The field of automated detection continues to evolve rapidly. Here are some emerging trends that I'm particularly excited about:
Adaptive Learning Systems
Newer AI systems can continuously learn from production data, becoming more accurate over time. They can adapt to new product variations and identify emerging quality issues before they become significant problems.
Advanced Analytics Integration
Quality control data is becoming increasingly valuable for overall process optimization. By analyzing patterns in defect data, manufacturers can identify root causes and prevent issues before they occur.
Collaborative Quality Control
The future of quality control lies in intelligent collaboration between automated systems and human experts. AI handles routine inspections and data analysis, while quality specialists focus on complex issues and process improvement.
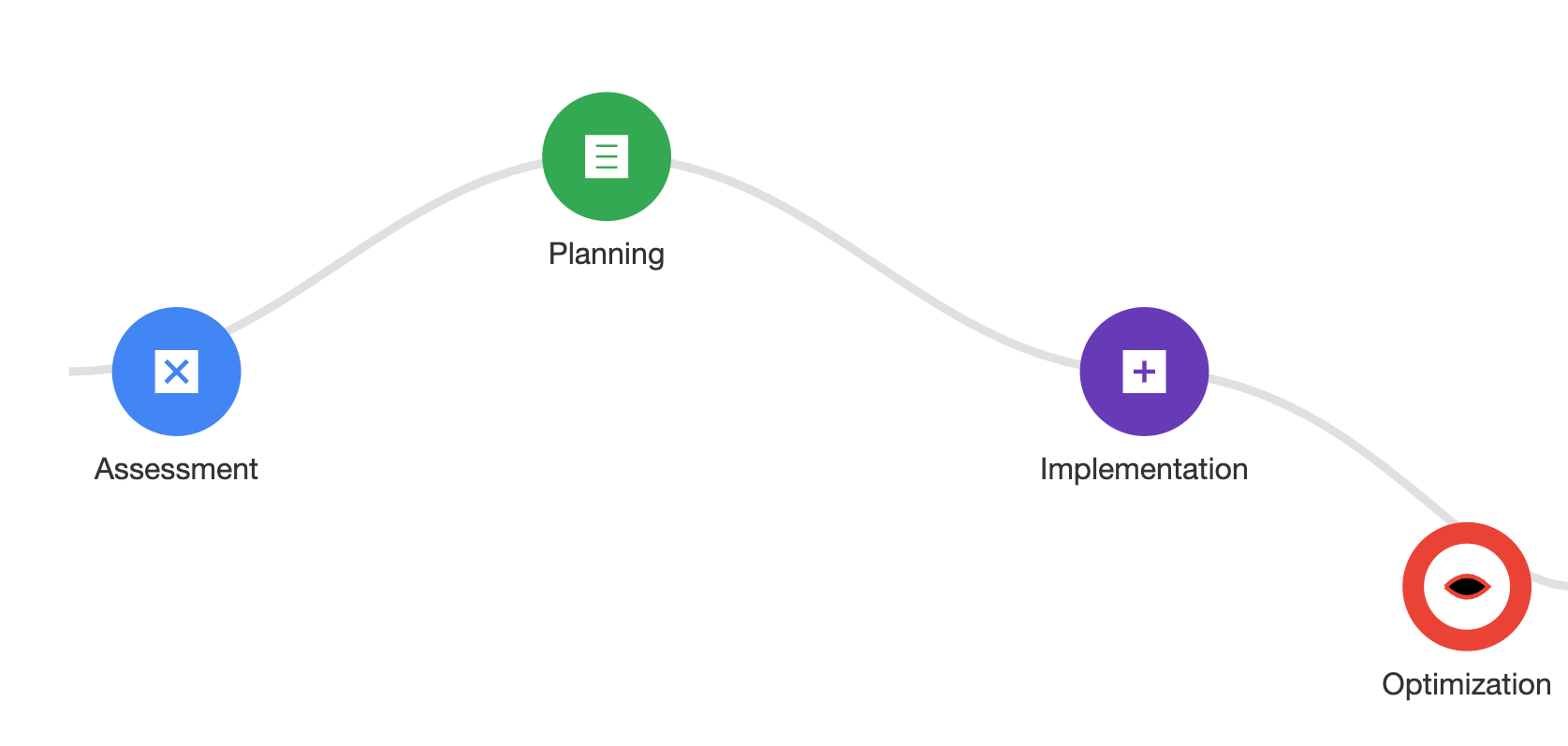
Getting Started
If you're considering implementing automated detection in your quality control process, here's a practical roadmap to get started:
- Assessment Phase
- Analyze current quality control processes
- Identify critical inspection points
- Document current defect rates and quality metrics
- Planning Phase
- Define specific quality requirements
- Evaluate technology options
- Develop implementation timeline
- Plan for training and change management
- Pilot Implementation
- Start with a single critical inspection point
- Collect and analyze results
- Refine parameters based on feedback
- Document lessons learned
- Full Deployment
- Roll out to additional inspection points
- Integrate with existing systems
- Train staff on new procedures
- Monitor and optimize performance
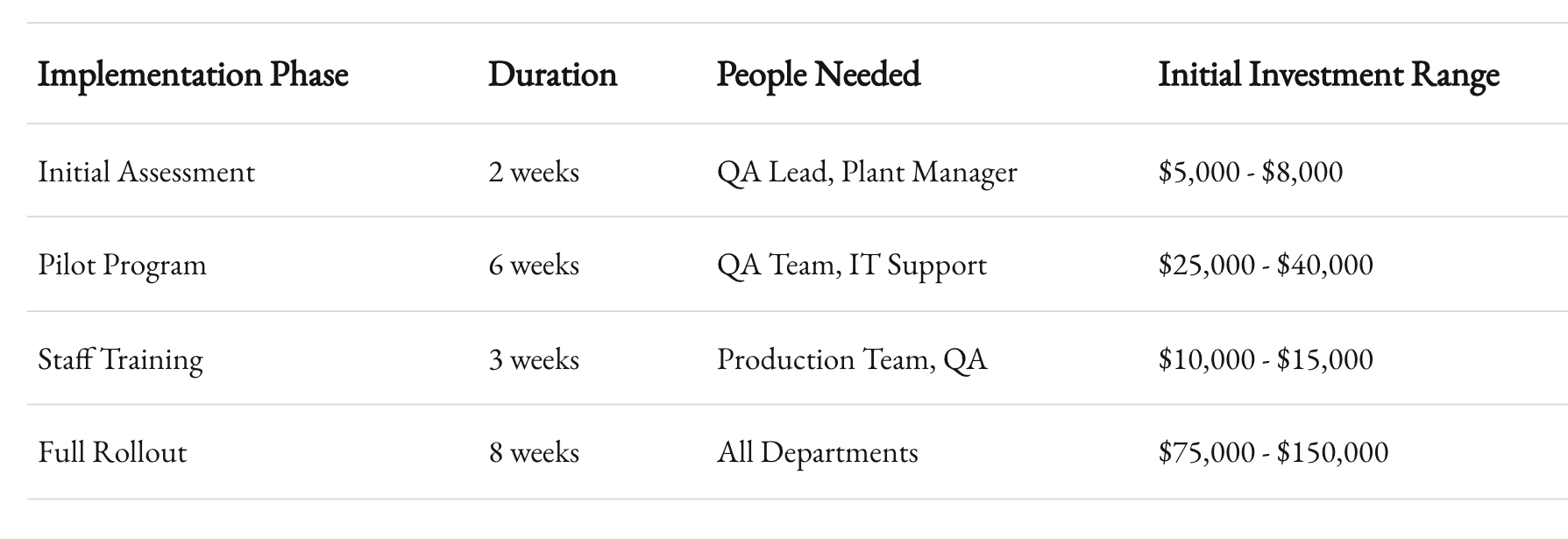
Quality control through automated detection represents a significant leap forward in manufacturing excellence. It's not just about replacing manual inspection with cameras and algorithms - it's about creating a more intelligent, data-driven approach to quality management.
The key to success lies in understanding that automation and human expertise are complementary forces. When properly implemented, automated detection frees your quality control team to focus on more strategic activities while ensuring consistent, reliable inspection around the clock.
As manufacturing continues to evolve, the role of automated detection will only grow more important. The manufacturers who embrace this technology today will be better positioned to meet the quality challenges of tomorrow.
If you're interested in exploring how automated detection could transform your quality control processes, let's connect. Together, we can develop a strategy that meets your specific needs and helps drive your manufacturing excellence forward.
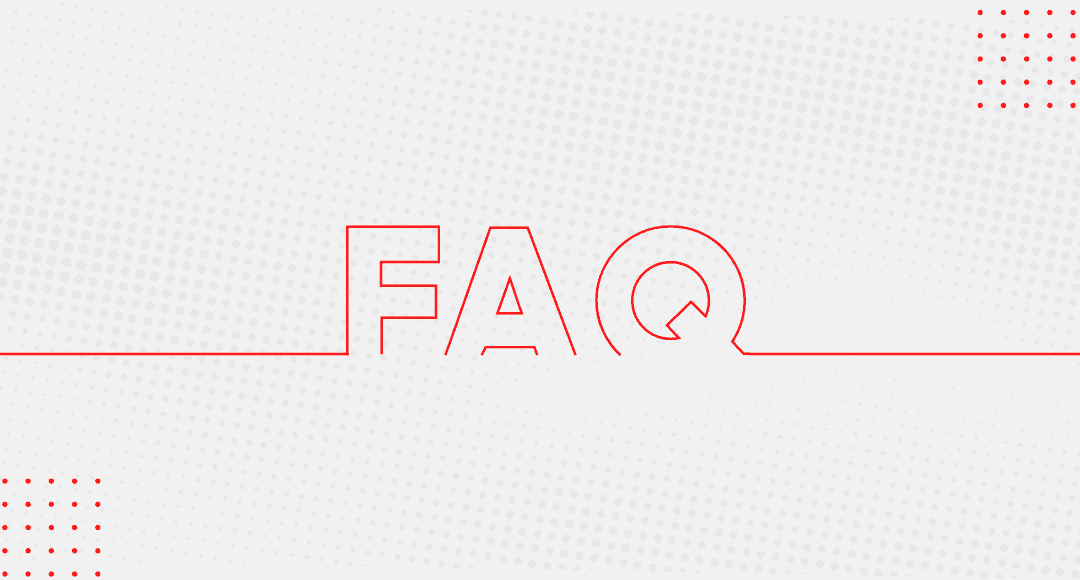
Q1: How do automated detection systems handle product variations that are technically within spec but look different?
The key lies in training the AI with a comprehensive dataset that includes all acceptable variations. Modern systems use what we call "tolerance bands" - essentially teaching the AI to recognize a range of acceptable appearances rather than looking for an exact match. I recently worked with a metal finishing company where we trained the system on hundreds of samples of acceptable surface finishes. The AI learned to distinguish between normal process variations and actual defects, reducing false rejections by 70%.
Q2: What's the realistic timeline for seeing ROI on an automated quality control system?
Most of our mid-sized manufacturing clients see initial ROI within 8-14 months. However, this timeline can vary significantly based on your current defect rates and production volume. A recent automotive parts client broke even in just 6 months because their high production volume meant that even a small reduction in defect rates translated to substantial savings. The key is to start with high-impact inspection points where defects are most costly or frequent.
Q3: How do you maintain quality control when the automated system needs maintenance or updates?
This requires a hybrid approach. We always recommend maintaining a backup manual inspection protocol, but more importantly, implementing a rolling update schedule. For instance, in a multi-camera setup, you can update systems one at a time while others remain operational. Modern systems also maintain a "fallback mode" where they can continue basic inspections even during updates, only requiring manual verification for edge cases.
Q4: Can automated systems really detect subtle defects as well as experienced human inspectors?
In many cases, they can detect even more subtle defects. Modern vision systems can spot variations down to microns, operating consistently across all shifts. However, the real power comes from combining AI detection with human expertise. I've seen cases where the AI flags subtle patterns that even experienced inspectors missed, leading to early detection of tool wear or process drift.
Q5: What kind of training do our existing QC staff need to operate these systems?
Typically, we're looking at 20-30 hours of initial training for operators and 40-50 hours for QC leads. The focus isn't just on operating the system but understanding how to interpret results and make adjustments. The good news is that most staff adapt quickly because modern interfaces are quite intuitive. The deeper training comes in understanding how to fine-tune detection parameters and analyze trend data.
Q6: How do automated systems handle changes in product specifications or new product introductions?
Modern AI-based systems are remarkably adaptable. The key is having a good "recipe management" system where inspection parameters for different products are stored and can be quickly loaded. Training the system on new products typically takes 2-3 days, including collecting sample images and validating detection accuracy. The system can often learn from existing similar products, shortening the training time.
Q7: What about the costs we don't see upfront - maintenance, updates, calibration?
Annual maintenance typically runs 8-12% of the initial system cost. This includes software updates, calibration services, and preventive maintenance. However, these costs are offset by reduced labor needs and fewer quality-related incidents. I recommend building a 3-year TCO (Total Cost of Ownership) model that includes training, maintenance, and potential upgrades. This gives a more realistic picture of the investment required.
Q8: How do these systems handle environmental variables like changing light conditions or vibration?
Environmental control is crucial for consistent inspection. Modern systems use a combination of controlled lighting environments and adaptive algorithms. For instance, we recently installed a system that automatically adjusts its detection thresholds based on ambient light levels. For vibration, we use a combination of physical dampening and image stabilization algorithms. The key is identifying these variables during the initial assessment phase.
Q9: Can the system be integrated with our existing ERP and quality management systems?
Yes, most modern quality control systems offer standard APIs for integration. The level of integration can range from basic data export to real-time synchronization. We typically start with basic integration - sharing inspection results and production counts - and gradually expand to more sophisticated interactions like automated production adjustments based on quality trends. The key is having a clear integration roadmap based on your specific needs.
Q10: What's the biggest mistake companies make when implementing automated quality control?
The biggest mistake is treating it as purely a technology project rather than a process improvement initiative. Success requires engaging your quality team early, understanding their current processes, and incorporating their expertise into the system setup. I've seen companies rush to install the technology without this groundwork, leading to resistance from staff and suboptimal results. The most successful implementations start with a clear understanding of current processes and pain points, then build the technical solution around these insights.
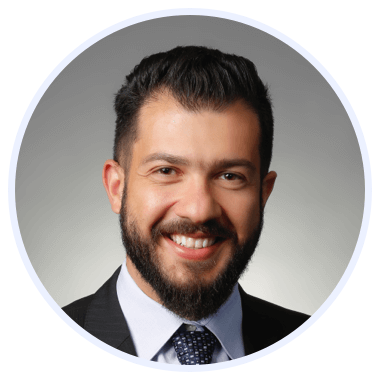
Rasheed Rabata
Is a solution and ROI-driven CTO, consultant, and system integrator with experience in deploying data integrations, Data Hubs, Master Data Management, Data Quality, and Data Warehousing solutions. He has a passion for solving complex data problems. His career experience showcases his drive to deliver software and timely solutions for business needs.